Appendix E
Processing Techniques and Available Classes of Armor Ceramics
This appendix covers additional material and details relevant to Chapter 5 of this report. These pages address several topics related to processes used in the manufacturing of ceramics for armors and include discussions on potential armor materials such as functionally graded materials, biomimetics, foams, smart sensors, and phononic band gap materials.
Some of the key manufacturing processes, together with their advantages and disadvantages, are listed in Table 5-1 of Chapter 5. Table E-1 presents the relevant properties of materials listed in Table 5-1 of Chapter 5.
PRESSURELESS SINTERING
The pressureless sintering process offers cost reduction through net shape processing using innovative powders and processing methods to obtain full density without the application of pressure. The goal of densification is to create strong bonds in the material and eliminate porosity so that theoretical densities, along with homogeneous microstructures, can be achieved for the sintered bodies. Residual porosity, along with the shape and size distributions of the pores and grains, influences the characteristics of dynamic performance. The low-cost alumina armor plates manufactured by means of uniaxial pressing, slip casting, and sintering are used in vehicle armor applications in large volumes. The typical cost of these plates runs about $2.50/lb to $10/lb for the finished tile. Solid state sintering is achieved by heating the “green” compact to the temperature that is in the range between approximately 50 and 80 percent of the melting temperature.1
At these temperatures the powder does not melt, but fusing of adjacent powder particles and reduction in the overall porosity occur by atomic diffusion in the solid state. Solid state sintering is typically used for pure, single-phase polycrystalline materials, such as α–Al2O3. For many covalently bonded polycrystalline ceramics, the required dense microstructure is hard to achieve using solid state sintering; therefore, additives are used to form a small amount of liquid phase between the particles at the sintering temperature. The liquid phase provides a high-diffusivity path to transport matter into the pores and facilitates densification. For example, hard-to-sinter silicon carbide (SiC) is processed as a liquid-phase sintered ceramic. The price of SiC tiles manufactured by means of a pressureless sintered process is in the range of $40/lb to $50/lb.
Solid- and liquid-state sintering processes are widely employed to densify refractory ceramics, but at much higher temperatures than required by the hot-pressing (HP) technique. Sintering of SiC was first performed by Prochazka,2 using boron and carbon as sintering aids to reduce the interfacial energy of the grains (boron),3 and by reacting the carbon with residual silica (carbon) present on the SiC particle surface.4,5Sintering of b-SiC is more difficult than sintering of α–SiC because of the b toα phase transformation at 1900°C to 2000°C, which generates voids between grains owing to the difference in the growth morphology of b and α grains.6 Several additives, such as Al–C, Al2O3–C, and Al2O3–Y2O3, have been tested as sintering aids for SiC powder to enhance the sintering rate and to reduce grain
______________
1Rahaman, M. 2007. Sintering of Ceramics. Boca Raton, Fla.: Taylor and Francis Group.
2Prochazka, S. 1974. Hot pressed silicon carbide. U.S. Patent 3,853,566, filed December 21, 1972, and issued December 10, 1974, to General Electric Company. Schenectady, NY.
3Maddrell, E. 1987. Pressureless sintering of silicon carbide. Journal of Materials Science Letters 6(4): 486-488.
4van Rijswijk, W., and D. Shanefield. 1990. Effects of carbon as a sintering aid in silicon carbide. Journal of the American Ceramic Society 73(1): 148-149.
5Hamminger, R. 1989. Carbon inclusions in sintered silicon carbide. Journal of the American Ceramic Society 72(9): 1741-1744.
6Williams, R., B. Juterbock, C. Peters, T. Whalen, and A. Heuer. 1984. Forming and sintering behavior of B- and C-doped α- and b-SiC. Journal of the American Ceramics Society 67(4): C62-C64.
TABLE E-1 Summary of Properties of Various Ceramics for Personnel Armor Application
|
||||||||||
Material |
Designation |
Density ρ (g/cc) |
Grain Size (μ) |
Young’s Modulus E (GPa) |
Flex Strength Σ (MPa) |
Fracture Toughness K (MPa-m1/2) |
Fracture Mode |
Hardness (HK-Knoop hardness, HV-Vickers hardness) |
HK 2 kg (kg/mm2) |
Areal Density |
|
||||||||||
Al2O3 |
CAP-3 |
3.90 |
— |
370 |
379 |
4-5 |
— |
1,440 (HK 1 kg) |
1,292 |
20.2 |
B4C |
Ceralloy-546 4E |
2.50 |
10-15 |
460 |
410 |
2.5 |
TG |
3,200 (HV 0.3 kg) |
2,066 |
13.0 |
Norbide |
2.51 |
10-15 |
440 |
425 |
3.1 |
TG |
2,800 (HK 0.1 kg) |
1,997 |
13.0 |
|
SiC |
SiC-N |
3.22 |
2-5 |
453 |
486 |
4.0 |
IG, TG |
— |
1,905 |
16.7 |
Ceralloy 146-3E |
3.20 |
— |
450 |
634 |
4.3 |
— |
2,300 (HV 0.3 kg) |
— |
16.6 |
|
Hexoloy |
3.13 |
3-50 |
410 |
380 |
4.6 |
TG |
2,800 (HK 0.1 kg) |
1,924 |
16.2 |
|
Purebide 5000 |
3.10 |
3-50 |
420 |
455 |
— |
TG |
— |
1,922 |
16.1 |
|
SC-DS |
3.15 |
3-50 |
410 |
480 |
3-4 |
— |
2,800 (HK 1 kg) |
— |
16.4 |
|
MCT SSS |
3.12 |
3-50 |
424 |
351 |
4.0 |
TG |
— |
1,969 |
16.2 |
|
MCT LPS |
3.24 |
1-3 |
425 |
372 |
5.7 |
IG |
— |
1,873 |
16.8 |
|
Ekasic-T |
3.25 |
1-3 |
453 |
612 |
6.4 |
IG |
— |
1,928 |
16.8 |
|
SiC (RB) |
SSC-702 |
3.02 |
45 |
359 |
260 |
4.0 |
TG |
1,757 (HK 0.5 kg) |
— |
15.7 |
SSC-802 |
3.03 |
45 |
380 |
260 |
4.0 |
TG |
— |
1,332 |
15.7 |
|
SSC-902 |
3.12 |
45 |
407 |
260 |
4.0 |
TG |
— |
1,536 |
16.2 |
|
SiC/B4C (RB) |
RBBC-751 |
2.56 |
45 |
390 |
271 |
5.0 |
TG+Ductile Si |
— |
1,626 |
13.3 |
TiB2 |
Ceralloy 225 |
4.5 |
— |
540 |
265 |
5.5 |
— |
— |
1,849 |
23.4 |
|
NOTE: Areal density in pounds per square foot (PSF): weight of a 12 × 12 × 1 in. panel in pounds; TG, transgranular fracture; IG, intergranular fracture.
