6
Working with Laboratory Equipment
6.A INTRODUCTION
Proper use of laboratory equipment is required to work safely with hazardous chemicals. Maintenance and regular inspection of laboratory equipment are an essential part of this activity. Many of the accidents that occur in the laboratory can be attributed to improper use or maintenance of laboratory equipment. This chapter discusses prudent practices for handling the apparatus often used in laboratories.
The most common equipment hazards in laboratories come from electrically powered devices, and these are followed by hazards with devices for work with compressed gases and high/low pressures and temperatures. Other physical hazards include electromagnetic radiation hazards from such equipment as lasers and radio-frequency generating devices. Seemingly ordinary hazards such as floods from water-cooled equipment, accidents with rotating equipment and machines or tools for cutting and drilling, noise extremes, slips, trips, and falls, lifting, and poor ergonomics probably account for the greatest frequency of laboratory accidents and injuries.
6.B WORKING WITH WATER-COOLED EQUIPMENT
The use of cooling water in laboratory condensers and other equipment is common laboratory practice, but can create a flooding hazard. The most common source of the problem is disconnection of the tubing supplying the water to the condenser. Hoses can pop off under irregular flows when building water pressure fluctuates or can break when the hose material has deteriorated from long-term use. Floods also result when exit hoses jump out of the sink from a strong flow pulse or sink drains are blocked by an accumulation of extraneous material. Proper use of hose clamps and maintenance of the entire cooling system or alternate use of a portable cooling bath with suction feed can resolve such problems. Plastic locking disconnects can make it easy to disconnect water lines without having to unclamp and reclamp secured lines. Some quick disconnects also incorporate check valves, which when disconnected do not allow flow into or out of either half of the connection. This feature allows for disconnecting and reconnecting with minimal spillage of water.
6.C WORKING WITH ELECTRICALLY POWERED LABORATORY EQUIPMENT
Electrically powered laboratory equipment is used routinely for laboratory operations requiring heating, cooling, agitation or mixing, and pumping. Electrically powered equipment found in the laboratory includes fluid and vacuum pumps, lasers, power supplies, both electrophoresis and electrochemical apparatus, x-ray equipment, stirrers, hot plates, heating mantles, and, more recently, microwave ovens and ultrasonicators. Attention must be paid to both the mechanical and the electrical hazards inherent in these devices. High voltage and high power requirements are increasingly prevalent; therefore prudent practices for handling these devices are increasingly necessary.
Electric shock is the major electrical hazard. A relatively low current of 10 milliamperes (mA) poses some danger, and 80 to 100 mA can be fatal. In addition, if improperly used, electrical equipment can serve as an ignition source for flammable or explosive vapors. Most of the risks involved can be minimized by regular, proper maintenance and a clear understanding of the correct use of the device.
6.C.1 General Principles
Particular caution must be exercised during installation, modification, and repair, as well as during use of the equipment. In order to ensure safe operation, all electrical equipment must be installed and maintained in accordance with the provisions of the National Electrical Code (NEC) of the National Fire Protection Association (NFPA, 1991a). Laboratory workers should also consult state and local codes and regulations, which may contain special provisions and be more stringent than the NEC and NFPA rules. All repair and calibration work on electrical equipment must be carried out by properly trained and qualified personnel. Before modification, installation, or even minor repairs of electrical equipment are carried out, the devices must be deenergized and all capacitors discharged safely. Furthermore, this deenergized and/or discharged condition must be verified before proceeding (note that OSHA Control of Hazardous Energy Standard (29 CFR 1910.147; Lock out/Tag out) applies).
It is imperative that each person participating in any experiment involving the use of electrical equipment be aware of all applicable equipment safety issues and be briefed on any potential problems. Workers can significantly reduce hazards and dangerous behavior by following some basic principles and techniques: checking and rechecking outlet receptacles (section 6.C.1.1), making certain that wiring complies with national standards and recommendations (section 6.C.1.2), and reviewing general precautions (section 6.C.1.3) and personal safety techniques (section 6.C.1.4).
6.C.1.1 Outlet Receptacles
All 110-volt (V) outlet receptacles in laboratories should be of the standard design that accepts a three-
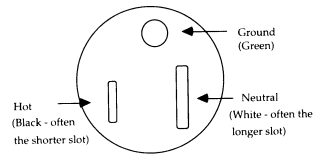
FIGURE 6.1 Standard design for a three-wire grounded outlet.
prong plug and provides a ground connection. Two-prong receptacles should be replaced as soon as feasible, and a separate ground wire should be added so that each receptacle is wired as shown in Figure 6.1. The ground wire should be on top so that anything falling onto the plug will not fall onto either the hot or the neutral line.
It is also possible to fit a receptacle with a ground fault circuit interrupter (GFCI), which disconnects the current if a ground fault is detected. GFCI devices are required by local electrical codes for outdoor receptacles and for selected laboratory receptacles located less than 6 feet (1.83 meters) from sinks if maintenance of a good ground connection is essential for safe operation. These devices differ in operation and purpose from fuses and circuit breakers, which are designed primarily to protect equipment and prevent electrical fires due to short circuits or other abnormally high current draw situations. Certain types of GFCIs can cause equipment shutdowns at unexpected and inappropriate times; hence, their selection and use need careful planning.
Receptacles that provide electric power for operations in hoods should be located outside the hood. This location prevents the production of electrical sparks inside the hood when a device is plugged in or disconnected, and it also allows a laboratory worker to disconnect electrical devices from outside the hood in case of an accident. Cords should not dangle outside the hood in such a way that they can accidentally be pulled out of their receptacles or tripped over. Simple, inexpensive plastic retaining strips and ties can be used to route cords safely. For fume hoods with airfoils, the electrical cords should be routed under the bottom airfoil so that the sash can be closed completely. Most airfoils can be easily removed and replaced with a screwdriver.
6.C.1.2 Wiring
Laboratory equipment plugged into a 110-V (or higher) receptacle should be fitted with a standard three-conductor line cord that provides an independent ground connection to the chassis of the apparatus (see Figure 6.2). All electrical equipment should be grounded unless it is "double-insulated." This type of equipment has a two-conductor line cord that meets national codes and standards. The use of two-pronged "cheaters" to connect equipment with three-prong grounded plugs to old-fashioned two-wire outlets should be prohibited.
The use of extension cords should be limited to temporary (less than one day) setups, if they are permitted at all. A standard three-conductor extension cord of sufficient rating for the connected equipment with an independent ground connection should be used. Electrical cables should be installed properly, even if only for temporary use, and should be kept out of aisles and other traffic areas. Overhead racks and floor channel covers should be installed if wires must pass over or under walking areas. Signal and power cables should not be intermingled in cable trays or panels. Special care is needed when installing and placing water lines (used, for example, to cool such equipment as flash lamps for lasers) so that they do not leak or produce condensation, which can dampen power cables nearby.
Equipment plugged into an electrical receptacle should include a fuse or other overload protection device to disconnect the circuit if the apparatus fails or is overloaded. This overload protection is particularly useful for equipment likely to be left on and unattended for a long time, such as variable autotransformers (e.g., Variacs and powerstats), vacuum pumps, drying ovens, stirring motors, and electronic instruments. Equipment that does not contain its own built-in overload protection should be modified to provide such protection or replaced with equipment that provides it. Overload protection does not protect the worker from electrocution, but it does reduce the risk of fire.
6.C.1.3 General Precautions for Working with Electrical Equipment
Laboratory personnel should be certain that all electrical equipment is maintained well, properly located, and safely used. In order to do this, the following precautions should be reviewed and the necessary adjustments made prior to working in the laboratory:
-
Insulate all electrical equipment properly. Visually inspect all electrical cords monthly, especially in any laboratory where flooding can occur. Keep in mind that rubber-covered cords can be eroded by organic solvents and by ozone (produced by ultraviolet lamps).
-
Replace all frayed or damaged cords before any
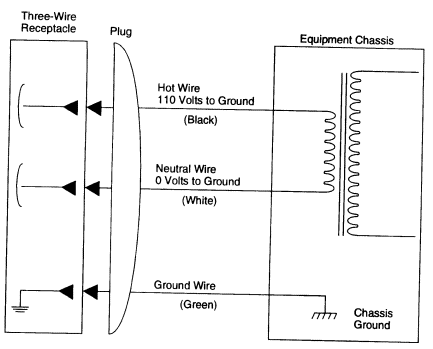
FIGURE 6.2 Standard wiring convention for 110-V electric power to equipment.
-
further use of the equipment is permitted. Replacement should be conducted by qualified personnel.
-
Ensure the complete electrical isolation of electrical equipment and power supplies. Enclose all power supplies in a manner that makes accidental contact with power circuits impossible. In every experimental setup, including temporary ones, employ suitable barriers or enclosures to protect against accidental contact with electrical circuits.
-
Equip motor-driven electrical equipment used in a laboratory where volatile flammable materials may be present (e.g., a hydrogenation room) with either nonsparking induction motors that meet Class 1, Division 2, Group C-D electrical standards (U.S. DOC, 1993) or air motors instead of series-wound motors that use carbon brushes, such as those generally used in vacuum pumps, mechanical shakers, stirring motors, magnetic stirrers, and rotary evaporators.
-
Do not use variable autotransformers to control the speed of an induction motor because such operation will cause the motor to overheat and perhaps start a fire.
-
Because series-wound motors cannot be modified to make them spark-free, do not use kitchen appliances (refrigerators, mixers, blenders, and so on) with such motors in laboratories where flammable materials may be present.
-
When bringing ordinary electrical equipment such as vacuum cleaners and portable electric drills having series-wound motors into the laboratory for special purposes, take specific precautions to ensure that no flammable vapors are present before such equipment is used (see Chapter 5, section G).
-
Locate electrical equipment so as to minimize the possibility of spills onto the equipment or flammable vapors carried into it. If water or any chemical is spilled on electrical equipment, shut off the power immediately at a main switch or circuit breaker and unplug the apparatus.
-
Minimize the condensation that may enter electrical equipment if it is placed in a cold room or a large refrigerator. Cold rooms pose a particular risk in this respect because the atmosphere is frequently at a high relative humidity, and the potential for water condensation is significant.
-
If electrical equipment must be placed in such areas, mount the equipment on a wall or vertical panel. This precaution will reduce, though not eliminate, the condensation problem.
-
Condensation can also cause electrical equipment to overheat, smoke, or catch fire. In such a case, shut off the power to the equipment immediately at a main switch or circuit breaker and unplug the apparatus.
-
To minimize the possibility of electrical shock, carefully ground the equipment using a suitable flooring material, and install ground-fault circuit interrupters (GFCIs).
-
Always unplug equipment before undertaking any adjustments, modifications, or repairs (with the exception of certain instrument adjustments as indicated in section 6.C.7). When it is necessary to handle equipment that is plugged in, be certain hands are dry
-
and, if feasible, wear nonconductive gloves and shoes with insulated soles.
-
Ensure that all workers know the location and operation of power shutoffs (i.e., main switches and circuit breaker boxes) for areas in which they work. Do not use equipment again until it has been cleaned and properly inspected.
ACETONE SPILLED UNDER AN ELECTRONIC BALANCE Acetone spilled out of a reaction vessel during the addition of dry ice. It seeped underneath a nearby electronic balance and ignited. The balance was severely damaged, but the fire was extinguished before the reaction vessel broke. |
All laboratories should have access to a qualified technician who can make routine repairs to existing equipment and modifications to new or existing equipment so that it will meet acceptable standards for electrical safety. The National Fire Protection Association's National Electrical Code Handbook (NFPA, 1993) provides guidelines.
6.C.1.4 Personal Safety Techniques for Use with Electrical Equipment
Each individual working with electrical equipment should be informed of basic precautionary steps that should be taken to ensure personal safety:
-
Avoid contact with energized electrical circuits. Electrical equipment should be serviced only by qualified individuals.
-
Before qualified individuals service electrical equipment in any way, disconnect the power source to avoid the danger of electric shock. Ensure that any capacitors are, in fact, discharged.
-
Before reconnecting electrical equipment to its power source after servicing, check the equipment with a suitable tester, such as a multimeter, to ensure that it is properly grounded.
-
Do not reenergize a circuit breaker until there is assurance that the short circuit that activated it has been corrected.
-
Install ground-fault circuit interrupters (GCFIs) as required by code to protect users from electric shock, particularly if an electrical device is hand-held during a laboratory operation.
-
If a person is in contact with a live electrical conductor, first disconnect the power source and then remove the person from the contact and administer first aid.
6.C.1.5 Additional Safety Techniques for Equipment Using High Current or High Voltage
Unless laboratory personnel are specially trained to install or repair high-current or high-voltage equipment, such tasks should be reserved for trained electrical workers. The following reminders are included for qualified personnel.
-
Always assume that a voltage potential exists within a device while servicing it, even if it is deenergized and disconnected from its power source. For example, a device may contain capacitors, which retain a potentially harmful electrical charge.
-
If it is not awkward or otherwise unsafe to do so, try to work with only one hand while keeping the other hand at your side or in a pocket, away from all conducting materials. This precaution reduces the likelihood of accidents that result in current passing through the chest cavity.
-
Avoid becoming grounded by staying at least 6 inches away from walls, water, and all metal materials including pipes.
-
Use voltmeters and test equipment with ratings and leads sufficient to measure the highest potential voltage to be found inside the equipment being serviced.
6.C.2 Vacuum Pumps
Distillations or concentration operations that involve significant quantities of volatile substances should normally be performed with the use of a facility vacuum system, a water aspirator, or a steam aspirator-each system protected by a suitable trapping device-rather than a mechanical vacuum pump. However, the distillation of less-volatile substances, removal of final traces of solvents, and some other operations that require pressures lower than those obtainable with a water aspirator are normally performed with a mechanical vacuum pump. The suction line from the system to the vacuum pump should be fitted with a cold trap to collect volatile substances from the system and to minimize the amount of material that enters the vacuum pump and dissolves in the pump oil. A cold trap should also be used with a water aspirator to minimize contamination of discharged water. The possibility that mercury will be swept into the pump as a result of a sudden loss of vacuum can be minimized by placing
a trap in the line to the pump. Vacuum pump oil contaminated with mercury must be treated as hazardous waste. (See Chapter 5, sections 5.C.11.8 and 5.D.)
