2
Development of Vehicle Subsystems
Candidate Systems
The ultimate success of the PNGV program will depend on integrating R&D programs that can collectively improve the fuel efficiency of automobiles within the very stringent boundary conditions of size, reliability, durability, safety, and affordability of today's vehicles. At the same time, the vehicles must meet even more stringent emission and recycling levels and must use components that can be mass produced and maintained in a manner similar to current automotive products.
In order to achieve the Goal 3 fuel economy upper limit of 80 mpg, the energy conversion efficiency of the chemical conversion system (e.g., a power plant, such as a compression-ignition direct-injection [CIDI] engine or a fuel cell) averaged over a driving cycle will have to be at least 40 percent, approximately double today's efficiency. This extremely challenging goal will require assessing many concepts. For example, the primary power plant will have to be integrated with energy-storage devices, and the vehicle structure will have to be built of lightweight materials to reduce vehicle weight.
The hybrid electric vehicle (HEV), which is the PNGV power train of choice, uses an energy-storage device to reduce the fluctuations in demand on the primary power plant, thereby permitting a smaller power plant that operates at optimum conditions for increased energy-conversion efficiency and reduced emissions, as well as recovery of a significant fraction of the vehicle's kinetic energy during braking operations. The PNGV is currently sponsoring research on batteries as energy-storage devices.
Achieving the high fuel economy objective for the Goal 3 vehicle will require more than improving the energy-conversion efficiency of the power train (including energy converters and transmissions) and reducing other energy losses in the vehicle. Vehicle weight reduction through new vehicle designs and lightweight materials will be extremely important for achieving the very ambitious fuel-economy objectives.
The committee re-evaluated the candidate energy-conversion and energy-storage technologies that survived the 1997 technology selection process, as well as candidate electrical and electronic systems and advanced structural materials for the vehicle body. The technologies evaluated in this chapter are listed below:
- four-stroke internal-combustion reciprocating engines
- fuel cells
- electrochemical storage systems (rechargeable batteries)
- electrical and electronic power-conversion devices
- structural materials
The committee reviewed R&D programs for each of these technologies to assess progress so far and the developments required for the future. The updated PNGV Technical Roadmap provides a good summary of the program goals (PNGV, 1998). In the committee's opinion, the PNGV has made substantial progress in assessing the potential of most candidate systems and identifying critical technologies that must be addressed to make each system viable. As discussed further in the remainder of the report, significant progress has been made toward meeting the program's goals. A few exceptions are noted in the sections describing specific technologies.
Because the global competitiveness of the U.S. automotive industry is a key consideration in the development of advanced automotive technologies, the committee also describes some international developments in the technology areas, based both on its own knowledge and experience and on selected information-gathering activities. An extensive review of worldwide developments, however, was not part of the committee's task. Additional information can be found in the fourth report (NRC, 1998a).
Internal-Combustion Reciprocating Engines
To meet the Goal 3 fuel economy target, an engine will have to be integrated into an HEV configuration. The 4SDI (four-stroke direct-injection) technical team continues to research four potential engine configurations as power plants for the HEV (see Figure 2-1). The CIDI engine, the homogeneous-charge compression-ignition engine, the gasoline direct-injection (GDI) engine, and the homogeneous-charge spark-ignition engine are all being evaluated as candidate power plants.
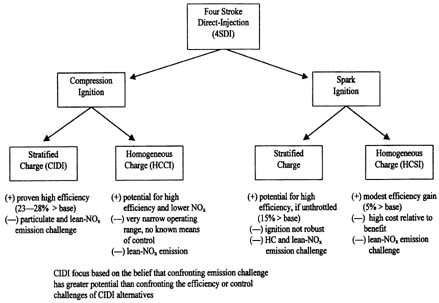
Figure 2-1
Alternatives for energy conversion. The baseline engine is the port fuel injection homogeneous charge spark injection for model year 1993.
SOURCE: Belaire et al. (1998).
The 4SDI technical team continues to believe that the CIDI engine has the potential for the highest fuel-conversion efficiency. In addition to better fuel economy, the performance of the CIDI engine is superior to other engine types in terms of evaporative, cold-start, hydrocarbon, and carbon monoxide (CO) emissions. However, there are still significant challenges to be overcome in the development of CIDI HEV systems that meet all of the PNGV targets. These challenges include reducing the emissions of nitrogen oxides (NOx) and particulates, reducing the weight of the power plant, and reducing costs.