SOURCES: CAP-3, SC DS: CoorsTek; Ceralloy, Ekasic-T: Ceradyne; Norbide, Hexoloy:Saint-Gobain; Purbide: Morgan AM&T; SiCN: Cercom (BAE); SSC, RBBC, BSC, SSS and LPS: M Cubed Technologies (MCT). Properties for other manufacturers’ materials are from their respective Web sites except for 2 kg Knoop hardness, grain size, and fracture mode.
growth. Aluminum (Al)7 and alumina8 with carbon promote silicon carbide sintering by means of a solid state mechanism at a temperature over 2000°C, while alumina and yttria lead to a high-density sintered sample by means of a liquid-phase mechanism at temperatures below 2000°C.9
Boron carbide (B4C) is mainly produced by the HP method. The cost of a B4C tile is in the range of $75/lb to $85/lb. The pressureless sintering processes of B4C and densification of B4C by solid state sintering techniques10 are slow, and it is difficult to reach high density due to low self-diffusion. Sintering aids such as SiC, Si, Al2O3, Mg, and Fe have been used to increase the density by means of liquid-phase sintering;11 however, the mechanical performance of liquid-phase-sintered B4C is inferior. It has been established that the presence of B2O3 coatings on B4C particles inhibits densification and facilitates grain coarsening.12 The boria can be removed by heat treatment in a hydrogen environment, which then permits direct contact between B4C–B4C grains, facilitating densification. As a result, the B4C powders with a particle size of approximately 1 μ can then be sintered to 96 percent of theoretical density and with hardness values similar to hot-pressed samples. Methods used to produce pressureless sintered B4C have been developed at the Georgia Institute of Technology and commercialized at Verco Materials,13as well as by larger armor producers such as Saint-Gobain. Armor-grade material of B4C with a zero porosity state can be produced using pressureless sintering combined with hot isostatic pressing.
Both SiC and B4C are harder materials with lower densities than alumina, yet alumina has been widely used in personnel and vehicle armor systems because of its lower
______________
7Stutz, D., S. Prochazka, and J. Lorenz. 1985. Sintering and microstructure formation of b–silicon carbide. Journal of the American Ceramics Society 68(9): 479-482.
8Sakai, T., H. Watanabe, and T. Aikawa. 1987. Effects of carbon on phase transformation of b–SiC with Al2O3. Journal of Materials Science Letters 6(7): 865-866.
9Omori, M., and H. Takei. 1988. Preparation of pressureless-sintered SiC–Y2O3–Al2O3. Journal of Materials Science 23(10): 3744-3749.
10Thévenot, F. 1990. Boron carbide—A comprehensive review. Journal of the European Ceramic Society 6(4): 205-225.
11H. Kim, H-W., Y-H. Koh, and H-E. Kim. 2000. Densification and mechanical properties of B4C with Al2O3 as a sintering aid. Journal of the American Ceramic Society 83(11):2863-2865.
12Cho, N., Z. Bao, and R. Speyer. 2005. Density and hardness-optimised pressureless sintered and post-hot isostatic pressed B4C. Journal of Materials Research 20 (8):2110-2116.
13Campbell, J., M. Klusewitz, J. LaSalvia, E. Chin, R. Speyer, N. Cho, N. Vanier, H. Cheng-Hung, E. Abbott, P. Votruba-Drzal, W. Coblenz, and T. Marcheaux. 2008. Novel processing of boron carbide (B4C): Plasma synthesized nano powders and pressureless sintering forming of complex shapes. ADM002187. Proceedings of the Army Science Conference (26th). Accessed April 1, 2011.
raw material cost and ease of fabrication. Large-size alumina panels up to 400 mm × 550 mm are currently produced by means of pressureless sintering14 for use in lightweight armor vehicles and police car door protection. Morgan is one is the main producers of armor-grade alumina made by the pressureless sintering technique.
HOT PRESSING
Hot pressing is often the procedure of choice for the manufacture of opaque ceramics, since it can produce fully dense ceramics at reasonably moderate temperatures and pressures. However, HP can only produce limited shapes such as flat plates or those with a small curvature. A current Army program is developing HP to fabricate SiC tiles at lower cost.15
Traditional hot pressing is a batch process in which the “green” powder compacts are formed by means of a suitable pressing method and then loaded into a hot-pressing die. Some armor manufacturers use tape casting or extrusion to build up green B4C armor shapes for hot pressing. The die and powder are ramped up to the sintering temperature and pressure is applied to the die. To meet the required high sintering temperatures (>2000°C), heated dies made of graphite or other high-strength inert materials are used in special hot-pressing furnaces. As the ceramic part size increases, the load requirements increase, making the HP equipment large. HP is associated with small production volumes, and typically large billets are produced to be cut into individual armor tiles. Often, multiple parts, separated by spacers, are pressed together to increase production rate. Once the ceramic is hot-pressed, it is cooled and then machined to its final dimensions by diamond tools using slow machining steps and grinding rates.
Materials with different final densities and mechanical properties are produced by varying the nature of powder additives and hot-pressing conditions such as pressure, temperature, and time. Typically, in hot-pressing SiC armor material, powders ofα–SiC are mixed with suitable sintering aids (boron and carbon, for example); additional carbon is added to remove the silica passivation layers from the SiC particles. Temperature steps are adjusted based on the specific mix of powders and additives, and during the last high-temperature cycle, pressure is applied to achieve maximum densification. Different final density and mechanical properties are reached by varying the hot-pressing conditions and the powder additives used. Additives and precise processing conditions are kept as proprietary information by different manufacturers.
Compared to lower-density, pressureless sintered products, the hot-pressing process is a slow batch process that typically yields a close-to-full-density product with superior ballistic properties. Hot-pressed SiC and B4C provide superior ballistic properties but are manufactured at high cost and in limited volumes through a batch process. The U.S. Army Manufacturing Technology Program has developed an HP apparatus with multiple heating and cooling chambers and central hot pressing chamber to reduce the cost of hot pressed 4 in. × 4 in. tiles from $135/lb to $85/lb.16 The goal is to increase production volumes, thus reducing the cost to $35/lb, similar to pressureless sintered material.
Due to processing differences, hot-pressed and pressureless sintered materials have different microstructures; see, for example, Figure E-1. Hot-pressed material is typically fully dense with fine microstructures, whereas pressureless sintered materials have large grains with texture. However, recent dynamic magnetic compaction (DMC) work has shown the promise of obtaining fine grain structures similar to those of HP material by combining DMC and pressureless sintering. Such a process needs to be further developed.
CURRENT-ASSISTED SINTERING
Nano-grain-size ceramic powders are currently being explored by various laboratories, including the U.S. Army Research Laboratory, to obtain better mechanical properties through microstructural modifications. However, when ceramic powders are hot-pressed or sintered at very high temperatures for extended times, grain growth takes place. Processing methods such as dynamic compaction or spark plasma sintering (SPS) techniques can be used to retain the small grain size of nanograined powders.