The output of each pump should be vented to an air exhaust system. This procedure is essential when the pump is being used to evacuate a system containing a volatile toxic or corrosive substance. Failure to observe this precaution would result in pumping any of the substance that is not trapped into the laboratory atmosphere. It is also recommended to scrub or absorb the gases exiting the pump. Even with these precautions, however, volatile toxic or corrosive substances may accumulate in the pump oil and, thus, be discharged into the laboratory atmosphere during future pump use. This hazard can be avoided by draining and replacing the pump oil when it becomes contaminated. The contaminated pump oil should be disposed of by following standard RCRA procedures for the safe disposal of toxic or corrosive substances. General-purpose laboratory vacuum pumps should have a record of use in order to prevent cross-contamination or reactive chemical incompatibility problems.
Belt-driven mechanical pumps with exposed belts must have protective guards. Such guards are particularly important for pumps installed on portable carts or tops of benches where laboratory workers might accidentally entangle clothing or fingers in the moving belt, but they are not necessary for enclosed pumps.
6.C.3 Refrigerators and Freezers
The potential hazards posed by laboratory refrigerators involve vapors from the contents, the possible presence of incompatible chemicals, and spillage. As general precautions, laboratory refrigerators should be placed against fire-resistant walls, should have heavy-duty cords, and preferably should be protected by their own circuit breaker. The contents of a laboratory refrigerator should be enclosed in unbreakable secondary containers. Because there is almost never a satisfactory arrangement for continuously venting the interior atmosphere of a refrigerator, any vapors escaping from vessels placed in one will accumulate in the refrigerated space and will gradually be absorbed into the surrounding insulation. Thus, the atmosphere in a refrigerator could contain an explosive mixture of air and the vapor of a flammable substance or a dangerously high concentration of the vapor of a toxic substance or both. The potential for exposure to toxic substances can be aggravated when a worker places his or her head inside a refrigerator while searching for a particular sample. The placement of potentially explosive (see Chapter 5, sections 5.C and 5.G) or highly toxic substances (see Chapter 5, sections 5.D and 5.E) in a laboratory refrigerator is strongly discouraged. If this precaution must be violated, then a clear, prominent warning sign should be placed on the outside of the refrigerator door. Storage of these types of materials in a refrigerator should be kept to a minimum and monitored regularly. As noted in Chapter 5, section 5.C, laboratory refrigerators and freezers should never be used to store food or beverages for human consumption.
AMPOULE EXPLOSION IN A REFRIGERATOR The door to a refrigerator used for storage of chemicals in a laboratory was left open for 10 minutes while a researcher searched through chemicals. Suddenly, an ampoule stored in the door exploded, spraying the contents in all directions, including toward the researcher. Fortunately, only one other container was ruptured, and the researcher received only a cut on his face from flying glass. A review of the incident concluded that the ampoule had been sealed at a relatively low temperature. When the ampoule warmed up in the open door, pressure built up inside it, causing it to rupture. |
There should be no potential sources of electrical sparks on the inside of a laboratory refrigerator where volatile or flammable chemicals are stored. Only refrigerators that have been Underwriters-approved for flammable storage by the manufacturer should be used for this purpose. If this is not possible, all new or existing manual defrost refrigerators should be modified by
-
removing the interior light and switch mounted on the door frame, if present, and
-
moving the contacts of the thermostat controlling the fan and temperature outside the refrigerated compartment.
Although a prominent sign warning against the storage of flammable substances can be permanently attached to the door of an unmodified refrigerator, this alternative is less desirable than modifying the equipment by removing any spark sources from the refrigerated compartment. "Frost-free" refrigerators are not suitable for laboratory use, owing to the problems associated with attempts to modify them. Many of these refrigerators have a drain tube or hole that carries water (and any flammable material present) to an area adjacent to the compressor and, thus, present
a spark hazard. The electric heaters used to defrost the freezing coils are also a potential spark hazard (see Chapter 5, section 5.G.1). To ensure its effective functioning, a freezer should be defrosted manually when ice builds up.
Uncapped containers of chemicals should never be placed in a refrigerator. Caps should provide a vapor-tight seal to prevent a spill if the container is tipped over. Aluminum foil, corks, corks wrapped with aluminum foil, and glass stoppers usually do not meet these criteria, and, therefore, their use should be discouraged. The most satisfactory temporary seals are normally screw-caps lined with either a conical polyethylene insert or a Teflon insert. The best containers for samples that are to be stored for longer periods of time are sealed, nitrogen-filled glass ampoules. At a minimum, catch pans should be used for secondary containment.
Careful labeling of samples placed in refrigerators and freezers with both the contents and the owner's name is essential. Water-soluble ink should not be used, and labels should be waterproof or covered with transparent tape. Storing samples with due consideration of chemical compatibility is important in these often small, crowded spaces.
6.C.4 Stirring and Mixing Devices
The stirring and mixing devices commonly found in laboratories include stirring motors, magnetic stirrers, shakers, small pumps for fluids, and rotary evaporators for solvent removal. These devices are typically used in laboratory operations that are performed in a hood, and it is important that they be operated in a way that precludes the generation of electrical sparks. Furthermore, it is important that, in the event of an emergency, such devices can be turned on or off from a location outside the hood. Heating baths associated with these devices (e.g., baths for rotary evaporators) should also be spark-free and controllable from outside the hood. (See sections 6.C.1 and 6.C.5; also see Chapter 5, section 5.C.7.)
Only spark-free induction motors should be used in power stirring and mixing devices or any other rotating equipment used for laboratory operations. Although the motors in most of the currently marketed stirring and mixing devices meet this criterion, their on-off switches and rheostat-type speed controls can produce an electrical spark any time they are adjusted, because they have exposed contacts. Many of the magnetic stirrers and rotary evaporators currently on the market have this disadvantage. An effective solution is to remove any switches located on the device and insert a switch in the cord near the plug end; because the electrical receptacle for the plug should be outside the hood, this modification ensures that the switch will also be outside the hood. The speed of an induction motor operating under a load should not be controlled by a variable autotransformer.
Because stirring and mixing devices, especially stirring motors and magnetic stirrers, are often operated for fairly long periods without constant attention, the consequences of stirrer failure, electrical overload, or blockage of the motion of the stirring impeller should be considered. It is good practice to attach a stirring impeller to the shaft of the stirring motor by using lightweight rubber tubing. If the motion of the impeller becomes impeded, the rubber can twist away from the motor shaft. If this occurs, the motor will not stall. However, this practice does not always prevent binding the impeller. Hence, it is also desirable to fit unattended stirring motors with a suitable fuse or thermal-protection device. (Also see section 6.C.1.)
6.C.5 Heating Devices
Perhaps the most common types of electrical equipment found in a laboratory are the devices used to supply the heat needed to effect a reaction or a separation. These include ovens, hot plates, heating mantles and tapes, oil baths, salt baths, sand baths, air baths, hot-tube furnaces, hot-air guns, and microwave ovens. The use of steam-heated devices rather than electrically heated devices is generally preferred whenever temperatures of 100 °C or less are required. Because they do not present shock or spark risks, they can be left unattended with assurance that their temperature will never exceed 100 °C.
A number of general precautions need to be taken when working with heating devices in the laboratory. First, new or existing variable autotransformers should be wired (or rewired) as illustrated in Figure 6.3. The actual heating element in any laboratory heating device should be enclosed in a glass, ceramic, or insulated metal case in such a fashion as to prevent a laboratory worker or any metallic conductor from accidentally touching the wire carrying the electric current. This type of construction minimizes the risk of electric shock and of accidentally producing an electrical spark near a flammable liquid or vapor (see Chapter 5, section 5.G.1). It also diminishes the possibility that a flammable liquid or vapor will come into contact with any wire whose temperature may exceed its ignition temperature. If any heating device becomes so worn or damaged that its heating element is exposed, the device should be either discarded or repaired to correct the damage before it is used again. Because many household appliances (e.g., hot plates and space heaters) do not meet this criterion, they should not be used in a
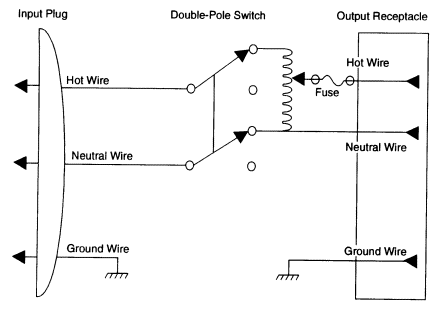
FIGURE 6.3 Schematic diagram of properly wired variable autotransformers.
laboratory. Resistance devices used to heat oil baths should not contain bare wires.
Laboratory heating devices should be used with a variable autotransformer to control the input voltage by supplying some fraction of the total line voltage, typically 110 V, to the heating element of the device. If a variable autotransformer is not wired in this manner, the switch on it may or may not disconnect both wires of the output from the 110 V line when it is switched to the off position. Also, if this wiring scheme has not been followed, and especially if the grounded three-prong plug is not used, even when the potential difference between the two output lines is only 10 V, each output line may be at a relatively high voltage (e.g., 110 V and 100 V) with respect to an electrical ground. Because these potential hazards exist, whenever a worker uses a variable autotransformer whose wiring scheme is not known, it is prudent to assume that either of the output lines carries a potential of 110 V and is capable of delivering a lethal electric shock.
The external cases of all variable autotransformers have perforations for cooling by ventilation, and some sparking may occur whenever the voltage adjustment knob is turned. Therefore, these devices should be located where water and other chemicals cannot be spilled onto them and where their movable contacts will not be exposed to flammable liquids or vapors. Variable autotransformers should be mounted on walls or vertical panels and outside of hoods; they should not simply be placed on laboratory benchtops.
Because the electrical input lines, including lines from variable transformers, to almost all laboratory heating devices have a potential of 110 V with respect to any electrical ground, these lines should always be viewed both as potential shock hazards and as potential spark hazards. Thus, any connection from these lines to a heating device should be both mechanically and electrically secure and completely covered with insulating material. Alligator clips should not be used to connect a line cord from a variable autotransformer to a heating device, especially to an oil bath or an air bath, because such connections pose a shock hazard. They also may slip off, creating an electrical spark and, perhaps, contacting other metal parts to create an additional hazard. All connections should be made by using, preferably, a plug and receptacle combination, or wires with insulated terminals firmly secured to insulated binding posts.
Whenever an electrical heating device is used, it is essential to use either a temperature controller or a temperature-sensing device that will turn off the electric power if the temperature of the heating device exceeds some preset limit. Similar control devices are available that will turn off the electric power if the flow of cooling water through a condenser is stopped owing to the loss of water pressure or loosening of the water supply hose to a condenser. Fail-safe devices, which can be either purchased or fabricated, can prevent the more serious problems of fires or explosions that may arise if the temperature of a reaction increases significantly because of a change in line voltage, the accidental loss of reaction solvent, or loss of cooling. Fail-safe devices should be used for stills employed to purify reaction solvents, because such stills are often left unattended for significant periods of time.
(See section 6.C.1 for additional information.)
6.C.5.1 Ovens
Electrically heated ovens are commonly used in the laboratory to remove water or other solvents from chemical samples and to dry laboratory glassware. Never use laboratory ovens for human food preparation.
Laboratory ovens should be constructed such that their heating elements and their temperature controls are physically separated from their interior atmospheres. Small household ovens and similar heating devices usually do not meet these requirements and, consequently, should not be used in laboratories. With the exception of vacuum drying ovens, laboratory ovens rarely have a provision for preventing the discharge of the substances volatilized in them into the laboratory atmosphere. Thus, it should be assumed that these substances will escape into the laboratory atmosphere and may also be present in concentrations sufficient to form explosive mixtures with the air inside the oven (see Chapter 5, section 5.G). This hazard can be reduced by connecting the oven vent directly to an exhaust system.
Ovens should not be used to dry any chemical sample that has even moderate volatility and might pose a hazard because of acute or chronic toxicity unless special precautions have been taken to ensure continuous venting of the atmosphere inside the oven. Thus, most organic compounds should not be dried in a conventional unvented laboratory oven.
To avoid explosion, glassware that has been rinsed with an organic solvent should not be dried in an oven until it has been rinsed again with distilled water. Potentially explosive mixtures can be formed from volatile substances and the air inside an oven.
Bimetallic strip thermometers are preferred for monitoring oven temperatures. Mercury thermometers should not be mounted through holes in the tops of ovens so that the bulb hangs into the oven. Should a mercury thermometer be broken in an oven of any type, the oven should be closed and turned off immediately, and it should remain closed until cool. All mercury should be removed from the cold oven with the use of appropriate cleaning equipment and procedures (see Chapter 5, section 5.C.11.8) in order to avoid mercury exposure. After removal of all visible mercury, the heated oven should be monitored in a fume hood until the mercury vapor concentration drops below the threshold limit value (TLV).
6.C.5.2 Hot Plates
Laboratory hot plates are normally used when solutions are to be heated to 100 °C or above and the inherently safer steam baths cannot be used as the source of heat. As previously noted, only hot plates that have completely enclosed heating elements should be used in laboratories. Although almost all laboratory hot plates now sold meet this criterion, many older ones pose an electrical spark hazard arising from either the on-off switch located on the hot plate, the bimetallic thermostat used to regulate the temperature, or both. Normally, these two spark sources are both located in the lower part of the hot plate in a region where any heavier-than-air and possibly flammable vapors evolved from a boiling liquid on the hot plate would tend to accumulate. In principle, these spark hazards can be alleviated by enclosing all mechanical contacts in a sealed container or by using solid-state circuitry for switching and temperature control. However, in practice, such modifications are difficult to incorporate into many of the hot plates now in use. Laboratory workers should be warned of the spark hazard associated with these hot plates. Any newly purchased hot plates should be set up in a way that avoids electrical sparks. In addition to the spark hazard, old and corroded bimetallic thermostats in these devices can eventually fuse shut and deliver full, continuous current to a hot plate. This risk can be avoided by wiring a fusible coupling into the line inside the hot plate. If the device does overheat, then the coupling will melt and interrupt the current (see Section 6.C.1).