For other candidate power plants, such as the GDI engine, reducing emissions may represent less of a challenge than increasing the fuel economy. The exhaust-gas after-treatment systems for gasoline engines are technically more mature than those for CIDI engines, and there are reasons to believe that the PNGV emission targets, and perhaps even the more stringent research targets, could be met with GDI engines. 1 However, it is not likely that the Goal 3
fuel-economy target (triple the fuel economy of current vehicles) could be achieved with GDI engines. Overall system cost remains a considerable challenge for all engines.
In the past year, the necessity of taking an integrated approach to the power train has become apparent. That is, the development should involve the entire power train system, which includes the engine, drivetrain, fuel, exhaust-gas after-treatment, and sensors and controls, to take into account the synergistic or antagonistic effects of individual components of the system. According to the 4SDI technical team, the emission targets cannot be met with a reciprocating piston, combustion power plant through combustion control alone, regardless of the power plant under investigation. Meeting the proposed targets will require both fuel modifications and extensive exhaust-gas after-treatment. Therefore, in addition to ongoing work on combustion control, research in these two areas has increased markedly during the past year.
Technical Targets
All of the USCAR manufacturers are developing in-house concept vehicles, and all are developing a CIDI hybrid system as one of the leading candidate power trains. The technical targets for the CIDI engine for the years 1998 and 2004 are listed in Table 2-1, but because the manufacturers are currently involved in proprietary vehicle development, it is not possible to list the current performance numbers for the CIDI engine systems.
The USCAR partners are making good progress toward meeting the targets for thermal efficiency, specific power, package volume, noise, and vibration. The emissions, exhaust-gas after-treatment performance, and cost targets represent significant challenges. Because the engine systems are still under development, the emissions performance and costs are either unknown or at a very early stage of optimization.
Program Status, Progress, and Highlights
The 4SDI technical team continues to interact extensively with other working groups both within and outside PNGV to maximize its coverage. The team has established cooperative relationships with energy companies to obtain special fuels for testing and has been working with the USCAR Low Emission Program to improve port-fuel-injected (PFI) spark-ignition (SI) engines and spark-ignition direct-injection (SIDI) engines. The 4SDI technical team is also involved in cooperative R&D agreements (CRADAs) between the national laboratories of the U.S. Department of Energy (DOE), industries, and universities to study the fundamentals of combustion and the development and performance of exhaust-gas after-treatment systems.
TABLE 2-1 Current Performance Characteristics and Targets of CIDI Engine Systems
Characteristic |
1998 Target |
2004 Target |
Best BTE |
43% |
45% |
BTE @ 2,000 rpm, 2 bar BMEP |
27% |
30% |
Displacement specific power |
40kW/liter |
45kW/liter |
Weight specific power |
0.53kW/kg |
0.63kW/kg |
Package volume |
0.13 m3 |
0.09m3 |
Mount vibration maximum @ firing order |
47N |
40N |
One-meter noise maximum |
97dBA |
90dBA |
Engine-out NOx emissions |
2.7g/k Wh |
1.5g/kWh |
Engine-out PM emissions |
0.26g/kWh |
0.16g/kWh |
NOx after-treatment efficiency |
25% |
40% |
PM after-treatment efficiency |
0% |
75% |
FTP 75 NOx emissions |
0.4g/mile |
0.2g/mile |
FTP 75 PM emissions |
0.06g/mile |
0.04g/milea |
a The PNGV target is 0.04 g/mile, whereas the research target, sometimes referred to as the ''stretch research objective," was set in 1997 at 0.01 g/mile (NRC, 1998a). Measuring levels of particulates at 0.01 g/miles is a challenge to current measurement techniques whose variability is as high as the research objective. Source: Based on Table III-F in the Technical Roadmap (PNGV, 1998). Acronyms: FTP = federal test procedure; BTE = brake thermal efficiency; BMEP = brake mean effective pressure; PM = particulate matter; N = newtons; dBA = decibels absolute. |
Engines
Even though the CIDI engine in an HEV configuration is considered the most likely power plant system for meeting the Goal 3 fuel economy target, other configurations of the reciprocating piston engine, including further development of SIDI gasoline engines and PFI SI engines, are being investigated in parallel programs. In addition, research on homogeneous-charge compression-ignition engines has been initiated at the Combustion Research Facility at Sandia National Laboratories (SNL) in Livermore, California. Although developments during the past year did not change the relative rankings of the engine types in terms of their potential fuel economy, the challenge of meeting the projected exhaust emission target (NOx level of 0.2 g/mile, and a research target for particulate matter of 0.0 1 g/mile) represents a considerable stretch at this time, especially for the CIDI engine.