One method of accelerating the sintering process of difficult-to-sinter armor ceramics involves the use of electrical current. The name most often used for such field-assisted sintering is SPS, but the process is also known as plasma pressure sintering, pulsed electric current, and electric-pulse-assisted consolidation. Significant advantages exist for using current-assisted sintering over that of hot-pressing, hot isostatic pressing, or pressureless sintering; the most important advantage is lower sintering temperature and reduced holding time, which results in marked comparative improvements in mechanical properties.17 For example, attaining a heating rate of 600°C/min, typically used in SPS of ceramics, could help retain the homogeneous grain size distribution
______________
14Medvedovski, E. 2010. Ballistic performance of armour ceramics: Influence of design and structure Part 2. Ceramics International 36(7): 2117-2127.
15Protection materials—Research to acquisition. Briefing by E. Chin, U.S. Army Research, Development and Engineering Command, to the committee, July 23, 2010.
16Campbell, J., J. LaSalvia, W. Roy, E. Chin, R. Palicka, and D. Ashkin. 2008. New Low-Cost Manufacturing Methods to Produce Silicon Carbide (SiC) for Lightweight Armor Systems. ADA504013. Proceedings of the Army Science Conference (26th). Accessed April 4, 2011.
17Munir, Z., U. Anselmi-Tamburini, and M. Ohyanagi. 2006. The effect of electric field and pressure on the synthesis and consolidation of materials: A review of the spark plasma sintering method. Journal of Materials Science 41(3): 763-777.
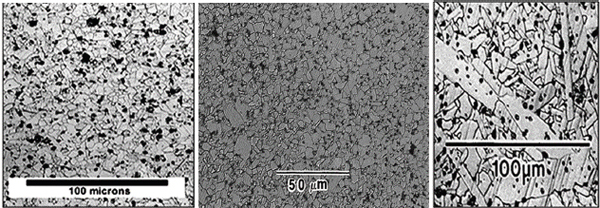
FIGURE E-1 Silicon carbide sample microstructures showing grains in (left) hot-pressing, (center) dynamic magnetic compaction followed by pressureless sintering, and (right) uniaxial pressing followed by pressureless sintering. SOURCE: Chelluri, B., and E.A. Knoth. 2008. SiC armor tiles via magnetic compaction and pressureless sintering. Presentation to the 32nd International Conference and Exposition on Advanced Ceramics and Composites, January 26-February 1, Daytona Beach, Florida.
along with the small average grain size of B4C.18,19 The spall strengths20 of SPS-processed B4C and SiC ceramics are improved over those from hot-pressing or pressureless sintering techniques. SPS is still under development, especially for sintering larger parts. Density variations are still observed in the case of difficult-to-sinter ceramics because of current flow along the highest-conductivity graphite die walls, although low or no current density is detected inside the part. As a result of such a temperature gradient, material density varies with its location relative to the die walls. The widespread adoption of SPS in the past decade was possible because of the availability of commercially built SPS systems. Currently the two major players are SPS SYNTEX Inc., Japan, and FCT Systeme GmbH, Germany. Recently, the U.S. firm Thermal Technology LLC also started selling field-assisted sintering furnaces. However, to the best of the committee’s knowledge, there are no commercially produced ceramic armor tiles using SPS, suggesting a potential opportunity for improved processing of dense ceramics.
REACTION-BONDED CERAMICS
Reaction-bonded SiC and reaction-bonded boron carbide have been successfully used for armor applications over the past decade.21,22,23,24 In reaction bonding, which uses silicon-based matrixes, the pressureless infiltration of a powder preform is achieved by good wetting and a highly exothermic reaction between liquid silicon and carbon.25 The process is known variously as reaction bonding, reaction sintering, self-bonding, or melt infiltration.
M Cubed Technologies Inc., a developer of the reaction bonding process, uses a process that includes the following steps: (1) mixing of B4C (or SiC) powder and a binder to make a slurry; (2) shaping of the slurry by various techniques, such as casting, injection molding, pressing, and others; (3) drying and carbonizing of the binder; (4) green machining; (5) infiltration (reaction bonding) with molten Si (or alloy) above 1410°C in an inert or vacuum atmosphere; and (6) solidification and cooling. During the infiltration step, carbon in the preform reacts with molten
______________
18Hayun, S., S. Kalabukhov, V. Ezersky, M. Dariel, and N. Frage. 2010. Microstructural characterization of spark plasma sintered boron carbide ceramics. Ceramics International 36(2): 451-457.
19Hayun, S., V. Paris, M.P. Dariel, N. Frage, and E. Zaretzky. 2009. Static and dynamic mechanical properties of boron carbide processed by spark plasma sintering. Journal of the European Ceramics Society 29(16): 3395-3400.
20Paris, V., N. Frage, M., Dariel, and E. Zaretsky. 2010. The spall strength of silicon carbide and boron carbide ceramics processed by spark plasma sintering. International Journal of Impact Engineering 37(11): 1092-1099.
21Waggoner, W., B. Rossing, M. Richmond, M. Aghajanian, and A. McCormick. 2003. Silicon carbide composites and methods for making same. U.S. Patent 6,503,572, filed July 21, 2000, and issued January 7, 2003, to M Cubed Technologies, Monroe, Conn.
22Aghajanian, M., B. Morgan, J. Singh, J. Mears, and R. Wolffe. 2002. A new family of reaction bonded ceramics for armor applications. Ceramic Transactions 134: 527-539.
23Aghajanian, M., McCormick, B. Morgan, and A. Liszkiewicz, Jr. 2005. Boron carbide composite bodies, and methods for making same. U.S. Patent 6,862,970, filed November 20, 2001, and issued March 8, 2005, to M Cubed Technologies. Monroe, Conn.
24Karandikar, P., M. Aghajanian, and B. Morgan. 2003. Complex, NET-shape composite components for structural, lithography, mirror and armor applications. Pp. 561-566 in 27th Annual Cocoa Beach Conference on Advanced Ceramics and Composites: B. Ceramic Engineering and Science Proceedings 24(4). W. Kriven and H-T. Lin, eds. Hoboken, N.J.: John Wiley & Sons.
25Karandikar, P., S. Wong, G. Evans, and M. Aghajanian. 2010. Microstructural development and phase changes in reaction bonded boron carbide. Pp. 5-22 in Advances in Ceramic Armor VI: Ceramic Engineering and Science Proceedings 31(5). Swab, J., S. Mathur, and T. Ohji, eds. Hoboken, N.J.: John Wiley & Sons.
Si, forming SiC around the original ceramic particles and bonding them together—hence the term “reaction bonding.” Typically the final product—that is, reaction-bonded boron carbide composite—consists of the original boron carbide particles, a newly formed ternary B–Si–C carbide, SiC, and some residual silicon. Because residual silicon adversely affects the mechanical properties of the composite,26,27,28,29 its amount, which is related to the free carbon present in compacted preform and also to the initial porosity,30 should be decreased. The porosity of the preform at the outset may be somewhat reduced by sintering31 or by using multimodal powder mixtures.32Adding titanium or iron or compounds that react with the boron carbide and release more free carbon33,34,35,36,37 or adding elements that react with silicon to form stable silicides38 may also serve to reduce the amount of residual silicon.