On many brands of combined stirrer/hot plates, the controls for the stirrer and temperature control look alike. Care must be taken to distinguish their functions. A fire or explosion may occur if the temperature rather than the stirrer speed is increased inadvertently.
6.C.5.3 Heating Mantles
Heating mantles are commonly used for heating round-bottomed flasks, reaction kettles, and related reaction vessels. These mantles enclose a heating element in a series of layers of fiberglass cloth. As long as the fiberglass coating is not worn or broken, and as long as no water or other chemicals are spilled into the mantle (see section 6.C.1), heating mantles pose no shock hazard. They are normally fitted with a male plug that fits into a female receptacle on an output line from a variable autotransformer. This plug combination provides a mechanically and electrically secure connection.
Heating mantles should always be used with a variable autotransformer to control the input voltage. They must never be plugged directly into a 110-V line. Workers should be careful not to exceed the input voltage recommended by the mantle manufacturer. Higher voltages will cause it to overheat, melting the fiberglass insulation and exposing the bare heating element.
Some heating mantles are constructed by encasing the fiberglass mantle in an outer metal case that provides physical protection against damage to the fiberglass. If such metal-enclosed mantles are used, it is good practice to ground the outer metal case either by using a grounded, three-conductor cord from the variable autotransformer or by securely affixing one end of a heavy, braided conductor to the mantle case and the other end to a known electrical ground. This practice protects the worker against an electric shock if the heating element inside the mantle shorts against the metal case.
6.C.5.4 Oil, Salt, and Sand Baths
In the use of oil, salt, and sand baths, care must be taken to avoid spilling water and other volatile substances into the baths. Such an accident can splatter hot material over a wide area and cause serious injuries.
Electrically heated oil baths are often used to heat small or irregularly shaped vessels or when a stable heat source that can be maintained at a constant temperature is desired. For temperatures below 200 °C, a saturated paraffin oil is often used; a silicone oil should be used for temperatures up to 300 °C. Care must be taken with hot oil baths not to generate smoke or have the oil burst into flames from overheating. An oil bath should always be monitored by using a thermometer or other thermal sensing device to ensure that its temperature does not exceed the flash point of the oil being used. For the same reason, oil baths left unattended should be fitted with thermal sensing devices that will turn off the electric power if the bath overheats. These baths should be heated by an enclosed heating element, such as a knife heater, a tubular immersion heater such as a Calrod®, or its equivalent. The input connection for this heating element should be a male plug that will fit a female receptacle from a variable autotransformer (e.g., Variac) output line. Alternatively, a temperature controller can be used to control the temperature of the bath precisely. Temperature controllers are now available that can provide a variety of heating and cooling options.
Oil baths must be well mixed to ensure that there are no ''hot spots" around the elements that take the surrounding oil to unacceptable temperatures. This problem can be minimized by placing the thermoregulator fairly close to the heater. Heated oil should be contained in either a metal pan or a heavy-walled porcelain dish; a Pyrex dish or beaker can break and spill hot oil if struck accidentally with a hard object. The oil bath should be mounted carefully on a stable horizontal support such as a laboratory jack that can be
THERMITE REACTION EXPLOSION An explosion injuring 27 people occurred when a thermite reaction was being demonstrated as part of a magic show at an engineering open house. The demonstration, which generated molten iron in a 2,500 to 3,000 °C reaction, was being carried out in a clay flowerpot above a beaker of water and sand to show the heat produced by the reaction when molten iron particles fall into water. Suddenly, the demonstration exploded, sending hot metal and water toward the audience. The most likely cause of the accident was thought to be a physical vapor explosion, which can occur when a very hot liquid comes into contact with a second liquid. In this case, the water may have turned to steam so rapidly that an explosion resulted. The injuries consisted of minor burns. |
raised or lowered easily without danger of the bath tipping over. It is also important that equipment always be clamped high enough above a hot plate or oil bath that if the reaction begins to overheat, the heater can be lowered immediately and replaced with a cooling bath without having to readjust the clamps holding the equipment setup. A bath should never be supported on an iron ring because of the greater likelihood of accidentally tipping the bath over. Secondary containment should be provided in the event of a spill of hot oil. Proper protective gloves should be worn when handling a hot bath.
Molten salt baths, like hot oil baths, offer the advantages of good heat transfer, commonly have a higher operating range (e.g., 200 to 425 °C), and may have a high thermal stability (e.g., 540 °C). The reaction container used in a molten salt bath must be able to withstand a very rapid heat-up to a temperature above the melting point of the salt. Care must be taken to keep salt baths dry, because they are hygroscopic, a property that can cause hazardous popping and splattering if the absorbed water vaporizes during heat-up.
6.C.5.5 Hot Air Baths and Tube Furnaces
Hot air baths can be useful heating devices. Nitrogen is preferred for reactions in which flammable materials are used. Electrically heated air baths are frequently used to heat small or irregularly shaped vessels. Because of their inherently low heat capacity, such baths normally must be heated considerably above the
desired temperature (100 °C or more) of the vessel being heated. These baths should be constructed so that the heating element is completely enclosed and the connection to the air bath from the variable autotransformer is both mechanically and electrically secure. These baths can be constructed from metal, ceramic, or, less desirably, glass vessels. If a glass vessel is used, it should be wrapped thoroughly with a heat-resistant tape so that if the vessel breaks accidentally, the glass will be contained and the bare heating element will not be exposed. Fluidized sand baths are usually preferred over air baths.
Tube furnaces are often used for high-temperature reactions under reduced pressure. The proper choice of glassware or metal tubes and joints is required, and the procedures should conform to safe practice with electrical equipment and evacuated apparatus.
(See also section 6.C.1 and Chapter 5, section 5.G.2.5.)
6.C.5.6 Heat Guns
Laboratory heat guns are constructed with a motor-driven fan that blows air over an electrically heated filament. They are frequently used to dry glassware or to heat the upper parts of a distillation apparatus during distillation of high-boiling materials. The heating element in a heat gun typically becomes red-hot during use and, necessarily, cannot be enclosed. Also, the on-off switches and fan motors are not usually spark-free. For these reasons, heat guns almost always pose a serious spark hazard (see Chapter 5, section 5.G.1). They should never be used near open containers of flammable liquids, in environments where appreciable concentrations of flammable vapors may be present, or in hoods used to remove flammable vapors. Household hair dryers may be substituted for laboratory heat guns only if they have three-conductor line cords or are double-insulated. Any hand-held heating device of this type that will be used in a laboratory should have ground-fault circuit interrupter (GFCI) protection to ensure against electric shock.
6.C.5.7 Microwave Ovens
To avoid exposure to microwaves, ovens should never be operated with doors open. Wires and other objects should not be placed between the sealing surface and the door on the oven's front face. The sealing surfaces must be kept absolutely clean. To avoid electrical hazards, the oven must be grounded. If use of an extension cord is necessary, only a three-wire cord with a rating equal to or greater than that for the oven should be used. To reduce the risk of fire in the oven, samples must not be overheated. The oven must be closely watched when combustible materials are in it. Metal containers or metal-containing objects (e.g., stir bars) should not be used in the microwave, because they can cause arcing.
Generally, sealed containers should not be heated in the oven, because of the danger of explosion. If sealed containers must be used, their materials must be selected carefully and the containers properly designed. Commercially available microwave acid digestion bombs, for example, incorporate a Teflon sample cup, a self-sealing Teflon O-ring, and a compressible pressure-relief valve. The manufacturer's loading limits must not be exceeded. For such applications, the microwave oven should be properly vented using an exhaust system. Placing a large item such as an oven inside a fume hood is not recommended.
Heating a container with a loosened cap or lid poses a significant risk. Microwave ovens can heat material (e.g., solidified agar) so quickly that, even though container lids may be loosened to accommodate expansion, the lid can seat upward against the threads and containers can explode. Screw-caps must be removed from containers being microwaved. If the sterility of the contents must be preserved, screw-caps may be replaced with cotton or foam plugs.
6.C.6 Ultrasonicators, Centrifuges, and Other Electrical Equipment
6.C.6.1 Ultrasonicators
The use of high-intensity ultrasound in the chemical laboratory has grown enormously during the past decade and has a diverse set of applications. Human exposure to ultrasound with frequencies of between 16 and 100 kilohertz (kHz) can be divided into three distinct categories: airborne conduction, direct contact through a liquid coupling medium, and direct contact with a vibrating solid.
Ultrasound through airborne conduction does not appear to pose a significant health hazard to humans. However, exposure to the associated high volumes of audible sound can produce a variety of effects, including fatigue, headaches, nausea, and tinnitus. When ultrasonic equipment is operated in the laboratory, the apparatus must be enclosed in a 2-cm-thick wooden box or in a box lined with acoustically absorbing foam or tiles to substantially reduce acoustic emissions (most of which are inaudible).
Direct contact of the body with liquids or solids subjected to high-intensity ultrasound of the sort used to promote chemical reactions should be avoided. (In contrast, ultrasound used for medical diagnostic imaging is relatively benign.) Under sonochemical conditions, cavitation is created in liquids, and it can induce high-energy chemistry in liquids and tissues. Cell death from
membrane disruption can occur even at relatively low acoustic intensities. Exposure to ultrasonically vibrating solids, such as an acoustic horn, can lead to rapid frictional heating and potentially severe burns.
6.C.6.2 Centrifuges
Centrifuges should be properly installed and must be operated only by trained personnel. It is important that the load be balanced each time the centrifuge is used and the lid be closed while the rotor is in motion. The disconnect switch must be working properly to shut off the equipment when the top is opened, and the manufacturer's instructions for safe operating speeds must be followed.
For flammable and/or hazardous materials, the centrifuge should be under negative pressure to a suitable exhaust system.
6.C.6.3 Electrical Instruments
Most modern electronic instruments have a cord that contains a separate ground wire for the chassis and are supplied with a suitable fuse or other overload protection. Any existing instrument that lacks these features should be modified to incorporate them. As is true for any electrical equipment, special precautions should be taken to avoid the possibility that water or other chemicals could be spilled into these instruments.
Under most circumstances, any repairs to, adjustments to, or alterations of such instruments should be made only by a qualified individual. Laboratory workers should not undertake such adjustments unless they have received certification as well as specific training for the particular instrument to be serviced. If laboratory workers do undertake repairs, the cord should always be unplugged before any disassembly begins. However, certain adjustments can be made only when the instrument is connected to a power source. Appropriate protective measures and due diligence are required when working on energized devices. Extra precautions are particularly important for instruments that incorporate high-voltage circuitry.
Many electrical instruments, such as lasers and x-ray, E-beam, radioactive, photochemical, and electrophoresis equipment, emit potentially harmful radiation, and, therefore, special precautions must be followed when they are used. This equipment should be used and serviced only by trained personnel.
(See section 6.C.1 and Chapter 5, section 5.E.)
6.C.7 Electromagnetic Radiation Hazards
Equipment found in laboratories that can produce hazardous amounts of electromagnetic radiation includes ultraviolet lamps, arc lamps, heat lamps, lasers, microwave and radio-frequency sources, and x-rays and electron beams.
6.C.7.1 Visible, Ultraviolet, and Infrared Laser Light Sources
Overexposure to direct or reflected ultraviolet light, arc lamps, and infrared sources should be minimized by sealing or enclosing sources whenever possible. Appropriately rated safety glasses, goggles, or face shields should be worn for eye protection. Long-sleeved clothing and gloves should be worn to protect arms and hands.
Control measures for the safe use of lasers have been established by the American National Standards Institute (ANSI) and presented in Safe Use of Lasers (ANSI Z136.1-1993), which describes the different types of laser hazards and the appropriate measures to control each type. Class IIIB and IV lasers should be operated only in posted laser-controlled areas. No one but the authorized operator of a laser system should ever enter a posted laser-controlled laboratory when the laser is in use.
6.C.7.2 Radio-frequency and Microwave Sources
Section 6.C.5.7 provides guidelines for the safe use of microwave ovens in the laboratory. Other devices in the laboratory can also emit harmful microwave or radio-frequency emissions. People working with these types of devices should be trained in their proper operation as well as measures to prevent exposure to harmful emissions. Shields and protective covers should be in proper position when the equipment is operating. Warning signs to protect people wearing heart pacemakers should be posted on or near these devices.
A laboratory worker removed the shield from a high-powered microwave-generating device. Fortunately, the emissions triggered the fire alarm system, prompting an evacuation of the laboratory. Had the exposure continued, the person could have suffered severe injury. |
6.C.7.3 X-rays, E-beams, and Sealed Sources
X-rays and electron beams (E-beams) are used in a variety of laboratory equipment, mostly for analytical operations. The equipment is government-regulated. In most cases, registration and licensing are required. Personnel operating or working in the vicinity of these
types of equipment should have appropriate training to minimize the risk of their being exposed to harmful ionizing radiation.
6.C.7.4 Miscellaneous Physical Hazards Presented by Electrically Powered Equipment
6.C.7.4.1
Magnetic Fields
If an object moves into the attractive field of a strong magnet, it can become a projectile when it is pulled rapidly toward the magnet. Therefore, objects ranging from keys, scissors, knives, wrenches, and other tools to oxygen cylinders, buffing machines, and wheelchairs and other ferromagnetic objects must be excluded from the immediate vicinity of the magnet, for the sake of both safety and data quality, in the case of NMR.
