6
Methodologies for Assessment of Structural Performance
Current structural design and analytical procedures used by the aeronautics industry are largely semiempirical, even though significant improvements have occurred in structural analysis methodology over the last two decades. Preliminary design efforts require estimates using relatively quick, easy to use, and insightful tools to allow sensitivity studies among different structural design options. Final design efforts require tools that provide a precise and accurate assessment of the structural design.
Finite element analysis methods are routinely used for predicting the stress, strain, and displacement fields in complex structural geometries. Superior graphical interfaces have significantly improved pre-and post-processing of data files. Automated mesh generation, mesh refinement, and automated adaptive remeshing have resulted in major improvements in the efficiencies of model development and analysis and in the accuracies of the numerical solutions. Post-processing algorithms and graphical interfaces have significantly enhanced the ability of the analyst to interpret the results of the stress analysis. Along with these improved analytical and software tools, advances in the available computing capabilities have been rapid. In spite of these advances, the reliable prediction of structural failure modes, ultimate strength, residual strength, and fatigue life has remained elusive to the structural engineer. Standard practice still relies heavily on extensive testing at the subelement, element, subcomponent, component, and full-scale levels. Design details are frequently optimized through test programs. Scale-up effects are handled through a building-block approach that relies on testing to verify the anticipated structural performance at each scale level. Full-scale static and fatigue tests are conducted to identify "hot spots," to verify adequate structural integrity for design limit and ultimate loads, and to verify durability and damage tolerance requirements. Hence the designation "semiempirical" for current practice, which is necessarily expensive and time-consuming.
In spite of over 60 years of experience by researchers and industry in designing metallic structure and 25 years of experience designing composite structure, the lack of rigorous analytical methods to predict residual strength and fatigue life can inhibit the cost-effective introduction of advanced materials with superior specific strength and stiffness relative to current conventional materials. Continuing efforts are needed to develop—and insert into standard engineering practice— advanced mechanics-based analytical prediction methodologies that would allow innovative designs to be evaluated and optimized at acceptable cost. Such methods would also provide the means to assess the effects of service history on the durability and damage tolerance performance of the structure. This chapter examines current issues and assess the impact of advanced methods on the introduction of new materials and the design of more-structurally efficient and cost-effective primary structures on next-generation aircraft.
ANALYTICAL PREDICTION METHODOLOGY FOR STRUCTURAL INTEGRITY
Metallic Materials
Metallic materials tend to fail due to the formation and growth of a dominant microcrack that eventually reaches a critical length and then more rapidly propagates to failure. However, the recently recognized phenomenon of multiple-site damage has been shown to be a critical issue in aging of commercial transport aircraft. While fracture mechanics is now a mature part of standard practice in engineering, rigorous prediction methodology only exists for brittle materials that exhibit limited plasticity. The fatigue crack growth behavior and fracture processes exhibited by ductile materials are reasonably well understood. However, the development of rigorous elastic-plastic analytical methods has been hampered by the complicated three-dimensional effects present in most structures. In thin-sheet planar structural components, local constraint effects on the development of plastically deformed material frequently result in highly inaccurate solutions when obtained from two-dimensional plane-stress or plane-strain assumptions. Three-dimensional analyses of cracks in geometries such as lugs and fittings may be inaccurate due to uncertainties in modeling the crack-front singularity.
Three-dimensional models of the geometry and crack configurations are computationally intensive and have been impractical for the practicing engineer. Therefore, improved
engineering methods for fracture mechanics using two-dimensional approximations that yeild reliable results are required for more-accurate, structural integrity prediction methodology. In addition, methods that compute reliable, stress intensity factors for various crack geometries using stresses obtained from uncracked stress analysis models should also be developed.
Most fracture mechanics analyses are performed on refined models of local structural details that use stress boundary conditions determined from a global structural analysis. Therefore, the computed stress intensity factors will never be more accurate than the global structural analysis, regardless of the sophistication of the fracture mechanics model. The structural models must account for global details such as frames, stiffeners, tear straps, shear ties, and shear clips; must accurately capture local details such as interference-fit stresses and clamp-up stresses at riveted fasteners; and must also accurately treat combined load effects and geometric nonlinear behavior. This level of fidelity in the local stress analysis can only be achieved by the development of more-robust and computationally efficient structural analysis methods that exploit global-local and other hierarchical computational strategies. However, it is not sufficient to only generate highly accurate local stresses. Other features that promote crack initiation and growth need to be modeled as well. These features include metal-forming defects, machining and fabrication defects, residual stresses such as from drilling holes and forming rivets, and mechanisms such as fretting and pitting corrosion. These features may be modeled best by an approach such as the "equivalent initial flaw size" to facilitate the fatigue and residual strength analysis.