FUNCTIONALLY GRADED MATERIALS
A functionally graded material (FGM) is a two-component composite system with a defined compositional gradient across its section; the system is structured in such a way as to preserve the inherent properties of each component. In a metal/ceramic FGM structure, for example, the gradual transition between an impact-resistant outer ceramic layer bonded to a tough metal backing can be advantageously applied in armor protection design.39 FGMs such as titanium/titanium boride composites have the potential to reduce or eliminate the need for thermal protection in extreme environments such as those encountered by aerospace vehicles. They are also ideal for minimizing thermomechanical mismatch in metal/ceramic bonding.40,41,42,43 FGMs are also of interest for other defense-related applications, including as heat shields for rockets, fusion energy devices, and thermal barrier coatings for turbine blades. For armor protection applications, FGMs with bulk dimensions on the order of millimeters to centimeters are needed, but commercially viable processes to make such structures are still in development. These processes are hindered by the high cost and specialized nature—they often involve segregation approaches employing sedimentation forming, slip casting, centrifugal casting, and thixotropic casting.44,45,46
Experimental and theoretical work recently revealed that controlled gradients in mechanical properties can guide the design of surfaces that are resistant to contact deformation and damage; such properties cannot be realized in conventional homogeneous materials. Wear-resistant, nano-
______________
26Hayun, S., D. Rittel, N. Frage, M.P. Dariel. 2010. Static and dynamic mechanical properties of infiltrated B4C-Si composites. Materials Science Engineering A 487(1-2):405-409.
27Aghajanian, M., B. Morgan, J. Singh, J. Mears, and R. Wolffe. 2001. A new family of reaction bonded ceramics for armor applications. Pp. 527-555 in Ceramic Armor Materials by Design. Ceramic Transactions 134. J. McCauley, J., and A. Crowson, eds. Baltimore, Md.: American Ceramic Society.
28Chhillar P., M. Aghajanian, D. Marchant, R. Haber, and M. Sennett. 2009. The effect of Si content on the properties of B4C-SiC-Si composites. Pp. 161-167 in Advances in Ceramic Armor III: Ceramic and Engineering Science Proceedings 28(5). Franks, L., J. Salem, and D. Zhu, eds. Hoboken, N.J.: John Wiley & Sons.
29Hayun, S., A. Weizmann, M. Dariel, and N. Frage. 2009. The effect of particle size distribution on the microstructure and the mechanical properties of boron carbide-based reaction-bonded composites. International Journal of Applied Ceramic Technology 6(4):492-500.
30Hayun, S., N. Frage, M. Dariel, E. Zaretsky, and Y. Ashuah. 2006. Dynamic response of B4C-SiC ceramic composites. Ceramic Transactions 178: 147-156.
31Hayun, S., N. Frage, and M. Dariel. 2006. The morphology of ceramic phases in BxC-SiC-Si infiltrated composites. Journal of Solid State Chemistry 179(9): 2875-2879.
32Hayun, S., A. Weizmann, M. Dariel, and N. Frage. 2009. The effect of particle size distribution on the microstructure and the mechanical properties of boron carbide-based reaction-bonded composites. International Journal of Applied Ceramic Technology 6(4):492-500.
33Hayun, S., N. Frage, H. Dilman, V. Tourbabin, and M. Dariel. 2006. Synthesis of dense B4C-SiC-TIB2 composites. Ceramic Transactions 78: 37-44.
34Mizrahi, I., A. Raviv, H. Dilman, M. Aizenshtein, M. Dariel, and N. Frage. 2007. The effect of Fe addition on processing and mechanical properties of reaction infiltrated boron carbide-based composites. Journal of Materials Science 42(16): 6923-6928.
35Sigl, L., H. Thaler, and K-A. Schwetz. 1994. Elemental carbon-containing boron carbide-titanium diboride composites, and their manufacture and use. [Verbundwerkstoff auf Basis von Borcarbid, Titanborid und Elementarem Kihlenstoff sowie Verhahren zu ihrer Herstellung.] European Patent 628525, filed June 11, 1993, and issued June 9, 1994, to Elektroschmelzwerk Kempten GmbH, Munich, Germany.
36Sigl, L., H. Thaler, and K-A. Schwetz. 1996. Composite materials based on boron carbide, titanium diboride and elemental carbon and processes for preparation of same. U.S. Patent 5,543,337, filed May 24, 1994, and issued August 6, 1996, to Elektroschmelzwerk Kemptem GmbH. Munich, Germany.
37Sigl, L. 1998. Processing and mechanical properties of boron carbide sintered with TiC. Journal of the European Ceramic Society 18(1):1521-1529.
38Messner, R., and Y-M. Chiang. 2008. Processing of reaction-bonded silicon carbide without residual silicon phase. Pp. 1053-1059 in Proceedings of the 12th Annual Conference on Composites and Advanced Ceramic Materials, Part 1 of 2: Ceramic Engineering and Science Proceedings 9(7/8). J. Wachtman, ed. Hoboken, N.J.: John Wiley & Sons.
39Hirai, T. 1996. Functional gradient materials. Pp. 293-341 in Processing of Ceramics, Part 2. Cahn, R., and R. Brook, eds. New York, N.Y.: VCH.
40Ibid.
41Chin, E. 1999. Army focused research team on functionally graded armor composites. Materials Science and Engineering A259(2): 155-161.
42Suresh, S. 2001. Graded materials for resistance to contact deformation and damage. Science 292(5526): 2447-2451.
43Gooch, W., B. Chen, M. Burkins, R. Palicka, J. Rubin, and R. Ravichandran. 1999. Development and ballistic testing of a functionally gradient ceramic/metal appliqué. Materials Science Forum 308-311:614-621.
44Kleponis, D., A. Mihalcin, and G. Filbey, Jr. 2005. Material design paradigms for optimal functional gradient armors. Army Research Lab Weapons and Materials Directorate. Available at http://handle.dtic.mil/100.2/ADA436346. Accessed April 4, 2011.
45Clougherty, E. 1974. Graded impact resistant structure of titanium diboride in titanium. U.S. Patent 3,802,850, filed November 13, 1972, and issued April 9, 1974, to Man-Labs, Incorporated, Cambridge, Mass.
46Johnson, G., T. Holmquist, and S. Beissel. 2003. Response of aluminum nitride (including a phase change) to large strains, high strain rates, and high pressures. Journal of Applied Physics 94(3), 1639-1647.
crystalline surface coatings, with grain sizes as small as a few tens of nanometers, can be synthesized by means of electrodeposition, thermal spray, sputter deposition, metal-organic chemical vapor deposition, and eletrophoretic deposition.47 Many of these processes can create surface layers wherein the grain sizes are smoothly graded from the surface to the bulk, bringing about controlled gradients in strength and fracture toughness. Similarly, improved resistance to contact damage can be achieved by tailoring gradients in porosity below the contact surfaces. Current materials synthesis and processing capabilities, engineered gradations in properties—from nanometer to macroscopic length scales—appear promising for the design of improved fracture-, damage-, and wear-resistant structures and surfaces and for armor protection applications.