Even relatively small peripheral magnetic fields can adversely affect credit cards, computer disks, and other magnetic objects, as summarized in Table 6.1. It is prudent to post warnings at the 5-gauss (G) line and to limit access to areas with more than 10 to 20 G to knowledgeable staff. People wearing heart pacemakers and other electronic or electromagnetic prosthetic devices should be kept away from strong electromagnetic sources.
Superconducting magnets use liquid nitrogen and liquid helium coolants. Thus, the precautions associated with the use of cryogenic liquids must be observed as well. (Also see section 6.E.2.)
6.C.7.4.2
Rotating Equipment and Moving Parts
Injuries can result from bodily contact with rotating or moving objects, including mechanical equipment, parts, and devices. The risk of injury can be reduced through improved engineering, good housekeeping, and safe work practice and personal behavior. Laboratory workers must know how to shut down equipment in the event of an emergency; must enclose or shield hazardous parts, such as belts, chains, gears, and pulleys, with appropriate guards; and must not wear loose clothing, jewelry, or unrestrained long hair around machinery.
6.C.7.4.3
Cutting and Puncturing Tools
Hand injuries are probably the most frequently encountered injuries in laboratories. Many of these injuries can be prevented by keeping all cutting and puncturing devices fully protected, avoiding the use of razor blades as cutting tools, and using utility knives that have a spring-loaded guard that covers the blade. Razor blades, needles, and other sharp objects or instruments should be disposed of carefully rather than simply thrown into the trash bin unprotected.
Glass cuts can be minimized by use of correct procedures (for example, that for inserting glass tubing into rubber stoppers and tubing, which is taught in introductory laboratories), through appropriate use of protective equipment, and by careful attention to manipulation.
6.C.7.4.4
Noise Extremes
Any laboratory operation that produces significant noise (85 decibels or greater) needs a hearing conservation program to protect employees from excessive exposure, that is, exposure to significant noise for an 8-hour average duration. An audiologist or industrial hygienist should be consulted to determine the need for such a program and to provide assistance in developing one.
6.C.7.4.5
Slips, Trips, and Falls
The risks of slips, trips, falls, and collisions between persons and objects can be reduced by cleaning up
TABLE 6.1 Summary of Magnetic Field Effects
|
Level at Which Effects Occur (gauss) |
||
Effects on electron microscopes |
1 |
||
Disturbance of color computer displays |
1-3 |
||
Disturbance of monochrome computer displays |
3-5 |
||
Erasure of credit card and bank card coding |
10 |
||
Effects on watches and micromechanical devices |
10 |
||
Lowest known field effect on pacemakers |
17 |
||
Saturation of transformers and amplifiers |
50 |
||
Erasure of floppy disks |
350 |
||
SOURCE: Adapted from Site Planning Guide for Superconducting NMR Systems, Bruker Instruments (1992). |
liquid or solid spills immediately, keeping doors and drawers closed and passageways clear of obstructions, providing step stools, ladders, and lifts to reach high areas, and walking along corridors and on stairways at a normal pace. Wet floors around ice, dry ice, or liquid nitrogen dispensers should be carpeted and paper towel dispensers made available for wiping up drops or small puddles as soon as they form.
6.C.7.4.6
Ergonomics and Lifting
Both standing and sitting in a static posture and making repeated motions have been shown to cause a wide variety of musculoskeletal complaints. Problems due to poor ergonomics include eyestrain, stiff and sore back, leg discomfort, and hand and arm injuries. Each situation needs to be evaluated individually. However, personnel who spend significant time working on video display terminals should use furniture appropriate for these tasks, proper posture, and perhaps special eyeglasses. Also, people who use the same tools and/or hand motions for extended periods of time should take breaks at appropriate intervals to help prevent injuries.
Lifting injuries are one of the more common types of injuries for laboratory workers. The weight of the item to be lifted is a factor, but it is only one of several. The shape and size of an object as well as the lifting posture and the frequency of lifting are also key factors in determining the risks of lifting. The National Institute for Occupational Safety and Health (NIOSH) has developed a guide that should be consulted to help determine lifting safety (U.S. DHHS, 1994). Personnel who are at risk for lifting injuries should receive periodic training.
6.D WORKING WITH COMPRESSED GASES
6.D.1 Compressed Gas Cylinders
Precautions are necessary for handling the various types of compressed gases, the cylinders that contain them, the regulators used to control their flow, the piping used to confine them during flow, and the vessels in which they are ultimately used. Regular inventories of cylinders and checks of their integrity with prompt disposal of those no longer in use are important. (See Chapter 4, section 4.E.4, for information on storing gas cylinders, and Chapter 5, section 5.H, for discussion of the chemical hazards of gases.)
A compressed gas is defined as a material in a container with an absolute pressure greater than 276 kilo-pascals (kPa), or 40 psi (pounds per square inch) at 21 °C or an absolute pressure greater than 717 kPa (104 psi) at 54 °C, or both, or any liquid flammable material having a Reid vapor pressure greater than 276 kPa (40 psi) at 38 °C. The Department of Transportation (DOT) has established codes that specify the materials to be used for the construction and the capacities, test procedures, and service pressures of the cylinders in which compressed gases are transported. However, regardless of the pressure rating of the cylinder, the physical state of the material within it determines the pressure of the gas. For example, liquefied gases such as propane and ammonia will exert their own vapor pressure as long as any liquid remains in the cylinder and the critical temperature is not exceeded.
Prudent procedures for the use of compressed gas cylinders in the laboratory include attention to appropriate purchase, especially selecting the smallest cylinder compatible with the need, as well as proper transportation and storage, identification of contents, handling and use, and marking and return of the empty cylinder. The practice of purchasing unreturnable lecture bottles should be discouraged if that leads to accumulation of partially filled cylinders and disposal problems. Returnable cylinders should be purchased and returned as prescribed by the manufacturer.
6.D.1.1 Identification of Contents
The contents of any compressed gas cylinder should be identified clearly so as to be easily, quickly, and completely determined by any laboratory worker. Such identification should be stenciled or stamped on the cylinder itself, or a durable label should be provided that cannot be removed from the cylinder. No compressed gas cylinder should be accepted for use that does not identify its contents legibly by name. Color coding is not a reliable means of identification; cylinder colors vary from supplier to supplier, and labels on caps have no value because many caps are interchangeable. Care in the maintenance of cylinder labels is important because unidentified compressed gas cylinders may pose a high risk and present very high disposal costs. It is good practice to provide compressed gas cylinders with tags on which the names of users and dates of use can be entered. If the labeling on a cylinder becomes unclear or an attached tag is defaced and the contents cannot be identified, the cylinder should be marked "contents unknown" and the manufacturer contacted regarding appropriate procedures.
All gas lines leading from a compressed gas supply should be labeled clearly to identify the gas, the laboratory served, and relevant emergency telephone numbers. The labels, in addition to being dated, should be color-coded to distinguish hazardous gases—that is, flammable, toxic, or corrosive substances coded with a yellow background and black letters—from inert gases, which are coded with a green background and
black letters. Signs should be posted conspicuously in areas in which flammable compressed gases are stored, identifying the substances and appropriate precautions, for example:
HYDROGEN—FLAMMABLE GAS
NO SMOKING-NO—OPEN FLAMES
6.D.1.2 Handling and Use
Gas cylinders must be handled carefully to prevent accidents or damage to the cylinder. The valve protection cap should be left in place until the cylinder is secured and ready for use. Gas cylinders should not be dragged, rolled, slid, or allowed to strike each other forcefully. Cylinders should always be transported on wheeled cylinder carts with retaining straps or chains. The plastic mesh sleeves sometimes installed on cylinders by vendors are intended only to protect the paint on the cylinder and do not serve as a safety device.
Compressed gas cylinders should be secured firmly at all times. A clamp and belt or chain, securing the cylinder between "waist" and "shoulder" to a wall, are generally suitable for this purpose. In areas of seismic activity, gas cylinders should be secured both toward the top and toward the bottom. Cylinders should be individually secured; using a single restraint strap or chain around a number of cylinders is often not effective. Pressure-relief devices protecting equipment that is attached to cylinders of flammable, toxic, or otherwise hazardous gases should be vented to a safe place. (See Section 6.D.2.2.1 for details.)
Standard cylinder-valve outlet connections have been devised by the Compressed Gas Association (CGA) to prevent the mixing of incompatible gases due to an interchange of connections. The outlet threads used vary in diameter: some are internal and some are external; some are right-handed and some are left-handed. In general, right-handed threads are used for nonfuel and water-pumped gases, and left-handed threads are used for fuel and oil-pumped gases. Information on the standard equipment assemblies for use with specific compressed gases is available from the supplier. To minimize undesirable connections that may result in a hazard, only CGA standard combinations of valves and fittings should be used in compressed gas installations; the assembly of miscellaneous parts (even of standard approved types) should be avoided. Use of an "adapter" or cross-threading of a valve fitting should not be attempted. The threads on cylinder valves, regulators, and other fittings should be examined to ensure that they correspond to one another and are undamaged.
Cylinders should be placed so that the rotary cylinder valve handle at the top is accessible at all times. Cylinder valves should be opened slowly, and only when a proper regulator is firmly in place and the attachment has been shown to be leak-proof by an appropriate test (see Chapter 5, section 5.H). The cylinder valve should be closed as soon as the necessary amount of gas has been released. Valves should be either completely open or completely closed. Flow restrictors should be installed on gas cylinders to minimize the chance of excessive flows. The cylinder valve should never be left open when the equipment is not in use. This precaution is necessary not only for safety when the cylinder is under pressure, but also to prevent the corrosion and contamination that would result from diffusion of air and moisture into the cylinder after it has been emptied.
Most cylinders are equipped with hand-wheel valves. Those that are not should have a spindle key on the valve spindle or stem while the cylinder is in service. Only wrenches or other tools provided by the cylinder supplier should be used to remove a cylinder cap or to open a valve. In no case should a screwdriver be used to pry off a stuck cap or should pliers be used to open a cylinder valve. Some valve fittings require washers or gaskets, and the materials of construction should be checked before the regulator is fitted.
If the valve on a cylinder containing an irritating or toxic gas is being opened outside, the worker should stand upwind of the cylinder with the valve pointed downwind, away from him or herself, and should warn those working nearby in case of a possible leak. If the work is being done inside, the cylinder should be opened only in a fume hood or specially designed cylinder cabinet. A differential pressure switch with an audible alarm should be installed in any hood dedicated for use with toxic gases. In the event of hood failure, the pressure switch should activate an audible alarm warning the user of hood failure.
6.D.1.2.1
Preventing and Controlling Leaks
Cylinders, connections, and hoses should be checked regularly for leaks. To check for leaks, a flammable gas leak detector (for flammable gases only) or soapy water, or a 50% glycerin-water solution, is used to look for bubbles. At or below freezing temperatures, the glycerin solution should be used instead of soapy water. When the gas to be used in the procedure is a flammable oxidizing or highly toxic gas, the system should be checked first for leaks with an inert gas (helium or nitrogen) before introducing the hazardous gas.
The general procedures discussed in Chapter 5, section 5.C, can be used for relatively minor leaks, when
SPONTANEOUS IGNITION OF HYDROGEN Late one evening in a chemical engineering facility, a student employee was working near a six-cylinder hydrogen gas manifold when she heard a cracking sound above her, followed by a whistling sound. She stepped away from the cylinder area to where she could see above the roof and noticed a flame on the roof above the cylinders. She immediately reported this to her supervisor, who went up on the roof and found that a rupture disk on the hydrogen manifold had ruptured. Had the disk ruptured in the daylight, the flame might not have been visible. The most likely cause of the flame was the spontaneous ignition of the hydrogen as it entered the air at high pressure. The hydrogen manifold was shut down, the rupture disk was replaced, and research was resumed. |
the indicated action can be taken without exposing personnel to highly toxic substances. The leaking cylinder can be moved through populated portions of the building, if necessary, by placing a plastic bag, rubber shroud, or similar device over the top and taping it (preferably with duct tape) to the cylinder to confine the leaking gas. If there is any risk of exposure, the environmental health and safety office should be called and the area evacuated before the tank is moved.
If a leak at the cylinder valve handle cannot be remedied by tightening a valve gland or a packing nut, emergency action should be taken and the supplier should be notified. Laboratory workers should never attempt to repair a leak at the junction of the cylinder valve and the cylinder or at the safety device; rather, they should consult with the supplier for instructions.
When the nature of the leaking gas or the size of the leak constitutes a more serious hazard, a self-contained breathing apparatus and protective apparel may be required, and personnel may need to be evacuated (see Chapter 5, section 5.C.2). Cylinders leaking toxic gases always require protective equipment and evacuation of personnel. Cylinder coffins are also available to encapsulate leaking cylinders. (See Chapter 5, section 5.G, for more information.)
6.D.1.2.2 Pressure Regulators
Pressure regulators are strongly recommended to reduce a high-pressure supplied gas to a desirable lower pressure and to maintain a satisfactory delivery pressure and flow level for the required operating conditions. They can be obtained to fit many operating conditions over a range of supply and delivery pressures, flow capacities, and construction materials. All regulators are of a diaphragm type and are spring-loaded or gas-loaded, depending on pressure requirements. They can be single-stage or two-stage. Under no circumstances should oil or grease be used on regulator valves or cylinder valves because these substances may be reactive with some gases (e.g., oxygen).
Each regulator is supplied with a specific CGA standard inlet connection to fit the outlet connection on the cylinder valve for the particular gas. Regulators should be checked before use to be sure they are free of foreign objects and correct for the particular gas.
Regulators for use with noncorrosive gases are usually made of brass. Special regulators made of corrosion-resistant materials can be obtained for use with such gases as ammonia, boron trifluoride, chlorine, hydrogen chloride, hydrogen sulfide, and sulfur dioxide. Because of freeze-up and corrosion problems, regulators used with carbon dioxide gas must have special internal design features and be made of special materials. Regulators used with oxidizing agents must be cleaned specially to avoid the possibility of an explosion on contact of the gas with any reducing agent or oil left from the cleaning process.