The design of longer-life and more-durable metallic structures could also be significantly enhanced by the incorporation of models that reliably account for the effects of the environment on fatigue life and residual strength. The aluminum alloys currently used in airframe structures are highly susceptible to corrosion damage. Elaborate corrosion prevention and control programs are used by the manufacturers and airline operators. These programs are successful at delaying the development of widespread corrosion, but are not 100 percent effective in preventing localized effects such as pitting that may cause crack nucleation. Furthermore, fatigue crack growth rates may be significantly accelerated when newly created fracture surfaces are exposed to the environment.
An improved understanding of the role of the environment on alloy behavior and better analytical methods to reliably predict spectrum loading effects, such as load sequencing, overloads, and stress reversals, on fatigue life will remove conservatism in current designs and may accelerate the use of advanced materials for corrosion-critical components. For those alloys that exhibit a strong crack-closure effect, models should be developed that incorporate the effects of the environment into closure mechanics such as plasticity-induced closure. For other materials, superposition models need to be developed which attempt to treat time-dependent effects and cyclic mechanical load effects independently. Typically, these models are computationally simple and rely on Paris Law formulations, but may require more test data to fully characterize mean stress and stress ratio effects.
The effects of widespread fatigue damage, including multiple-site damage (MSD) and multiple-element damage (MED), have been critical in the understanding of aging of metallic aircraft structures. Structural mechanics research is needed to develop analytical methods to predict the residual strength of a thin-sheet stiffened shell structure with fatigue cracks or damage caused by an in-flight accident. Structural analysis methods are needed to evaluate the damage tolerance of aircraft for MSD and MED and to provide a basis for assessing the integrity of repairs on existing aircraft structures. Stiffened shell analysis methods should include automated, adaptive remeshing capability, as well as a capability to analyze structures with nonlinear materials properties and at large deformations. These improved methods should be integrated into the structural analysis methodology to predict fatigue crack growth and residual strength of aircraft structures. In cooperation with industry, a structural test program, through the subcomponent and subscale test article level, will be necessary to verify the integrated fracture mechanics and structural analysis methods.
Composite Materials
In contrast to metallic alloys, composite materials exhibit complex failure modes that may involve the interaction of several different damage mechanisms. The complexity of the failure modes becomes a major design consideration when addressing durability and damage tolerance requirements. The prediction of composite structural behavior is complicated by the fact that there are virtually no material properties of the constituents that can be measured independently and used to predict the response of the composite. Most design allowables depend on the as-cured properties of the constituents and the fiber architecture. The process of inferring local (micro) behavior from global (macro) response tends to promote empirically based design practices.
The current design practices rely heavily on empirical approaches to conservatively estimate the effects of damage on durability and damage tolerance. For example, simple tests such as open-hole compression and compression-after-impact tests are often used to establish "knock-down" factors for reducing the working strain levels to avoid damage growth. In the absence of mechanical methods to predict damage initiation, growth, and failure modes, all test data must be obtained on the specific laminate stacking sequence or fiber preform architecture to be used in the design. As described in the introduction to part 2, structural concepts are tested at the
element and subcomponent level to confirm the suitability of the structural design parameters and to couple coupon-level material behavior and test data to the actual structural behavior. This approach would be significantly enhanced by the introduction of rigorous, mechanics-based analytical methodology that would enable the design of composite structures that are more structurally efficient.
There are several key technical barriers to developing reliable methods to predict failure of composite structure. The first barrier is related to the complex three-dimensional stress states produced by the fiber architecture. The task of developing crack initiation and growth criteria for complex local effects is complicated by the difficulty of isolating an individual damage mechanism and varying the stress states to develop a comprehensive failure criterion.
Second, loading-history-dependent growth laws for individual damage mechanisms and for interacting cracks do not exist. Progress has been made developing damage onset criteria, particularly for those special cases where an individual damage mechanism can be isolated, but three-dimensional models of the material system may be required to predict the correct local stresses to use in the criteria. This results in a massive computational process involving an iterative and incremental loading scheme and may require a very refined finite element mesh with many degrees of freedom. Also, neither fatigue crack growth and life nor stable damage progression prior to catastrophic fracture can be predicted in a rigorous sense because crack growth laws do not exist. Once again, empirical engineering approaches have been developed to avoid these complexities.
Third, residual stresses in the matrix polymer that result from elevated-temperature processing (i.e., curing of thermosets or consolidation of thermoplastics) need to be characterized. Processing residual stresses often leads to the first damage (matrix cracking) in the composite structure. Matrix cracking can eventually lead to delamination, fiber damage, and other damage-mode interactions.