BIOMIMETIC MATERIALS
Natural materials that are mechanically robust often have hierarchical designs. Abalone nacre, rat teeth, fish scales, wood, and spider silk exhibit highly complex hierarchical structures, multifunctionality, and even self-healing capabilities48 and thus are appealing to mimic for use in advanced armor design. The remarkable mechanical performance of certain natural materials stems from their complex ordered microstructure, organized over several length scales, even though the materials are often made of relatively weak constituents. Nacre, which is found in a number of mollusk shells, combines stiffness and strength along with a high level of toughness. Mimicking of the abalone structure was first attempted in the 1980s, when a laminated structure of Al–B4C was produced.49 A significant increase in fracture toughness (up to 16 MPa-m1/2) was achieved; however, Al4C3 was formed during the processing of the laminates, limiting the useful armor application of the produced laminates owing to low hardness and strength and the high brittleness of the Al4C3 phase. Another example of mimicking abalone nacre, but on a macroscale, was conducted a decade ago by Foster-Miller50—LAST (Light Applique Segmented Tile) armor plates were produced using Coors alumina and SiC or B4C hexagonal tiles covered in a thermoset laminate of Kevlar and held together with a Velcro-type adhesive. A nacre-like armor structure such as this absorbs energy and serves to toughen by many of the same mechanisms that occur in natural nacre. The entire array is fastened onto the steel plates of tanks and similar vehicles using Velcro. The armor has been implemented onto various ground and air vehicles, including 1,000 High Mobility Multipurpose Wheeled Vehicles (Humvees) for the U.S. Marines.
Another example of a natural material for biologically inspired design is the skins of certain fish. Both the scales and dermis of fish skin are highly pliant, lightweight, and resist penetration—all of this in an ultrathin structure.51 Although fish scales have received very little attention, it is recognized that bony scales are difficult to penetrate and dissipate energy quite well.52 Scales form a physical barrier that deters attacks by predators; indeed, they were likely the inspiration for scale armor not only in ancient times but also in modern times.53 While its hierarchical organization is important for the overall mechanical performance of fish skin,54 the contributions at the different length scales are rarely investigated. It is not known, for instance, how adjacent scales interact to thwart penetration, but this mechanism should be understood if its performance in the new generation of ultralight pliant armor systems is to be replicated.
Biomorphic ceramics using natural products such as wood and cellulose-fiber paper and cardboard have also been of interest for their potential use as armor materials.55In particular, wood-based biomorphic SiC (bioSiC) is a promising material for armor. The fabrication of bioSiC entails the rapid mineralization of wood, during which the wood is carbonized and then infiltrated with either Si vapor or Si melt. The formed SiC replicates the wood microstructure, and the diversity of the wood texture results in a large and varied selection of bioSiC ceramics. Novel biomorphic SiC ceramics have been successfully developed at DLR, Germany’s national research center for aeronautics and space.56,57 At DLR, wood-based preforms are converted to SiSiC materials using the liquid silicon infiltration process. In this process, a green body or preform based on low-cost raw materials—for
______________
47Suresh, S. 2001. Graded materials for resistance to contact deformation and damage. Science Magazine 292(5526):2447-2451. Available online at http://www.sciencemag.org/content/292/5526/2447.full. Accessed October, 11, 2010.
48Meyers, M., P-U. Chen, A. Lin, and Y. Seki. 2008. Biological materials: Structure and mechanical properties. Progress in Materials Science 53(1): 1-206.
49Sarikaya, M., and I.A. Aksay. 1992. Nacre of abalone shell: A natural multifunctional nanolaminated ceramic polymer composite material. Pp. 1-25 in Structure, Cellular Synthesis and Assembly of Biopolymers (Results and Problems in Cell Differentiation) 19(1). S. Case, ed. Amsterdam: Springer-Verlag.
50QinetiQ. www.foster-miller.com. Accessed October 13, 2010.
51Vernerey, F., and F. Barthelat. 2010. On the mechanics of fishscale structures. International Journal of Solids and Structures 47(17): 2268-2275.
52Bruet, B., J. Song, M. Boyce, and C. Ortiz. 2008. Materials design principles of ancient fish armour. Nature Materials 7: 748-756.
53Vernerey, F., and F. Barthelat. 2010. On the mechanics of fishscale structures. International Journal of Solids and Structures 47(17): 2268-2275.
54Fratzl, P., and R. Weinkamer. 2007. Nature’s hierarchical materials. Progress in Materials Science 52(177): 1263-1334.
55Medvedovski, E. 2010. Ballistic performance of armour ceramics: Influence of design and structure. Part 1. Ceramics International 36(7): 21032115.
56Heidenreich, B., M. Gahr, E. Strassburger, and E. Lutz. 2010. Biomorphic SiSiC-materials for lightweight armour. Pp. 21-33 in Proceedings of 30th International Conference on Advanced Ceramics & Composites 2010. Hoboken, N.J.: John Wiley & Sons.
57Heidenreich, B., M. Crippa, H. Voggenreiter, H. Gedon, M. Nordmann, and E. Strassburger. 2010. Development of biomorphic SiSiC- and C/SiSiC- materials for lightweight armour. Advances in Ceramics Armor VI: Ceramic Engineering and Science Proceedings (31). Hoboken, N.J.: John Wiley & Sons.
example, wood fibers and phenolic resin—is manufactured by means of warm pressing. One preform used for manufacturing biomorphic SiSiC is medium-density fiberboard, which is widely used in the furniture industry. The preform is made by pressing fine fibers of needle wood with binders based on formaldehyde or phenolic resins in a mass production process, making very large panels—typically 1.22 m × 2.44 m (4 ft× 8 ft) up to 2.8 m × 6.5 m (9.2 ft × 21.3 ft)—at a cost of about $1.75/kg. After pyrolysis, the porous C-preform is siliconized in a vacuum at temperatures above 1450°C; next, capillary forces allow molten silicon to infiltrate the open pores of the C-preform. The resulting reaction with the carbon forms SiSiCx.58 The final composition—that is, the content of SiC, Si, and C—is heavily influenced by the porosity and microstructure of the C-preform and can be varied widely by using tailored green bodies. Because practically no change in geometry occurs during siliconization or in reproducible contraction rates during pyrolysis, even large and complicated shaped parts can be manufactured using a cost-effective, near-net-shape technique.
The processing technology for bioSiC makes the production of complex shapes relatively easy; production is much cheaper, because the bioSiC forms at much lower temperatures than those required for SiC sintering or hot-pressing techniques. Biomorphic SiC shows excellent thermomechanical performance along with structural stability over a wide range of temperatures.59,60,61,62,63,64,65 BioSiC consists of b-SiC formed as a result of the interaction of Si and C, a significant quantity of residual Si (up to 30 vol percent), and a very small amount of carbon (up to 3 vol percent). The typical structure of bioSiC is more homogeneous than conventional reaction-bonded SiC and is defined by the particular wooden preform. The typical size of SiC grains is 5 to 20 μ, but owing to the relatively high content of residual Si, the density is about 2.8 g/cm3. BioSiC ceramics, such as one manufactured using inexpensive preforms from medium-density fiberboard66 can be produced inexpensively for armor systems consisting of large, single-piece components. Biomorphic siliconized silicon carbide (SiSiC) has demonstrated good potential for use in lightweight ceramic armor systems. Although manufacturing defects and excessive residual silicon in bioSiC reduce ballistic performance, especially in multi-hit situations, appropriate armor system design—that is, with the right selection of ceramic thickness and type and backing thickness—allows the materials to withstand even armor-piercing rounds. In order to increase resistance to multiple hits, novel materials based on the combination of biomorphic SiSiC and C/C-SiC ceramics have been developed, with carbon fibers integrated into biomorphic SiSiC to increase ductility and damage tolerance.