All pressure regulators should be equipped with spring-loaded pressure-relief valves (see section 6.D.2.2.1 for further information on pressure-relief devices) to protect the low-pressure side. When used on cylinders of flammable, toxic, or otherwise hazardous gases, the relief valve should be vented to a hood or other safe location. The use of internal-bleed-type regulators should be avoided. Regulators should be removed from corrosive gases immediately after use and flushed with dry air or nitrogen. Mercury bubblers should not be used.
6.D.1.2.3
Flammable Gases
It is important to keep all sources of ignition away from cylinders of flammable gases and to ensure that these cylinders will not leak. A solution of soapy water should be used to detect leaks except during freezing weather, when a 50% glycerin-water solution or its equivalent should be used. Connections to piping, regulators, and other appliances should always be kept tight to prevent leakage, and the tubing or hoses used should be kept in good condition. Regulators, hoses, and other appliances used with cylinders of flammable gases should not be interchanged with similar equipment intended for use with other gases. Cylinders should be grounded properly to prevent static electricity buildup, especially in very cold or dry environ-
ments. All cylinders containing flammable gases should be stored in a well-ventilated place. Reserve stocks of such cylinders should never be stored in the vicinity of cylinders containing oxygen, fluorine, chlorine, or other oxidizing gases. Reaction vessels should be equipped with pressure-relief devices.
6.D.1.2.4
Empty Cylinders
A cylinder should never be emptied to a pressure lower than 172 kPa (25 psi) because the residual contents may become contaminated with air if the valve is left open. Empty cylinders should never be refilled by the user. Rather, the regulator should be removed, and the valve cap should be replaced. The cylinder should be clearly marked as empty (MT) and returned to a storage area for pickup by the supplier. Empty and full cylinders should not be stored in the same place.
Cylinder discharge lines should be equipped with approved check valves to prevent inadvertent contamination of cylinders that are connected to a closed system where the possibility of flow reversal exists. Backflow is particularly troublesome in the case of gases used as reactants in a closed system. A cylinder in such a system should be shut off and removed from the system while the pressure remaining in the cylinder is still greater than the pressure in the closed system. If there is a possibility that a cylinder has become contaminated, it should be so labeled and returned to the supplier.
6.D.2 Other Equipment Used with Compressed Gases
6.D.2.1 Records, Inspection, and Testing
High-pressure operations should be carried out only with equipment specifically built for this use and only by those trained especially to use this equipment. Reactions should never be carried out in, nor heat applied to, an apparatus that is a closed system unless it has been designed and tested to withstand pressure. To ensure that the equipment has been properly designed, each pressure vessel should have stamped on it, or on an attached plate, its maximum allowable working pressure, the allowable temperature at this pressure, and the material of construction. Similarly, the relief pressure and setting data should be stamped on a metal tag attached to installed pressure-relief devices, and the setting mechanisms should be sealed. Relief devices used on pressure regulators do not require these seals or numbers.
All pressure equipment should be tested or inspected periodically. The frequency of tests and/or inspections varies, depending on the type of equipment, how often it is used, and the nature of its usage. Corrosive or otherwise hazardous service requires more frequent tests and inspections. Inspection data should be stamped on or attached to the equipment.
Testing the entire assembled apparatus with soap solution and air or nitrogen pressure to the maximum allowable working pressure of the weakest section of the assembled apparatus can usually detect leaks at threaded joints, packings, and valves.
Before any pressure equipment is altered, repaired, stored, or shipped, it should be vented, and all toxic, flammable, or other hazardous material removed completely so it can be handled safely. Especially hazardous materials may require special cleaning techniques, which should be solicited from the distributor.
(See section 6.E.1 for further information.)
6.D.2.2 Assembly and Operation
During the assembly of pressure equipment and piping, only appropriate components should be used, and care should be taken to avoid strains and concealed fractures resulting from the use of improper tools or excessive force. Tubing in place in a pressure apparatus should not be used to support any significant weight.
Threads that do not fit exactly should not be forced (refer to section 6.D.1.2.1). Thread connections must match; tapered pipe threads cannot be joined with parallel machine threads. Teflon tape or a suitable thread lubricant should be used when assembling the apparatus (see section 6.D.2.2.6). However, oil or lubricant must never be used on any equipment that will be used with oxygen. Parts having damaged or partly stripped threads should be rejected (also see section 6.D.2.2.5).
In assembling copper tubing installations, sharp bends should be avoided and considerable flexibility should be allowed. Copper tubing hardens and cracks on repeated bending. Many metals can become brittle in hydrogen (H2) or corrosive gas service. Nickel alloys can generate Ni(CO)4 in some carbon monoxide atmospheres. All tubing should be inspected frequently and replaced when necessary.
Stuffing boxes and gland joints are a likely source of trouble in pressure installations. Particular attention should be given to the proper installation and maintenance of these parts, including the proper choice of lubricant and packing material.
Experiments carried out in closed systems and involving highly reactive materials, such as those subject to rapid polymerization (e.g., dienes or unsaturated aldehydes, ketones, or alcohols) should be preceded by small-scale tests using the exact reaction materials to determine the possibility of an unexpectedly rapid
reaction or unforeseen side reactions. All reactions under pressure should be shielded and should be carried out as remotely as possible, for example, with valve extensions and behind a heavy shield or with closed-circuit TV monitoring if needed.
Autoclaves and other pressure-reaction vessels should not be filled more than half full to ensure that space remains for expansion of the liquid when it is heated. Leak corrections or adjustments to the apparatus should not be made while it is pressurized; rather, the system should be depressurized before mechanical adjustments are made.
Immediately after an experiment in which low-pressure equipment connected to a source of high pressure is pressurized, the low-pressure equipment should either be disconnected entirely or left independently vented to the atmosphere. Either action will prevent the accidental buildup of excessive pressure in the low-pressure equipment due to leakage from the high-pressure side.
Vessels or equipment made partly or entirely of silver, copper, or alloys containing more than 50% copper should not be used in contact with acetylene or ammonia. Those made of metals susceptible to amalgamation (e.g., copper, brass, zinc, tin, silver, lead, and gold) should not come into contact with mercury. This includes equipment that has soldered and brazed joints.
Prominent warning signs should be placed in any area where a pressure reaction is in progress so that people entering the area will be aware of the potential risk.
6.D.2.2.1
Pressure-Relief Devices
All pressure or vacuum systems and all vessels that may be subjected to pressure or vacuum should be protected by properly installed and tested pressure-relief devices. Experiments involving highly reactive materials that might explode may also require the use of special pressure-relief devices and may need to be operated at a fraction of the permissible working pressure of the system.
Examples of pressure-relief devices include the rupture-disk type used with closed-system vessels and the spring-loaded safety valves used with vessels for transferring liquefied gases. The following precautions are advisable in the use of pressure-relief devices:
-
The maximum setting of a pressure-relief device is the rated working pressure established for the vessel or for the weakest member of the pressure system at the operating temperature. The operating pressure should be less than the allowable working pressure of the system. In the case of a system protected by a spring-loaded relief device, the maximum operating pressure should be from 5 to 25% lower than the rated working pressure, depending on the type of safety valve and the importance of leak-free operation. In the case of a system protected by a rupture-disk device, the maximum operating pressure should be about two-thirds of the rated working pressure; the exact figure is governed by the fatigue life of the disk used, the temperature, and load pulsations.
-
Pressure-relief devices that may discharge toxic, corrosive, flammable, or otherwise hazardous or noxious materials should be vented in a safe and environmentally acceptable manner such as scrubbing and/ or diluting with nonflammable streams.
-
Shutoff valves must not be installed between pressure-relief devices and the equipment they are to protect.
-
Only qualified persons should perform maintenance work on pressure-relief devices.
-
Pressure-relief devices should be inspected and replaced periodically.
6.D.2.2.2
Pressure Gauges
The proper choice and use of a pressure gauge involve several factors, including the flammability, compressibility, corrosivity, toxicity, temperature, and pressure range of the fluid with which it is to be used. Generally, a gauge with a range that is double the working pressure of the system should be selected.
A pressure gauge is normally a weak point in any pressure system because its measuring element must operate in the elastic zone of the metal involved. The resulting limited factor of safety makes careful gauge selection and use mandatory and often dictates the use of accessory protective equipment. The primary element of the most commonly used gauges is a Bourdon tube, which is usually made of brass or bronze and has soft-soldered connections. More expensive gauges can be obtained that have Bourdon tubes made of steel, stainless steel, or other special metals and welded or silver-soldered connections. Accuracies vary from ±2% for less-expensive pressure gauges to ±0.1% for higher-quality gauges. A diaphragm gauge should be used with corrosive gases or liquids or with viscous fluids that would destroy a steel or bronze Bourdon tube.
Consideration should be given to alternative methods of pressure measurement that may provide greater safety than the direct use of pressure gauges. Such methods include the use of seals or other isolating devices in pressure tap lines, indirect observation devices, and remote measurement by strain-gauge transducers with digital readouts.
6.D.2.2.3
Glass Equipment
The use of glassware for work at high pressure should be avoided whenever possible. Glass is a brittle material subject to unexpected failures due to factors such as mechanical impact and assembly and tightening stresses. Poor annealing after glassblowing can leave severe strains. Glass equipment, such as rotameters and liquid-level gauges, incorporated in metallic pressure systems should be installed with shutoff valves at both ends to control the discharge of liquid or gaseous materials in the event of breakage. Mass flowmeters are available that can replace rotameters in desired applications.
6.D.2.2.4
Plastic Equipment
Except as noted below, the use of plastic equipment for pressure or vacuum work should be avoided unless no suitable substitute is available. These materials can fail under pressure or thermal stress.
Tygon and similar plastic tubing have quite limited applications in pressure work. These materials can be used for hydrocarbons and most aqueous solutions at room temperature and moderate pressure. Reinforced plastic tubing that can withstand higher pressures is also available. However, loose tubing under pressure can cause physical damage by its own whipping action. Details of permissible operating conditions must be obtained from the manufacturer. Because of their very large coefficients of thermal expansion, some polymers have a tendency to expand a great deal on heating and to contract on cooling. This behavior can create a hazard in equipment subjected to very low temperatures or to alternating low and high temperatures.
6.D.2.2.5
Piping, Tubing, and Fittings
The proper selection and assembly of components in a pressure system are critical safety factors. Considerations should include the materials used in manufacturing the components, compatibility with the materials to be under pressure, the tools used for assembly, and the reliability of the finished connections. No oil or lubricant of any kind should be used in a tubing system with oxygen because the combination produces an explosion hazard.
All-brass and stainless steel fittings should be used with copper or brass and steel or stainless steel tubings, respectively. It is important that fittings of this type be installed correctly. Different brands of tube fittings should not be mixed in the same apparatus assembly because construction parts are often not interchangeable.
6.D.2.2.6
Teflon Tape Applications
Teflon tape should be used on tapered pipe thread where the seal is formed in the thread area. Tapered pipe thread is commonly found in applications where fittings are not routinely taken apart (e.g., general building piping applications).
Teflon tape should not be used on straight thread where the seal is formed through gaskets or by other metal-to-metal contacts that are forced together when the fitting is tightened (e.g., CGA gas cylinder fittings or compression fittings). Metal-to-metal seals are machined to tolerances that seal without the need of Teflon tape or other gasketing materials. If used where not needed, as on CGA fittings, Teflon tape only spreads and weakens the threaded connections and can plug up lines that it enters accidentally.
6.E
WORKING WITH HIGH/LOW PRESSURES AND TEMPERATURES
Work with hazardous chemicals at high/low pressures and/or high/low temperatures requires planning and special precautions. For many experiments, extremes of both pressure and temperature, such as reactions at elevated temperatures and pressures and work with cryogenic liquids and high vacuum, must be managed simultaneously. Procedures at high/low pressures should be carried out with protection against explosion or implosion by appropriate equipment selection and the use of safety shields. Appropriate temperature control and interlocks should be provided so that heating or cooling baths cannot exceed the desired limits even if the equipment fails. Care must be taken to select and use glass apparatus that can safely withstand thermal expansion or contraction at the designated pressure and temperature extremes.
6.E.1 Pressure Vessels
High-pressure operations should be performed only in special chambers equipped for this purpose. Laboratory workers should ensure that equipment for operations using pressure vessels is appropriately selected, properly labeled and installed, and protected by pressure-relief and necessary control devices. Vessels must be strong enough to withstand the stresses encountered at the intended operating pressures and temperatures. The vessel material must not corrode when it is in contact with the material(s) it contains. The material should not react with the process being studied, and
the vessel must be of the proper size and configuration needed for the process. Reactions should never be carried out in, nor heat applied to, an apparatus that is a closed system unless it has been designed and tested to withstand pressure.
Pressure-containing systems designed for use at elevated temperatures should have a positive temperature controller. Manual control using a simple variable autotransformer, such as a Variac, is not good practice. The use of both a back-up temperature controller capable of recording temperatures and shutting down an unattended system is strongly recommended.
(See section 6.D.2 above.)
6.E.1.1 Records, Inspection, and Testing
In some localities, adherence to national codes such as the ASME (American Society of Mechanical Engineers) Boiler and Pressure Vessel Code (ASME, 1992) is mandatory. Selection of containers, tubing, fittings, and other process equipment, along with the operational techniques and procedures, must adhere to the constraints necessary for high-pressure service. The proper selection and assembly of components in a pressure system are critical safety factors. Compatibility of materials, tools used for assembly, and the reliability of connections are all key considerations.
Each pressure vessel in a laboratory should have a stamped number or fixed label plate that uniquely identifies it. Information such as the maximum allowable working pressure, allowable temperature at this pressure, material of construction, and burst diagram should be readily available. Information on the vessel's history should include temperature extremes it has experienced, any modifications and repairs made to the original vessel, and all inspections or test actions it has undergone. Similarly, the relieving pressure and setting data should be stamped on a metal tag attached to installed pressure-relief devices, and the setting mechanisms should be sealed. Relief devices used on pressure regulators do not require these seals or numbers.