Finally, the understanding of failure mechanisms and associated failure criteria, including interactions that take place between different failure modes at length scales ranging from constituent-level (e.g., matrix cracking) to component-level (e.g., buckling) is incomplete. The complexity of the (inhomogeneous) composite materials and their array of anisotropic material strengths give rise to the development of a corresponding array of damage and failure modes in these materials that must be understood and correctly modeled. Hence, there is a need to develop understandings and representations of the critical damage and failure modes that control the types of structures typical of commercial aircraft.
A report of the National Research Council discusses some of the methods for the assessment and prediction of durability and damage tolerance of composite materials (NRC, 1991). General features of these methods include:
-
Remaining strength and life models are developed and predictions are made for each independent failure mode (such as fiber failure in tension or microbuckling in compression).
-
Mechanical representations of the state of stress and state of material are constructed on the basis of a "representative volume" of the material that is typical of the distributed damage state that controls the remaining stiffness and strength of the composite.
-
Various methods are used to characterize and monitor the degradation rate of the strength of composites.
-
Micromechanics (mechanics analysis at the fiber/matrix level of representation) is increasingly used for remaining strength modeling, for the calculation of stiffness change (which leads to internal stress redistribution), and for the estimation of the remaining strength for a given failure mode.
-
Statistical considerations are essential for the correct representation of the long-term behavior of composites. Composites typically fail because of the statistical accumulation of defects, which eventually interact to create a critical condition.
-
Time-dependent behavior such as viscoelastic creep, creep rupture (driven by, for example, internal stress redistribution or oxidation), and aging are typically important in the consideration of the long-term durability and damage tolerance of polymer-matrix composites.
Two methodologies for predicting remaining strength (damage tolerance) and life of composite structure for aeronautical applicators are currently being researched and developed for potential use in design. The first is the use of "damage mechanics" to predict the changes in stiffness that occur during service life (Talreja, 1985; Simo and Ju, 1987; Lee et al., 1989; Shapery, 1990). This approach is becoming common for the purpose of following the development of damage and for interpreting the changes in stiffness of the structure as well as at the microstructural level in composites.
The second methodology is the use of micromechanics and kinetic theory to predict remaining strength. A schematic diagram of such an approach appears in figure 6-1. Micromechanical representations of the fundamental composite strengths are constructed in terms of the constituents, their geometry, and their arrangement (Reifsnider and Stinchcomb, 1986; Reifsnider, 1991a,b, 1992; Reifsnider and Gao, 1991; Gao and Reifsnider, 1993; Xu and Reifsnider, 1993). The constitutive parameters in these strength models are studied as a function of the service inputs and environments using kinetic (or rate) theory, allowing fatigue, creep, creep rupture, aging, oxidation, and other time-dependent and cycle-dependent effects to be introduced at the constituent level. These constituent effects are combined and their collective effect assessed by the micromechanics models mentioned
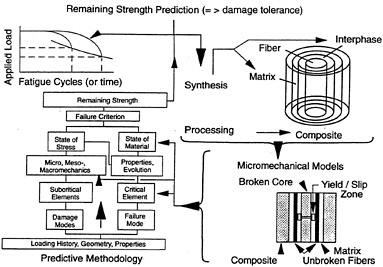
FIGURE 6-1 Methodology for predicting remaining strength in composites.
earlier, without the need for empirical or phenomenological postulates, which is a major advantage.
More reliable and robust mechanics-based analytical methodology to predict structural failure modes, life, and residual strength need to be developed to support the introduction of new materials and to contribute to the development of efficient and optimized structural designs. While semiempirical engineering approaches will continue to be refined, the most promising methods are those that will exploit the dramatic improvements in computer capability and numerical methods. The three-dimensional behavior of composite materials is well suited to global, local, and hierarchical methods of analysis. New methods can efficiently couple local material-level damage mechanisms to global responses, such as load redistribution, geometric nonlinear and instability phenomena, and predict structural failure modes.
Adhesive-Bonded Joints
Key structural integrity issues continue to limit the widespread acceptance of adhesive bonding as a viable joining technology for commercial transport aircraft. This is partly because of negative experiences with early bonding technology and partly because of unresolved technological barriers such as those described in chapter 2 (e.g., inspection methods). Both strength-based (Hart-Smith, 1990) and fracture mechanics-based (Rakestraw et al., 1994) design methods have been developed to determine appropriate bonding parameters to achieve the desired load transfer capability.