There is special interest in replicating dragline silk, the extremely strong silk that forms the framing threads of spider webs. The comparative properties of selected silk and manmade fibers are presented in Table E-2.
Mimicking the structure of materials found in nature might provide insight into the creation of armor materials with superior ballistic properties. However, the task of producing manmade materials with similar microstructures and performance is challenging precisely because the structures are so complex.
MACHINING, GRINDING, AND POLISHING CERAMICS
The machining, grinding, and polishing of ceramics are expensive processes. For example, the final shape of the armor product from a flat, hot-pressed part is created by grinding with diamond wheels. The pressureless sintered process, with its much larger shrinkage (20 to 30 percent), requires considerably more grinding to achieve final tolerances. Therefore, grinding and finishing costs make the final cost of hot-pressed parts higher than that of pressureless sintered parts. Part geometry and concentricity or parallelism also affect the final cost. For example, improving the tolerance of the outside diameter from 0.020 in. to 0.010 in. can double the cost of a piece. Typically, a ground part has a surface finish tolerance of 16 μin. or better. A better finish of 4 μin. can be obtained using lapping and honing, but will cost more.
______________
58Gahr, M., J. Schmidt, W. Krenkel, A. Hofenauer, and O. Treusch. 2004. Dense SiSiC ceramics derived from different wood-based composites: processing, microstructure and properties. P. 425 in Proceedings of the 5th International Conference on High Temperature Ceramic Matrix Composites. Westerville, Ohio: The American Ceramic Society.
59Martinez-Fernández, J., F. Valera-Feria, and M. Singh. 2000. High temperature compressive mechanical behavior of biomorphic silicon carbide ceramics. Scripta Materialia 43(9): 813-818.
60Martínez-Fernández J., F. Valera-Feria, Rodríguez, A., and M. Singh. 2000. Microstructure and thermomechanical characterization of biomorphic silicon carbide-based ceramics. Pp. 733-740 in Environment Conscious Materials: Ecomaterials. 39th Annual Conference of Metallurgists. Ottawa, Canada: Canadian Institute of Mining.
61Singh, M., J. Martínez-Fernández, A., and de Arellano-López. 2003. Environmentally conscious ceramics (ecoceramics) from natural wood precursors. Current Opinion in Solid State and Materials Science 7(3): 247-254.
62de Arellano-López, A, J. Martínez-Fernández, P. González, C. Domínguez, V. Fernández-Quero, and M. Singh. 2004. Biomorphic SiC: A new engineering ceramic material. International Journal of Applied Ceramic Technology 1(1): 56-67.
63Varela-Feria, F., J. Martínez-Fernández, A. de Arellano-López, and M. Singh. 2002. Low density biomorphic silicon carbide: Microstructure and mechanical properties. Journal of the European Ceramic Society 22(14-15): 2719-2725.
64Varela-Feria, F., J. Ramírez-Rico, A. de Arellano-López, J. Martínez-Fernández, and M. Singh. 2008. Reaction-formation mechanisms and microstructure evolution of biomorphic SiC. Journal of Materials Science 43(3): 933-941.
65Bautista, M., A. de Arellano-López, J. Martínez-Fernández, A. BravoLéon, and J. López-Cepero. 2009. Optimization of the fabrication process for medium density fiberboard (MDF)-based biomimetic SiC. International Journal of Refractory Metals and Hard Materials 27(2): 431-437.
66Heidenreich, B., M. Gahr, and E. Medvedovski. 2005. Biomorphic reaction bonded silicon carbide ceramics for armor applications. Pp. 45-53 in Proceedings of the 107th Annual Meeting of the American Ceramic Society. Hoboken, N.J.: Wiley-Blackwell.
TABLE E-2 Tensile Mechanical Properties of Spider Silks and Other Materials
|
||||
Material |
Stiffness (GPa) |
Strength (GPa) |
Strain to Failure |
Toughness (MJ-m–3) |
|
||||
Natural fibers |
||||
Araneus major Ampullate (MA) silk |
10 |
1.1 |
0.27 |
160 |
A. viscid silk |
0.003 |
0.5 |
2.7 |
150 |
Nephila clavipes silk |
11-13 |
0.88-0.97 |
0.17-0.18 |
40-130a |
N. edulis silk |
208b |
|||
Bombyx mori cocoon silk |
7 |
0.6 |
0.18 |
70 |
B. mori silk (w/sericin) |
5-12 |
0.5 |
0.19 |
35-55c |
B. mori silk (w/o sericin) |
15-17 |
0.61-0.69 |
0.4-0.16 |
30-70d |
Synthetic materials |
||||
Nylon fiber |
5 |
0.95 |
0.18 |
80 |
Kevlar 49 fiber |
130 |
3.6 |
0.027 |
50 |
Carbon fiber |
300 |
4 |
0.013 |
25 |
High-tensile steel |
200 |
1.5 |
0.008 |
6 |
|
aGosline, J., M. DeMont, and M. Denny. 1986. The structure and properties of spider silk. Endeavour 10(1): 37-43; Zemlin, J. 1968. A study of the mechanical behavior of spider silks. Technical Report 69-29-CM (AD 684333). U.S. Army Natick Laboratory, Natick, Mass.; Cunniff, P., S. Fossey, M. Auerbach, J. Song, D. Kaplan, W. Adams, R. Eby, D. Mahoney, and D. Vezie. 1994. Mechanical and thermal properties of dragline silk from the spider Nephila clavipes. Polymers for Advanced Technologies 5(8): 401-410.
bVollrath, F., B. Madsen, and Z. Shao. 2001. The effect of spinning conditions on the mechanics of a spider’s dragline silk. Proceedings of the Royal Society 268(1483):2339-2346.
cPérez-Rigueiro, J., C. Viney, J. Llorca, and M. Elices. 1998. Silkworm silk as an engineering material. Journal of Applied Polymer Science 70(12): 2439-2447.
dPérez-Rigueiro, J., C. Viney, J., Llorca, and M. Elices. 2000. Mechanical properties of single-brin silkworm silk. Journal of Applied Polymer Science 75(10): 1270-1277.
FOAMS
Foam is a complex assemblage of dispersed voids or pores separated by a film. The reason for using foams to absorb shock wave energy is that as the shock wave passes into the foam, the individual cells collapse; it is through this deformation that energy is absorbed. Foams can be made from any number of materials and may be open-or closed-cell, but it is the metal foams, particularly aluminum, and the polymeric foams, particularly polyurethane, that are employed most frequently in shock wave research.67,68,69 Two important directions for future research are (1) constructing foams from a wider variety of materials and (2) developing methods for greater control over foam microstructure. Such model foams will help computational efforts on porous structures.