All pressure equipment should be tested or inspected periodically. The interval between tests or inspections is determined by the severity of the usage the equipment has received. Corrosive or otherwise hazardous service requires more frequent tests and inspections. Inspection data should be stamped on or attached to the equipment. Pressure vessels may be subjected to nondestructive inspections such as visual inspection, penetrant inspection, acoustic emissions recording, and radiography. However, hydrostatic proof tests are necessary for final acceptance. These tests should be as infrequent as possible. They should be performed before the vessel is placed in initial service, every 10 years thereafter, after a significant repair or modification, and if the vessel experiences overpressure or overtemperature.
Testing the entire apparatus with soap solution and air or nitrogen pressure to the maximum allowable working pressure of the weakest section of the assembled apparatus can usually detect leaks at threaded joints, packings, and valves.
Final assemblies should be pressure-tested and leak-tested to ensure their integrity. Laboratory workers are strongly advised to consult an expert on high-pressure work as they design, build, and operate a high-pressure process. Finally, extreme care should be exercised when disassembling pressure equipment for repair, modification, or decommissioning. Protective equipment should be worn just in case a line or vessel that is opened contains material under pressure.
6.E.1.2 Pressure Reactions in Glass Equipment
For any reaction run on a large scale (more than 10 g total weight of reactants) or at a maximum pressure in excess of 690 kPa (100 psi), only procedures involving a suitable high-pressure autoclave or shaker vessel should be used. Whenever possible, metal reactors with glass liners should be used instead of sealed glass tubes. Fisher-Porter-type tubes with a pressure gauge and release device are preferred for pressure reactions in glass equipment. However, it is sometimes convenient to run very small-scale reactions at low pressures in a small sealed glass tube or in a thick-walled pressure bottle of the type used for catalytic hydrogenation. For any such reaction, the worker should be fully prepared for the significant possibility that the sealed vessel will burst. Removal of any gas should be prepared for by appropriate ventilation. Every precaution should be taken to prevent injury from flying glass or from corrosive or toxic reactants by using suitable shielding. Centrifuge bottles should be sealed with rubber stoppers clamped in place, wrapped with friction tape and shielded with a metal screen or wrapped with friction tape and surrounded by multiple layers of loose cloth toweling, and clamped behind a good safety shield. Some bottles are typically equipped with a head containing inlet and exhaust gas valves, a pressure gauge, and a pressure-relief valve. When corrosive materials are being used, a Teflon pressure-relief valve should be used. The preferred source of heat for such vessels is steam, because an explosion in the vicinity of an electrical heater could start a fire and an explosion in a liquid heating bath would scatter hot liquid around
the area. Any reaction of this type should be carried out in a hood and labeled with signs that indicate the contents of the reaction vessel and the explosion risk.
Glass tubes with high-pressure sealers should be no more than three-quarters full. Appropriate precautions using the proper shielding must be taken for condensing materials and sealing tubes. Vacuum work can be carried out on a Schlenck line as long as proper technique is used. The sealed glass tubes can be placed either inside pieces of brass or iron pipe capped at one end with a pipe cap or in an autoclave containing some of the reaction solvent (to equalize the pressure inside and outside the glass tube). The tubes can be heated with steam or in a specially constructed, electrically heated ''sealed-tube" furnace that is controlled thermostatically and located such that the force of an explosion would be directed into a safe area. When the required heating has been completed, the sealed tube or bottle should be allowed to cool to room temperature. Sealed bottles and tubes of flammable materials should be wrapped with cloth toweling, placed behind a safety shield, and then cooled slowly, first in an ice bath and then in dry ice. After cooling, the clamps and rubber stoppers can be removed from the bottles prior to opening. Personal protective equipment and apparel, including shields, masks, coats, and gloves, should be used during tube-opening operations. It should be noted that NMR tubes are often thin-walled and should only be used for pressure reactions in a special high-pressure probe or in capillary devices.
Newly fabricated or repaired glass equipment for pressure or vacuum work should be examined for flaws and strains under polarized light. Corks, rubber stoppers, and rubber or plastic tubing should never be relied on as relief devices for protection of glassware against excess pressure; a liquid seal, Bunsen tube, or equivalent positive relief device should be used. When glass pipe is used, only proper metal fittings should be used.
6.E.2 Liquefied Gases and Cryogenic Liquids
Cryogenic liquids are materials with boiling points of less than -73 °C (-100 °F). Liquid nitrogen, helium, and argon, and slush mixtures of dry ice with isopropanol are the materials most commonly used in cold traps to condense volatile vapors from a system. In addition, oxygen, hydrogen, and helium are often used in the liquid state.
The primary hazards of cryogenic liquids are fire or explosion, pressure buildup (either slowly or due to rapid conversion of the liquid to the gaseous state), embrittlement of structural materials, frostbite, and asphyxiation. The extreme cold of cryogenic liquids requires special care in their use. The vapor that boils off from a liquid can cause the same problems as the liquid itself.
The fire or explosion hazard is obvious when gases such as oxygen, hydrogen, methane, and acetylene are used. Air enriched with oxygen can greatly increase the flammability of ordinary combustible materials and may even cause some noncombustible materials to burn readily (see Chapter 5, sections 5.G.4 and 5.G.5). Oxygen-saturated wood and asphalt have been known to literally explode when subjected to shock. Because oxygen has a higher boiling point (-183 °C) than nitrogen (-195 °C), helium (-269 °C), or hydrogen (-252.7 °C), it can be condensed out of the atmosphere during the use of these lower-boiling-point cryogenic liquids. With the use of liquid hydrogen particularly, conditions may develop for an explosion. (See Chapter 5, sections 5.F.3 and 5.G.2, for further discussion.)
It is advisable to furnish all cylinders and equipment containing flammable or toxic liquefied gases (not vendor-owned) with a spring-loaded pressure-relief device (not a rupture disk) because of the magnitude of the potential risk that can result from activation of a non-resetting relief device. Commercial cylinders of liquefied gases are normally supplied only with a fusible-plug type of relief device, as permitted by DOT regulations. Pressurized containers that contain cryogenic material should be protected with multiple pressure-relief devices.
Cryogenic liquids must be stored, shipped, and handled in containers that are designed for the pressures and temperatures to which they may be subjected. Materials that are pliable under normal conditions can become brittle at low temperatures. Dewar flasks, which are used for relatively small amounts of material, should have a dust cap over the outlet to prevent atmospheric moisture from condensing and plugging the neck of the tube. Special cylinders insulated and vacuum-jacketed with pressure-relief valves and rupture devices to protect the cylinder from pressure buildup are available in capacities of 100 to 200 liters (L).
A special risk to personnel is skin or eye contact with the cryogenic liquid. Because these liquids are prone to splash in use owing to the large volume expansion ratio when the liquid warms up, eye protection, preferably a face shield, should be worn when handling liquefied gases and other cryogenic fluids. The transfer of liquefied gases from one container to another should not be attempted for the first time without the direct supervision and instruction of someone experienced in this operation. Transfers should be done very slowly to minimize boiling and splashing.
Unprotected parts of the body should not be in contact with uninsulated vessels or pipes that contain cryogenic liquids because extremely cold material may bond firmly to the skin and tear flesh if separation or withdrawal is attempted. Even very brief skin contact with a cryogenic liquid can cause tissue damage similar to that of frostbite or thermal burns, and prolonged contact may result in blood clots that have potentially very serious consequences. Gloves must be impervious to the fluid being handled and loose enough to be tossed off easily. A potholder may be a desirable alternative. Objects that are in contact with cryogenic liquids should also be handled with tongs or potholders. The work area should be well ventilated. Virtually all liquid gases present the threat of poisoning, explosion, or, at a minimum, asphyxiation in a confined space. Major harmful consequences of the use of cryogenic inert gases, including asphyxiation, are due to boiling off of the liquid and pressure buildup, which can lead to violent rupture of the container or piping.
In general, liquid hydrogen should not be transferred in an air atmosphere because oxygen from the air can condense in the liquid hydrogen, presenting a possible explosion risk. All precautions should be taken to keep liquid oxygen from organic materials; spills on oxidizable surfaces can be hazardous. Though nitrogen is inert, its liquefied form can be hazardous because of its cryogenic properties and because displacement of air oxygen in the vicinity can lead to asphyxiation followed by death with little warning. Rooms that contain appreciable quantities of liquid nitrogen (N2) should be fitted with oxygen meters and alarms. Liquid nitrogen should not be stored in a closed room because the oxygen content of the room can drop to unsafe levels.
Cylinders and other pressure vessels used for the storage and handling of liquefied gases should not be filled to more than 80% of capacity, to protect against possible thermal expansion of the contents and bursting of the vessel by hydrostatic pressure. If the possibility exists that the temperature of the cylinder may increase to above 30°C, a lower percentage (e.g., 60%) of capacity should be the limit.
6.E.2.1 Cold Traps and Cold Baths
Cold traps should be chosen that are large enough and cold enough to collect the condensable vapors in a vacuum system. Cold traps should be checked frequently to make sure they do not become plugged with frozen material. Cold traps in a reduced-pressure system should be taped or placed in a metal can filled with vermiculite. After completion of an operation in which a cold trap has been used, the system should be vented in a safe and environmentally acceptable way. Otherwise, pressure could build up, creating a possible explosion and sucking pump oil into the system. Cold traps under continuous use, such as those used to protect inert atmosphere dry boxes, should be cooled electrically and monitored by low-temperature probes.
Appropriate gloves and a face shield should be used to avoid contact with the skin when using cold baths. Dry gloves should be used when handling dry ice. Lowering of the head into a dry ice chest is to be avoided because carbon dioxide is heavier than air and asphyxiation can result. The preferred liquids for dry ice cooling baths are isopropyl alcohol or glycols, and the dry ice should be added slowly to the liquid portion of the cooling bath to avoid foaming. The common practice of using acetone-dry ice as a coolant should be avoided. Dry ice and liquefied gases used in refrigerant baths should always be open to the atmosphere. They should never be used in closed systems, where they may develop uncontrolled and dangerously high pressures.
Extreme caution should be exercised in using liquid nitrogen as a coolant for a cold trap. If such a system is opened while the cooling bath is still in contact with the trap, oxygen may condens from the atmosphere. The oxygen could then combine with any organic material in the trap to create a highly explosive mixture. Thus, a system that is connected to a liquid nitrogen trap should not be opened to the atmosphere until the trap has been removed. Also, if the system is closed after even a brief exposure to the atmosphere, some oxygen (or argon) may have already condensed. Then, when the liquid nitrogen bath is removed or when it evaporates, the condensed gases will vaporize, producing a pressure buildup and the potential for explosion. The same explosion hazard can be created if liquid nitrogen is used to cool a flammable mixture that is exposed to air.
6.E.2.2 Selection of Low-Temperature Equipment
Equipment used at low temperatures should be selected carefully. Temperature can dramatically change characteristics of materials. For example, even the impact strength of ordinary carbon steel is greatly reduced at low temperatures, and failure can occur at points of weakness, such as notches or abrupt changes in the material of construction, in cold equipment. When combinations of materials are required, it is important that the temperature dependence of their volumes be considered so that leaks, ruptures, and glass fractures can be avoided. For example, O-rings that provide a good seal at room temperature may lose resilience and fail to function on chilled equipment.
IMPROPER GLASSWARE IN A CRYOGENIC FLUID A thin-walled Pyrex NMR sample tube containing absorbed hydrocarbons on platinum on an alumina support, which had been sealed under vacuum and annealed, was placed in a dry ice and chloroform mixture in a Dewar flask in a hood with horizontal sliding sashes. The tube exploded after approximately one minute in the bath, apparently due to thermal shock. Although the Dewar was not damaged, the researcher suffered severely irritated eyes and had to be transported to the trauma center. The researcher had been wearing glasses and a laboratory coat as personal protection, and the hood sash had been slid to the side. Face shields, goggles, gloves, and acrylic shielding were available in the laboratory but had not been used. |
The 18% chromium/8% nickel stainless steels retain their impact resistance down to approximately -240 °C, the exact value depending heavily on special design considerations. The impact resistance of aluminum, copper, nickel, and many other nonferrous metals and alloys increases with decreasing temperatures. Special alloy steels should be used for liquids or gases containing hydrogen at temperatures greater than 200 °C or at pressures greater than 34.5 MPa (500 psi) because of the danger of weakening carbon steel equipment by hydrogen embrittlement.
6.E.2.3 Cryogenic Lines and Supercritical Fluids
Liquid cryogen transfer lines should be designed so that liquid cannot be trapped in any nonvented part of the system. Experiments in supercritical fluids include high pressure and should be carried out with appropriate protective systems.
6.E.3 Vacuum Work and Apparatus
Vacuum work can result in an implosion and the possible hazards of flying glass, spattering chemicals, and fire. All vacuum operations must be set up and operated with careful consideration of the potential risks.
Although a vacuum distillation apparatus may appear to provide some of its own protection in the form of heating mantles and column insulation, this is not sufficient because an implosion could scatter hot, flammable liquid. An explosion shield and a face mask should be used to protect the worker, and the procedure should be carried out in a hood.
Equipment at reduced pressure is especially prone to rapid pressure changes, which can create large pressure differences within the apparatus. Such conditions can push liquids into unwanted locations, sometimes with undesirable consequences.
Water, solvents, and corrosive gases should not be allowed to be drawn into a building vacuum system. When the potential for such a problem exists, a water aspirator with a solvent collection device and a trap with a check valve installed between the water aspirator and the apparatus, to prevent water from being drawn back into the apparatus, should be used as the vacuum source.
Mechanical vacuum pumps should be protected by cold traps, and their exhausts should be vented to an exhaust hood or to the outside of the building. If solvents or corrosive substances are inadvertently drawn into the pump, the oil should be changed before any further use. (Oil contaminated with solvents, mercury, corrosive substances, and so on, must be handled as hazardous waste.) It may be desirable to maintain a log of pump usage as a guide to length of use and potential contaminants in the pump oil. The belts and pulleys on vacuum pumps should be covered with guards.