Interfacial properties are crucial in the understanding of long-term durability of adhesive-bonded joints, especially under harsh environmental conditions encountered in aircraft service (Kinloch, 1979; Kinloch and Osiyemi, 1993). Fracture mechanics testing and analytical techniques can be used to provide quantitative evaluations of adhesive-bonded structure (Rakestraw et al., 1994). Further work is needed to develop fracture mechanics-based adhesive tests, such as double-cantilever-beam and edge-notch bend tests, and analytical techniques that can provide information concerning rate-dependent failure characteristics and the influence of environmental effects.
Surface preparation and bonding processes are very unforgiving, placing more reliance on inspection technology to assess structural integrity. While there are methods under development that appear to have high reliability to detect disbonded regions, there are currently no reliable methods to assess bond integrity in cases where there are no disbonds but the existing bond is of poor quality and does not have the expected load transfer and strength characteristics. This basic problem must be resolved through improved bonding technology, better fail-safe designs, or more reliable inspection methods before expanded applications of adhesive bonding will be implemented into new aircraft designs.
ADVANCED COST AND STRUCTURAL OPTIMIZATION METHODOLOGY
Major advances in computing technology can have a significant impact on the cost-effective incorporation of high-performance materials into both new and derivative aircraft. At this writing, optimistic projections suggest the availability in several years of moderately priced, powerful desktop computers with massively parallel processing (MPP) capabilities. This computing power would enable designers and analysts to make rapid, theoretical performance analyses of a very large number of candidate material and structural configurations. Obviously, the results would be no more reliable than the assumptions underlying the numerical formulations. However, in conjunction with the development of the improved mechanics-based analytical methodologies described in the previous section, the computing power afforded by MPP should go a long way toward reducing the time-consuming, expensive testing now needed to validate the performance of new materials and structural configurations.
Cost-effectiveness has already been emphasized as a pre-eminent driver in the present industrial climate facing the airlines. But estimating the real cost of introducing a new material into an aircraft is a task of incredible difficulty, requiring assessments of costs of myriads of contributory elements—not just the obvious cost of acquisition, processing, manufacturing, engineering, maintenance, but also the elusive costs of money, time, and risk. (In comparison, stress analysis is trivial!) A willingness by industry, government, and academia to grapple with sophisticated, rational cost analyses is starting to emerge. This trend should be encouraged. With precise, visible exposure of assumptions and definitions, and prudent recognition of uncertainties, credible cost analyses can help industry steer a sensible course between competition-vulnerable stagnation and risky, premature innovation. Furthermore, the full potential of such cost modeling and analyses dictates its concurrent integration into the high-speed, high-power, numerical design and analysis procedures anticipated in the future. The great danger, to be assiduously guarded against, is that cost models will start to be treated as natural laws. They will never be exactly right; by their nature they will need unending revision. With appropriately chosen criteria of merit, an integrated design-analysis-cost model can provide the basis for a numerical optimization package that in conjunction with MPP, would constitute a powerful tool for the cost-effective utilization of new materials.
SUMMARY
Current structural design and analytical procedures used by the aeronautics industry are largely semiempirical, even though significant improvements have occurred in structural analysis methodology over the last two decades. Continuing efforts are needed to develop—and insert into standard engineering practice—advanced mechanics-based analytical prediction methodologies that would allow innovative designs to be evaluated and optimized at acceptable cost. Such methods would also provide the means to assess the effects of service history on the durability and damage tolerance performance of the structure.
For metallic structures, fracture mechanics-based methods are fairly well developed. Work is needed to improve the analytical capabilities that account for the effects of crack and component geometry; the effects of stress concentrations and manufacturing defects, corrosion, environmental exposure; and existing fatigue damage. Improved methods should be integrated into the structural analysis methodology to predict fatigue crack growth and residual strength of aircraft structures.
For composite structure, complex failure modes that may involve the interaction of several different damage mechanisms are major design considerations when addressing durability and damage tolerance requirements. There are several key technical barriers to developing reliable methods to predict failure of composite structure, including incomplete understanding of complex three-dimensional stress states, damage progression laws, processing residual stresses, and understanding of failure mechanisms and associated failure criteria.
For adhesive-bonded structure, further work is needed to develop fracture mechanics-based adhesive tests and analytical techniques that can provide information concerning rate-dependent failure characteristics and the influence of environmental effects.
Cost has been identified as an important driver in the application of new materials and structures technology on commercial transports. With appropriately chosen criteria of merit, an integrated design-analysis-cost model can provide the basis for a numerical optimization package that would constitute a powerful tool for the cost-effective utilization of new materials.