The use of foams as impact barriers was demonstrated by Gama et al.,70 who performed impact tests on layered composite armor systems with various foam positions and thicknesses, using 20 mm fragment simulating projectiles (FSP). A test performed with an impact velocity of 1,067 m/s on a baseline setup, followed by a test on the baseline with a 12.7-mm-thick piece of aluminum foam incorporated into the material stack, revealed that the rise time of the stress wave increased from 1 ms for the baseline sample to 2 ms for the sample with foam. The use of foam also delayed the time for the stress wave to reach the stress gauge by about 14.6 ms. The maximum stress reached in both cases was about 6.25 GPa. The air-filled cellular structure of the foam is not conducive to wave propagation because the waves are only transmitted along the cell walls, which, owing to their random orientations, tend to disperse the wave. For a foam thickness of 12.7 mm, a stress of 0.825 GPa was recorded in the ceramic tile, while a thickness of 30.48 mm completely eliminated the stress recorded in the tile. In this case, the foam was not fully compacted by the FSP and thus acted as an excellent wave barrier.
The location of the foam is also important, demonstrating the need not only to consider the inherent material properties in isolation but also to consider them as part of the overall armor system.
TRANSPARENT CERAMICS AND EMBEDDED DAMAGE SENSORS
Transparent armor ceramics must provide good transparency in the visible (0.4-0.7 μ) and mid-infrared (1-5 μ)
______________
67Hanssen, A., L. Enstock, and M. Langseth. 2002. Close-range blast loading of aluminum foam panels. International Journal of Impact Engineering 27(6): 593-618.
68Ramachandra, S., P. Sudheer Kumar, and U. Ramamurty. 2003. Impact energy absorption in an Al foam at low velocities. Scripta Materialia 49(8): 741-745.
69Gama, B., T. Bogetti, B. Fink, C. Yu, T. Dennis Claar, H. Eifert, and J. Gillespie. 2001. Aluminum foam integral armor: A new dimension in armor design. Composite Structures 52(3-4): 381-395.
70Ibid.
optical ranges and protection against fragmentation from ballistic impacts, with multi-hit capability and minimal distortion around the impacted regions.71,72
As mentioned in Chapter 5, transparent armor systems are typically constructed of multiple layers of armor-grade ceramic plates, separated by transparent polymer (for example, polycarbonate) interlayers, and are bonded together with a transparent adhesive. The polymer phase mitigates the stresses generated by thermal expansion mismatches and inhibits crack propagation from ceramic to polymer. Polymeric materials such as transparent nylons, polyurethanes, and acrylics have also been explored as separators, but they have not been widely used in armor protection owing to less-than-optimal optical and durability characteristics. Transparent alumina (Al2O3) and magnesia (MgO) are two commonly used transparent ceramic armor materials. The composite system formed by these two materials provides good protection against high-velocity ballistic projectiles.73,74 Silicon nitride (Si3N4), a nonoxide ceramic, has also been employed for use in radomes because of its good transit of microwave energy and its superior mechanical strength.
These materials can be produced as transparent polycrystalline ceramic parts, often with complex geometries, by using standard ceramic-forming techniques such as pressing, (hot) isostatic pressing, and slip casting.75
Nanocomposite ceramic materials of yttria (Y2O3) and magnesia (MgO) have been explored for use in transparent armor protection. The materials exhibit an average grain size of approximately 200 nm, and near-theoretical transmission in the 3 to 5 μ infrared band range. These complex ceramic nanocomposites reportedly offer improved mechanical properties such as superplastic flow and metal-like machinability. However, mechanical failure modes and armor protection characteristics must still be fully evaluated for these nanocomposite materials systems.76,77,78 These materials have potential for use in new dome construction requiring substantial durability and high transparency across the operational bandwidth for infrared-guided missile sensing.79,80,81 Special glasses and glass-ceramics such as lithium disilicate or aluminum-lithium-based crystallized or partially crystallized structures also offer advantages as host materials for laser use, since their refractive indexes and strain-optical coefficients can be readily controlled through changes in chemical composition.82
Damage-Reactive Sensors for Armor
Combat vehicles could be outfitted with smart ceramic sensors built into the protective armor material. Such sensor could detect and report on structural damage in real time. Structural damage caused by a wide range of ballistic impacts can be expected to affect armor structures under battlefield conditions. Changes in the armor’s structural condition can be detected by tiny piezoelectric transducers, or sensors, built into the protective armor plate material. Piezoelectric sensors are usually ferroelectric, perovskite structure materials—for example, lead zirconate/lead titanate, barium titanate, and others—that have been suitably doped and electrically poled to optimize their piezoelectric response characteristics.83,84
Given the above relationships, the piezoelectric transducers can be designed both to generate and to receive voltage responses when coupled with ultrasonic waves that are generated to pass through the material. To determine the best response characteristics for particular environmental conditions, the ultrasonic signals may vary over a wide frequency range (1.0 kHz to 200 kHz). A generated shock wave through the plate picks up the reflections of sound waves and converts them into electrical voltages from which, with suitable amplification, one can determine their spectra and whether the plate is cracked or damaged.
______________
71Patel, P., G. Gilde, P. Dehmer, and J. McCauley. 2000. Transparent ceramics for armor and EM window applications. P. 1 in Proceedings of the International Society for Optics and Photonics 4102(1).
72Harris, D. 2009. Materials for infrared windows and domes: Properties and performance. Bellingham, Wash.: International Society of Optical Engineers.
73Villalobos, G., J. Sanghera, and I. Aggarwal. 2005. Transparent ceramics: Magnesium aluminate spinel. Naval Research Laboratory Optical Sciences Division.
74Hogan, P., R. Stefanik, C. Willingham, and R. Gentilman. 2004. Transparent yttria for IR windows and domes—Past and present. Raytheon Integrated Defense Systems.
75Ibid.
76Bisson, J-F., Lu Jianren, K. Takaichi, Yan Feng, M. Tokurakawa, A. Shirakawa, A. Kaminskii, H. Yagi, T. Yanagitani, and K-I. Ueda. 2004. Nanotechnology is stirring up solid-state laser fabrication technology. Recent Research Developments in Applied Physics 7(Part II): 475-469.
77Wen, L., X. Sun, S. Chen, and C-I. Tsai. 2003. Synthesis of nanocrystalline yttria powder and fabrication of transparent YAG ceramics. Journal of the European Ceramics Society 24(9): 2681-2688.
78Wen, L., X. Sun, Q. Lu, G. Xu, and X. Hu. 2006. Synthesis of yttria nanopowders for transparent yttria ceramics. Optical Materials 29(2-3): 239-245.
79Huang, Z., X. Sun, Z. Xiu, S. Chen, and C-T. Tsai. 2004. Precipitation synthesis and sintering of yttria nanopowders. Materials Letters 58(15): 2137-2142.