(See section 6.C.2 for a discussion of vacuum pumps.)
6.E.3.1 Glass Vessels
Although glass vessels are frequently used in low-vacuum operations, evacuated glass vessels may collapse violently, either spontaneously from strain or from an accidental blow. Therefore, pressure and vacuum operations in glass vessels should be conducted behind adequate shielding. It is advisable to check for flaws such as star cracks, scratches, and etching marks each time a vacuum apparatus is used. Only round-bottomed or thick-walled (e.g., Pyrex) evacuated reaction vessels specifically designed for operations at reduced pressure should be used. Repaired glassware is subject to thermal shock and should be avoided. Thin-walled, Erlenmeyer, or round-bottomed flasks larger than 1 L should never be evacuated.
6.E.3.2 Dewar Flasks
Dewar flasks are under high vacuum and can collapse as a result of thermal shock or a very slight mechanical shock. They should be shielded, either by a layer of fiber-reinforced friction tape or by enclosure in a wooden or metal container, to reduce the risk of flying glass in case of collapse. Metal Dewar flasks
IMPLODING DEWAR A researcher was about to prepare an ice trap in a Dewar to cool a stationary stainless steel receiver on a chemical reactor system. The researcher had positioned the Dewar on a laboratory jack stand and had raised the Dewar into position. The Dewar imploded, propelling glass shards toward the researcher, who fortunately was wearing prescription safety glasses and received only minor facial cuts. The researcher should have been wearing a full-length face shield and should have had a cover on the Dewar. |
should be used whenever there is a possibility of breakage.
Styrofoam buckets with lids can be a safer form of short-term storage and conveyance of cryogenic liquids than glass vacuum Dewars. Although they do not insulate as well as Dewar flasks, they eliminate the danger of implosion.
6.E.3.3 Desiccators
If a glass vacuum desiccator is used, it should be made of Pyrex or similar glass, completely enclosed in a shield or wrapped with friction tape in a grid pattern that leaves the contents visible and at the same time guards against flying glass should the vessel implode. Plastic (e.g., polycarbonate) desiccators reduce the risk of implosion and may be preferable, but should also be shielded while evacuated. Solid desiccants are preferred. An evacuated desiccator should never be carried or moved. Care should be taken in opening the valve to avoid a shock wave into the desiccator.
6.E.3.4 Rotary Evaporators
Glass components of the rotary evaporator should be made of Pyrex or similar glass, completely enclosed in a shield to guard against flying glass should the components implode. Increase in rotation speed and application of vacuum to the flask whose solvent is to be evaporated should be gradual.
6.E.3.5 Assembly of Vacuum Apparatus
Vacuum apparatus should be assembled so as to avoid strain. Joints must be assembled so as to allow various sections of the apparatus to be moved if necessary without transmitting strain to the necks of the flasks. Heavy apparatus should be supported from below as well as by the neck. The assembler should avoid putting pressure on a vacuum line. Failure to keep the pressure below 1 atmosphere could lead to the stopcocks popping out at high velocity or to an explosion of the glass apparatus. Such increased pressure could result from warming of the contents of the trap due to failure to maintain low temperatures.
Vacuum apparatus should be placed well back onto the bench or into the hood where they will not be inadvertently hit. If the back of the vacuum setup faces the open laboratory, it should be protected with panels of suitably heavy transparent plastic to prevent injury to nearby workers from flying glass in case of explosion.
6.F USING PERSONAL PROTECTIVE, SAFETY, AND EMERGENCY EQUIPMENT
As outlined in previous chapters, it is essential for each laboratory worker to be proactive to ensure the laboratory is a safe working environment. This attitude begins with wearing appropriate apparel and using proper eye, face, hand, and foot protection when working with hazardous chemicals. It is the responsibility of the institution to provide appropriate safety and emergency equipment for laboratory workers and for emergency personnel. (See also section 5.C.)
6.F.1 Personal Protective Equipment and Apparel
6.F.1.1 Personal Clothing
Clothing that leaves large areas of skin exposed is inappropriate in laboratories where hazardous chemicals are in use. The worker's personal clothing should be fully covering. Appropriate laboratory coats should be worn, buttoned, with the sleeves rolled down. Laboratory coats should be fire-resistant. Those fabricated of polyester are not appropriate for glassblowing or work with flammable materials. Cotton coats are inexpensive and do not burn readily. Laboratory coats or laboratory aprons made of special materials are available for high-risk activities. Laboratory coats that have been used in the laboratory should be left there to minimize the possibility of spreading chemicals to public assembly, eating, or office areas, and they should be cleaned regularly. (For more information, see the OSHA Personal Protective Equipment Standard (29 CFR 1910.132) and the OSHA Laboratory Standard (29 CFR 1910.1450).)
Unrestrained long hair and loose clothing such as neckties, baggy pants, and coats are inappropriate in a laboratory where hazardous chemicals are in use. Such items can catch fire, be dipped in chemicals, and
get caught in equipment. Similarly, rings, bracelets, watches, or other jewelry that could be damaged, trap chemicals close to the skin, come in contact with electrical sources, or get caught in machinery should not be worn. Leather clothing or accessories should not be worn in situations where chemicals could be absorbed in the leather and held close to the skin.
Protective apparel should always be worn if there is a possibility that personal clothing could become contaminated with chemically hazardous material. Washable or disposable clothing worn for laboratory work with especially hazardous chemicals includes special laboratory coats and aprons, jumpsuits, special boots, shoe covers, and gauntlets, as well as splash suits. Protection from heat, moisture, cold, and/or radiation may be required in special situations. Among the factors to be considered in choosing protective apparel, in addition to the specific application, are resistance to physical hazards, flexibility and ease of movement, chemical and thermal resistance, and ease of cleaning or disposal. Although cotton is a good material for laboratory coats, it reacts rapidly with acids. Plastic or rubber aprons can provide good protection from corrosive liquids but can be inappropriate in the event of a fire. Plastic aprons can also accumulate static electricity, and so they should not be used around flammable solvents, explosives sensitive to electrostatic discharge, or materials that can be ignited by static discharge. Disposable garments provide only limited protection from vapor or gas penetration. Disposable garments that have been used when handling carcinogenic or other highly hazardous material should be removed without exposing any individual to toxic materials and disposed of as hazardous waste.
(See Chapter 5, sections 5.C.2.5 and 5.C.2.6.)
6.F.1.2 Foot Protection
Street shoes may not be appropriate in the laboratory, where both chemical and mechanical hazards may exist. Substantial shoes should be worn in areas where hazardous chemicals are in use or mechanical work is being done. Clogs, perforated shoes, sandals, and cloth shoes do not provide protection against spilled chemicals. In many cases, safety shoes are advisable. Shoe covers may be required for work with especially hazardous materials. Shoes with conductive soles are useful to prevent buildup of static charge, and insulated soles can protect against electrical shock.
6.F.1.3 Eye and Face Protection
Safety glasses with side shields that conform to ANSI standard Z87.1-1989 should be required for work with hazardous chemicals. Ordinary prescription glasses with hardened lenses do not serve as safety glasses. Contact lenses can sometimes be worn safely if appropriate eye and face protection is also worn (see, however, section 5.C.2.1). Although safety glasses can provide satisfactory protection from injury from flying particles, they do not fit tightly against the face and offer little protection against splashes or sprays of chemicals. It is appropriate for a laboratory to provide impact goggles that include splash protection (splash goggles), full-face shields that also protect the throat, and specialized eye protection (i.e., protection against ultraviolet light or laser light). Splash goggles, which have splash-proof sides to fully protect the eyes, should be worn if there is a splash hazard in any operation involving hazardous chemicals. Impact protection goggles should be worn if there is a danger of flying particles, and full-face shields with safety glasses and side shields are needed for complete face and throat protection. When there is a possibility of liquid splashes, both a face shield and splash goggles should be worn; this is especially important for work with highly corrosive liquids. Full-face shields with throat protection and safety glasses with side shields should be used when handling explosive or highly hazardous chemicals. If work in the laboratory could involve exposure to lasers, ultraviolet light, infrared light, or intense visible light, specialized eye protection should be worn. It also is appropriate for a laboratory to provide visitor safety glasses and a sign indicating that eye protection is required in laboratories where hazardous chemicals are in use.
6.F.1.4 Hand Protection
Gloves appropriate to the hazard should be used at all times. It is important that the hands and any skin that is likely to be exposed to hazardous chemicals receive special attention. Proper protective gloves should be worn when handling hazardous chemicals, toxic materials, materials of unknown toxicity, corrosive materials, rough or sharp-edged objects, and very hot or very cold objects. Before the gloves are used, it is important that they be inspected for discoloration, punctures, or tears. A defective or improper glove can itself be a serious hazard in handling hazardous chemicals. If chemicals do penetrate glove material, they could then be held in prolonged contact with the hand and cause more serious damage than in the absence of a proper glove.
The degradation and permeation characteristics of the glove material selected must be appropriate for protection from the hazardous chemicals being handled. Glove selection guides (available from most man-
ufacturers) should be consulted, with careful consideration given to the permeability of any material, particularly when working with organic solvents, which may be able to permeate or dissolve the glove materials. The thin latex "surgical" vinyl and nitryl gloves that are popular in many laboratories because of their composition and thin construction may not be appropriate for use with highly toxic chemicals or solvents. For example, because latex is readily permeated by carbon disulfide, a hand covered by a latex glove immersed in carbon disulfide would receive constant wetting by this toxic chemical, which would by then be absorbed through the skin. Gloves should be replaced immediately if they are contaminated or torn. The use of double gloves may be appropriate in situations involving chemicals of high or multiple hazards. Leather gloves are appropriate for handling broken glassware and inserting tubing into stoppers, where protection from chemicals is not needed. Insulated gloves should be used when working with very hot or very cold materials. With cryogenic fluids the gloves must be impervious to fluid, but loose enough to be tossed off easily. Absorbent gloves could freeze on the hand and intensify any exposure to liquefied gases. Turning up the cuffs on gloves can prevent liquids from running down the arms when hands are raised.
Gloves should be decontaminated or washed appropriately before they are taken off and should be left in the work area and not be allowed to touch any uncontaminated objects in the laboratory or any other area. Gloves should be replaced periodically, depending on the frequency of use. Regular inspection of their serviceability is important. If they cannot be cleaned, contaminated gloves should be disposed of according to institutional procedures.
Barrier creams and lotions can provide some skin protection but should never be a substitute for gloves, protective clothing, or other protective equipment. These creams should be used only to supplement the protection offered by personal equipment.
6.F.2 Safety and Emergency Equipment
Safety equipment, including spill control kits, safety shields, fire safety equipment, respirators, safety showers and eyewash fountains, and emergency equipment should be available in well-marked, highly visible locations in all chemical laboratories. Fire alarm pull stations and telephones with emergency telephone numbers clearly indicated must be readily accessible. In addition to the standard items, there may also be a need for other safety devices. It is the responsibility of the laboratory supervisor to ensure proper training and provide supplementary equipment as needed.
6.F.2.1 Spill Control Kits and Cleanup
In most cases, researchers are responsible for cleaning up their own spills. If a spill exceeds their ability or challenges their safety, they should leave the spill site and call the emergency telephone number for help. Emergency response spill cleanup personnel should be given all available information about the spill.
A spill control kit should be on hand. A typical cleanup kit may be a container on wheels that can be moved to the location of the spill and may include such items as instructions; absorbent pads; a spill absorbent mixture for liquid spills; a polyethylene scoop for dispensing spill absorbent; mixing it with the spill, and picking up the mixture; thick polyethylene bags for deposit of the mixture; and tags and ties for labeling the bags. Any kit should be used in conjunction with the personal protective equipment needed for the chemical that is to be cleaned up. Before beginning an operation that could produce a spill, the worker should locate the specialized spill control kits for that operation.
(Also see Chapter 5, section 5.C.11.5.)
6.F.2.2 Safety Shields
Safety shields should be used for protection against possible explosions or splash hazards. Laboratory equipment should be shielded on all sides so that there is no line-of-sight exposure of personnel. The front sashes of conventional laboratory exhaust hoods can provide shielding. However, a portable shield should also be used when manipulations are performed, particularly with hoods that have vertical-rising doors rather than horizontal-sliding sashes.
Portable shields can be used to protect against hazards of limited severity, such as small splashes, heat, and fires. A portable shield, however, provides no protection at the sides or back of the equipment, and many such shields not sufficiently weighted for forward protection may topple toward the worker when there is a blast. A fixed shield that completely surrounds the experimental apparatus can afford protection against minor blast damage.
Polymethyl methacrylate, polycarbonate, polyvinyl chloride, and laminated safety plate glass are all satisfactory transparent shielding materials. Where combustion is possible, the shielding material should be nonflammable or slow burning; if it can withstand the working blast pressure, laminated safety plate glass may be the best material for such circumstances. When cost, transparency, high tensile strength, resistance to bending loads, impact strength, shatter resistance, and burning rate are considered, polymethyl methacrylate offers an excellent overall combination of shielding characteristics.
Polycarbonate is much stronger and self-extinguishing after ignition but is readily attacked by organic solvents.
6.F.2.3 Fire Safety Equipment
6.F.2.3.1
Fire Extinguishers
All chemical laboratories should have carbon dioxide and dry chemical fire extinguishers. Other types of extinguishers should be available if required for the work being done. The four types of extinguishers most commonly used are classified by the type of fire for which they are suitable, as listed below. It should be noted that multipurpose class A, B, and C extinguishers are available.
-
Water extinguishers are effective against burning paper and trash (class A fires). These should not be used for extinguishing electrical, liquid, or metal fires.