80Jeong, J., S. Park, D. Moon, and W. Kim. 2010. Synthesis of Y2O3 nanopowders by precipitation method using various precipitants and preparation of high stability dispersion for backlight unit (BLU). Journal of Industrial Engineering Chemistry 16(2): 243-250.
81Nihara, K., and T. Sekino. 1993. New nanocomposite structural ceramics. P. 405 in Materials Research Society Symposium Proceedings held at the Nanophase and Nanocomposite Materials Symposium. Warrendale, Pa.: Materials Research Society.
82Hartmann, P., R. Jedamzik, S. Reichel, and B. Schreder. 2010. Optical glass and glass ceramic historical aspects and recent developments: A Schott view. Applied Optics 49(16): D157-D176.
83Meitzler, T., G. Smith, M. Charbeneau, E. Sohn, M. Bienkowski, I. Wong, and A. Meitzler. 2008. Crack detection in armor plates using ultrasonic techniques. Materials Evaluation 66(6): 555-559.
84Song, J., and G. Washington. 2000. Plate vibration modes identification by using piezoelectric sensors. Pp. 867-878 in Smart Structures and Materials 2000. International Society for Optics and Photonics 3985.
Armor Damage Control Sensors
The piezoelectric transducers can perform other functions that contribute to armor and vehicle survivability. For example, they can be made to act as antennas; to monitor the temperature of armor structures, including that of body armor, and to detect and monitor projectile impacts on the armor surface. For the latter application, each projectile striking the armor will create an electrically generated shock wave and differing amounts of electricity; a smart sensor can integrate these effects to generate useful information. Complex mathematical algorithms can be used to analyze the amount of electricity generated by a bullet’s impact to determine what kind of round was used, since a small-caliber projectile will generate less electricity than a large-caliber projectile.85 This combination of detection and assessment of threat level in real time could be significant for developing armor survival strategies. The following conclusions may be drawn:
- Infrared-transparent nanocomposite materials in the systems SiC/Al2O3, SiC/Si3N4, SiC/MgO, Al2O3/ZrO2, and transparent Al2O3 offer greatly enhanced ballistic needs for transmission in the 3 to 5 μ range, significantly increased mechanical strength of (700 MPa), and fracture toughness and creep resistance of interest for next-generation armor use.
- Piezoelectric transducers coupled with acoustic wave propagation and complex mathematical algorithms can be used to analyze impact damage to armor structures from ballistic projectiles.
PHONONIC BAND GAP CONCEPTS FOR PROTECTIVE MATERIALS
Shortly after research on photonic band gaps began to show promise of controlling the flow of photons, the idea was extended to mechanical waves in periodic elastic structures. Referred to as phononic crystals, such structures can create what are called phononic, or acoustic, band gaps. A phononic crystal prevents the propagation of elastic waves if the frequencies of the waves fall within a band gap. The normalized width of the band gap—the ratio of band-gap width to the central frequency of the gap—is a measure of the performance of the particular phononic crystal design. In addition to preventing the propagation of waves, phononic crystals dictate the nature of the modes that are allowed to propagate in the material; they can decrease the velocity of the waves and even force their negative refraction. This capability suggests numerous ideas that could someday be developed to influence material fabrication and enhance armor designs to take advantage of the new ability to control mechanical waves in armor materials.
Because there are three polarizations of elastic waves in solid materials—longitudinal, transverse (shear) in plane, and transverse out of plane—for a structure to possess a full band gap, it must prohibit the propagation of all types of waves in all directions. A phononic crystal can create an acoustic band gap through a combination of Bragg diffraction (destructive wave interference) and Mie resonances86 as well as anticrossing of bands having the same mode symmetry.87 Bragg scattering occurs when the wavelength of the phonon is approximately equal to the periodicity of the structure, and Mie resonances occur when the diameter of the scattering features is of the same order as the wavelength. Some of the earliest references to phononic crystals are from Sigalas and Economou88,89 and Kushwaha et al.90,91 A rather complete library of phononic crystal research may be found by consulting Vlasov and Dowling.92,93
The length scale of phononic crystals ranges from the macroscopic—meters for acoustic waves (kHz) to millimeters for the ultrasound typically used in medical imaging (MHz), and down to the nanoregime—approximately100 nm for waves in the gigahertz (GHz) regime. In general, design rules for creating a gap are based on Bragg scattering and the use of highly symmetric structures to minimize the irreducible Brillouin zone over which the gap occurs. The materials parameters that are important are density, elastic modulus, and Poisson ratio or, equivalently, density and the transverse and longitudinal speed of sound in the materials. Because the waves are scattered from interfaces that affect wave propagation implies that understanding the differences in mechanical impedance of the materials comprising the structure (impedance is the product of density and wave speed) is key to understanding how phononic crystals can control the propagation of mechanical waves. However, in
______________
85Sands, J., C. Fountzoulas, G. Gilde, and P. Patel. 2009. Modelling transparent ceramics to improve military armour. Special Issue on Transparent Ceramics, Journal of the European Ceramics Society 29(2): 261-266.
86Mie theory, also called Lorenz-Mie theory, Lorenz-Mie-Debye theory, and Mie scattering, is an analytical solution of Maxwell’s equations for the scattering of electromagnetic radiation by spherical particles.
87Kushwaha, M., A. Akjouj, B. Djafari-Rouhani, L. Dobrzynski, and J. Vasseur. 1998. Acoustic spectral gaps and discrete transmission in slender tubes. Solid State Communications 106(10): 659-663.
88Sigalas, M., and E. Economou. 1992. Elastic and acoustic wave band structure. Journal of Sound and Vibration 158(2): 377-382.
89Sigalas, M., and E. Economou. 1993. Band structure of elastic waves in two dimensional systems. Solid State Communications 86(3): 141-143.
90Kushwaha, M., P. Halevi, L. Dobrzynski, and B. Djafari-Rouhani. 1993. Acoustic band structure of periodic elastic composites. Physical Review Letters 71(13): 2022-2025.
91Kushwaha, M., P. Halevi, G. Martinez, L. Dobrzynski, and B. Djafari-Rouhani. 1994. Theory of acoustic band structure of periodic elastic composites. Physical Review B 49(4): 2313-2322.
92Yaslov, Y. Photonic band gap links. Available at http://www.pbglink.com.
93Dowling, J. 2008. Photonic and sonic band-gap bibliography. Available at http://phys.lsu.edu/~jdowling/pbgbib.html. Accessed on November 6, 2010.
solids, in addition to simple reflection at an interface, polarization conversion always occurs; making it difficult to form complete gaps, and a design strategy for optimal constructs is not yet available. The use of fluids (which support only longitudinal waves) makes it difficult to form gaps because of the conversion of shear modes into longitudinal modes at the solid-fluid interface.
The idea of using a structured material to influence the propagation of elastic waves is promising since in addition to creating a band gap, there is the possibility of creating a set of band gaps that would significantly block multiple frequencies. Moreover, phononic crystals permit the tailoring of the allowed modes and their wave speeds inside the material, such that the frequencies of various material loss regimes may be matched with the density of states and frequencies of the allowed modes to provide enhanced energy absorption.