-
Carbon dioxide extinguishers are effective against burning liquids, such as hydrocarbons or paint, and electrical fires (class B and C fires). They are recommended for fires involving computer equipment, delicate instruments, and optical systems because they do not damage such equipment. They are less effective against paper and trash fires and must not be used against metal hydride or metal fires. Care must be taken in using these extinguishers, because the force of the compressed gas can spread burning combustibles such as papers and can tip over containers of flammable liquids.
-
Dry powder extinguishers, which contain ammonium phosphate or sodium bicarbonate, are effective against burning liquids and electrical fires (class B and C fires). They are less effective against paper and trash or metal fires. They are not recommended for fires involving delicate instruments or optical systems because of the cleanup problem. Computer equipment may need to be replaced if exposed to sufficient amounts of the dry powders. These extinguishers are generally used where large quantities of solvent may be present.
-
Met-L-X® extinguishers and others that have special granular formulations are effective against burning metal (class D fires). Included in this category are fires involving magnesium, lithium, sodium, and potassium; alloys of reactive metals; and metal hydrides, metal alkyls, and other organometallics. These extinguishers are less effective against paper and trash, liquid, or electrical fires.
Every extinguisher should carry a label indicating what class or classes of fires it is effective against and the date last inspected. There are a number of other, more specialized types of extinguishers available for unusual fire hazard situations. Each laboratory worker should be responsible for knowing the location, operation, and limitations of the fire extinguishers in the work area. It is the responsibility of the laboratory supervisor to ensure that all workers are shown the locations of fire extinguishers and are trained in their use. After use, an extinguisher should be recharged or replaced by designated personnel.
6.F.2.3.2
Heat and Smoke Detectors
Heat sensors and/or smoke detectors may be part of the building safety equipment. If designed into the fire alarm system, they may automatically sound an alarm and call the fire department, they may trigger an automatic extinguishing system, or they may only serve as a local alarm. Because laboratory operations may generate heat or vapors, the type and location of the detectors must be carefully evaluated in order to avoid frequent false alarms.
6.F.2.3.3
Fire Hoses
Fire hoses are intended for use by trained firefighters against fires too large to be handled by extinguishers and are included as safety equipment in some structures. Water has a cooling action and is effective against fires involving paper, wood, rags, trash, and such (class A fires). Water should not be used directly on fires that involve live electrical equipment (class C fires) or chemicals such as alkali metals, metal hydrides, and metal alkyls that react vigorously with it (class D fires).
Streams of water should not be used against fires that involve oils or other water-insoluble flammable liquids (class B fires). Water will not readily extinguish such fires. Rather, it can cause the fire to spread or float to adjacent areas. These possibilities are minimized by the use of a water fog. Water fogs are used extensively by the petroleum industry because of their fire-controlling and extinguishing properties. A fog can be used safely and effectively against fires that involve oil products, as well as those involving wood, rags, rubbish, and such.
Because of the potential risks involved in using water around chemicals, laboratory workers should refrain from using fire hoses except in extreme emergencies. Otherwise, such use should be reserved for trained firefighters. Clothing fires can be extinguished by immediately dropping to the floor and rolling; how-
ever, if a safety shower is immediately available, it should be used (as noted in section 6.F.2.5).
6.F.2.3.4
Automatic Fire-Extinguishing Systems
In areas where fire potential and the risk of injury or damage are high, automatic fire-extinguishing systems are often used. These may be of the water sprinkler, foam, carbon dioxide, halon, or dry chemical type. If an automatic fire-extinguishing system is in place, laboratory workers should be informed of its presence and advised of any safety precautions required in connection with its use (e.g., evacuation before a carbon dioxide total-flood system is activated, to avoid asphyxiation).
6.F.2.4 Respiratory Protective Equipment
The primary method for the protection of laboratory personnel from airborne contaminants should be to minimize the amount of such materials entering the laboratory air. When effective engineering controls are not possible, suitable respiratory protection should be used after proper training. Respiratory protection may be needed in carrying out an experimental procedure, in dispensing or handling hazardous chemicals, in responding to a chemical spill or release in cleanup decontamination, or in hazardous waste handling.
Under Occupational Safety and Health Administration (OSHA) regulations, only equipment listed and approved by the Mine Safety and Health Administration (MSHA) and the National Institute for Occupational Safety and Health (NIOSH) may be used for respiratory protection. Also under the regulations, each site on which respiratory protective equipment is used must implement a respirator program (including training and medical certification) in compliance with OSHA's Respiratory Protection Standard (29 CFR 1910.134); see also ANSI standard Z88.2-1992, Practices for Respiratory Protection.
6.F.2.4.1
Types of Respirators
Several types of nonemergency respirators are available for protection in atmospheres that are not immediately dangerous to life or health but could be detrimental after prolonged or repeated exposure. Other types of respirators are available for emergency or rescue work in hazardous atmospheres from which the wearer needs protection. In either case, additional protection may be required if the airborne contaminant is of a type that could be absorbed through or irritate the skin. For example, the possibility of eye or skin irritation may require the use of a full-body suit and a full-face mask rather than a half-face mask. For some chemicals the dose from skin absorption can exceed the dose from inhalation.
The choice of the appropriate respirator to use in a given situation depends on the type of contaminant and its estimated or measured concentration, known exposure limits, and hazardous properties. The degree of protection afforded by the respirator varies with the type. Four main types of respirators are currently available:
-
Chemical cartridge respirators can be used only for protection against particular individual (or classes of) vapors or gases as specified by the respirator manufacturer and cannot be used at concentrations of contaminants above that specified on the cartridge. Also, these respirators cannot be used if the oxygen content of the air is less than 19.5%, in atmospheres immediately dangerous to life, or for rescue or emergency work. These respirators function by trapping vapors and gases in a cartridge or canister that contains a sorbent material, with activated charcoal being the most common adsorbent. Because it is possible for significant breakthrough to occur at a fraction of the canister capacity, knowledge of the potential workplace exposure and length of time the respirator will be worn is important. It may be desirable to replace the cartridge after each use to ensure the maximum available exposure time for each new use. Difficulty in breathing or the detection of odors indicates plugged or exhausted filters or cartridges or concentrations of contaminants higher than the absorbing capacity of the cartridge, and the user should immediately leave the area of contamination. Chemical cartridge respirators must be checked and cleaned on a regular basis. New and used cartridges must not be stored near chemicals because they are constantly filtering the air. Cartridges should be stored in sealed containers to prevent chemical contamination.
Respirators must fit snugly on the face to be effective. Failure to achieve a good face-to-face piece seal (for example, because of glasses or facial hair) can permit contaminated air to bypass the filter and create a dangerous situation for the user. Respirators requiring a face-to-face piece seal should not be used by those with facial hair, for whom powered air-purifying or supplied-air respirators are at times appropriate. Tests for a proper fit must be conducted prior to selection of a respirator and verified before the user enters the area of contamination.
Organic vapor cartridges cannot be used for vapors that are not readily detectable by their odor or other irritating effects or for vapors that will generate sub-
-
stantial heat upon reaction with the sorbent materials in the cartridge.
-
Dust, fume, and mist respirators can be used only for protection against particular, or certain classes of, dusts, fumes, and mists as specified by the manufacturer. The useful life of the filter depends on the concentration of contaminant encountered. Such particulate-removing respirators usually trap the particles in a filter composed of fibers; they are not 100% efficient in removing particles. Respirators of this type are generally disposable. Examples are surgical masks and 3M® toxic-dust and nuisance-dust masks. Some masks are NIOSH-approved for more specific purposes such as protection against simple or benign dust and fibrogenic dusts and asbestos.
Particulate-removing respirators afford no protection against gases or vapors and may give the user a false sense of security. They are also subject to the limitations of fit.
-
Supplied-air respirators supply fresh air to the face piece of the respirator at a pressure high enough to cause a slight buildup relative to atmospheric pressure. As a result, the supplied air flows outward from the mask, and contaminated air from the work environment cannot readily enter the mask. This characteristic renders face-to-face piece fit less important than with other types of respirators. Fit testing is, however, required before selection and use.
-
Supplied-air respirators are effective protection against a wide range of air contaminants (gases, vapors, and particulates) and can be used where oxygen-deficient atmospheres are present. Where concentrations of air contaminants could be immediately dangerous to life, such respirators can be used provided (1) the protection factor of the respirator is not exceeded and (2) the provisions of OSHA's Respiratory Standard (which indicates the need for a safety harness and an escape system in case of compressor failure) are not violated.
The air supply of this type of respirator must be kept free of contaminants (e.g., by use of oil filters and carbon monoxide absorbers). Most laboratory air is not suitable for use with these units. These units usually require the user to drag lengths of hose connected to the air supply, and they have a limited range.
-
The self-contained breathing apparatus (SCBA) is the only type of respiratory protective equipment suitable for emergency or rescue work. Untrained personnel should not attempt to use them.
6.F.2.4.2
Procedures and Training
Each area where respirators are used should have written information available that shows the limitations, fitting methods, and inspection and cleaning procedures for each type of respirator available. Personnel who may have occasion to use respirators in their work must be thoroughly trained, before initial use and annually thereafter, in the fit testing, use, limitations, and care of such equipment. Training should include demonstrations and practice in wearing, adjusting, and properly fitting the equipment. OSHA regulations require that a worker be medically certified before beginning work in an area where a respirator must be worn (OSHA Respiratory Standard, 29 CFR 1910.134(b)(10)).
6.F.2.4.3
Inspections
Respirators for routine use should be inspected before each use by the user and periodically by the laboratory supervisor. Self-contained breathing apparatus should be inspected at least once a month and cleaned after each use.
6.F.2.5 Safety Showers and Eyewash Fountains
6.F.2.5.1
Safety Showers
Safety showers should be available in areas where chemicals are handled. They should be used for immediate first aid treatment of chemical splashes and for extinguishing clothing fires. Every laboratory worker should know where the safety showers are located in the work area and should learn how to use them. Safety showers should be tested routinely to ensure that the valve is operable and to remove any debris in the system.
The shower should be capable of drenching the subject immediately and should be large enough to accommodate more than one person if necessary. It should have a quick-opening valve requiring manual closing; a downward-pull delta bar is satisfactory if long enough, but chain pulls are not advisable because they can hit the user and be difficult to grasp in an emergency. It is preferable to have drains under safety showers to reduce the risks associated with the water.
6.F.2.5.2
Eyewash Fountains
Eyewash fountains should be required in research or instructional laboratories if substances used there present an eye hazard or if unknown hazards may be encountered. An eyewash fountain should provide a soft stream or spray of aerated water for an extended period (15 minutes). These fountains should be located close to the safety showers so that, if necessary, the eyes can be washed while the body is showered.
6.F.2.6 Storage and Inspection of Emergency Equipment
It is often useful to establish a central location for storage of emergency equipment. Such a location should contain the following:
-
self-contained breathing apparatus,
-
blankets for covering the injured,
-
stretchers (although it is generally best not to move a seriously injured person and to wait for qualified medical help to provide this service),
-
first aid equipment (for unusual situations such as exposure to hydrofluoric acid or cyanide, where immediate first aid is required), and
-
chemical spill cleanup kits and spill control equipment (e.g., spill pillows, booms, shoe covers, and a 55-gallon drum in which to collect sorbed material). (Also consult Chapter 5, sections 5.C.11.5 and 5.C.11.6.)
Safety equipment should be inspected regularly (e.g., every 3 to 6 months) to ensure that it will function properly when needed. It is the responsibility of the laboratory supervisor or safety coordinator to establish a routine inspection system and to verify that inspection records are being kept.
Inspections of emergency equipment should be performed as follows:
-
Fire extinguishers should be inspected for broken seals, damage, and low gauge pressure (depending on type of extinguisher). Proper mounting of the extinguisher and its ready accessibility should also be checked. Some types of extinguishers must be weighed annually, and periodic hydrostatic testing may be required.
-
Self-contained breathing apparatus should be checked at least once a month and after each use to determine whether proper air pressure is being maintained. The examiner should look for signs of deterioration or wear of rubber parts, harness, and hardware and make certain that the apparatus is clean and free of visible contamination.
-
Safety showers and eyewash fountains should be examined visually and their mechanical function should be tested. They should be purged as necessary to remove particulate matter from the water line.
6.G EMERGENCY PROCEDURES
The following emergency procedures are recommended in the event of a fire, explosion, spill, or medical or other laboratory accident. These procedures are intended to limit injuries and minimize damage if an accident should occur. Telephone numbers to call in emergencies should be posted clearly at all telephones in hazard areas.
-
Have someone call for emergency help. State clearly where the accident has occurred and its nature.
-
Ascertain the safety of the situation. Do not enter or reenter an unsafe area.
-
Render assistance to the people involved and remove them from exposure to further injury. 4. Warn personnel in adjacent areas of any potential risks to their safety.
-
Render immediate first aid; appropriate measures include washing under a safety shower, administration of CPR by trained personnel if heartbeat and/or breathing have stopped, and special first aid measures.
-
Extinguish small fires by using a portable extinguisher. Turn off nearby equipment and remove combustible materials from the area. For larger fires, contact the appropriate fire department promptly.
-
Provide emergency personnel with as much information as possible about the nature of the hazard.
In case of medical emergency, laboratory personnel should remain calm and do only what is necessary to protect life.
-
Summon medical help immediately.
-
Do not move an injured person unless he or she is in danger of further harm.
-
Keep the injured person warm. If feasible, designate one person to remain with the injured person. The injured person should be within sight, sound, or physical contact of that person at all times.
-
If clothing is on fire and a safety shower is immediately available, douse the person with water; otherwise, move the person to the floor and roll him or her around to smother the flames.
-
If harmful chemicals have been spilled on the body, remove them, usually by flooding the exposed area with sufficient running water from the safety shower, and immediately remove any contaminated clothing.
-
If a chemical has splashed into the eye, immediately wash the eyeball and the inner surface of the eyelid with plenty of water for 15 minutes. An eyewash fountain should be used if available. Forcibly hold the eye open to wash thoroughly behind the eyelids.
-
If possible, determine the identity of the chemical and inform the emergency medical personnel attending the injured person.