A number of notable accomplishments in the 4SDI area achieved during the last year are listed below:
- Desirable characteristics of a fuel-injection system have been identified,
- and a prototype injection system has been fabricated. The injection system is a piezoelectric system with variable rate shape and controlled opening and closing nozzle capabilities. Tests using this injection system will be conducted at FEV.
- The Ford direct-injection, aluminum-block, through-bolt assembly (DIATA) engine was demonstrated to have specific power output levels comparable with state-of-the-art diesel engines and noise, vibration, and harshness levels comparable to state-of-the-art SI engines. Also a dimethyl ether fueling system has been developed for the DIATA engine to test this alternate fuel.
- Initial results of the fundamental combustion studies at SNL, Wayne State University, and the University of Wisconsin were reported. In-cylinder combustion visualization experiments are under way at SNL; additional engine tests are being run at Wayne State University; and three-dimensional simulations are being performed at the University of Wisconsin. In addition, an homogeneous-charge compression-ignition program has been initiated at SNL.
- Preliminary assessments of the incremental cost, including emissions controls, associated with replacing the current SI engine with an advanced CIDI engine have been made. A breakdown of the costs shows an increase of approximately $900 compared to the target cost.
Fuel Formulation
The PNGV emission targets represent a technological stretch, particularly for the CIDI engine. Discussions are under way among regulatory bodies and various environmental groups (Environmental Protection Agency [EPA], the California Air Resources Board [CARB], and the South Coast Air Quality Management District [SCAQMD], among others) about reducing the regulated levels of emissions.2 In response, PNGV is investigating the requirements of reformulated or different fuels for CIDI engines:
- DOE, which has taken the lead in involving the USCAR partners and energy companies, has been organizing meetings and technical interchanges.
-
- The reduction of particulate matter was demonstrated for three diesel fuels: a very low-sulfur fuel, a Fischer-Tropsch fuel, and DMM15 (a blend of low-sulfur diesel fuel and 15 percent dimethoxymethane, which reduced particulate matter emissions by 60 percent). These results demonstrated that emissions can indeed be reduced through fuel modifications.
- Test fuels were delivered to each of the three USCAR partners to be incorporated into their engine development programs.
- The EPA completed comparisons of emissions from a premier diesel-based fuel with Swedish City Diesel fuel (a very low-sulfur, low-aromatic, high-cetane fuel), which demonstrated a particulate matter reduction and a nominal NOx reduction. Tests were conducted in engines of larger size than would be used in the vehicles under development in the PNGV program.
- The DOE initiated a program to promote collaboration with energy companies in the development of fuels capable of achieving the new research target in CIDI engines.
- New programs for testing alternative fuels for CIDI engines were started by the USCAR partners.
- A fueling system for dimethyl ether, a possible alternative fuel, was developed by AVL List GmbH.
- U.S. automobile manufacturers suggested a 30 ppm sulfur standard to the fuels industry.
The 4SDI technical team projects that the CIDI HEV performance could meet the triple fuel economy targets (Goal 3) at Tier 2 levels with a reformulated diesel fuel with a very high cetane number, very low aromatics, and no sulfur. They also predict that meeting the emission targets will not be possible without a reformulated fuel.
Exhaust-Gas After-treatment
Although reformulated fuels can significantly lower the emission of particulate matter (e.g., a low sulfur, DMM 15 fuel) relative to a premier diesel fuel, their effect on NOx emissions is small (<10 percent). Therefore, an after-treatment system that meets the cost and performance target remains a critical challenge.
Two lean-NOx catalyst technologies are under active development for the CIDI engine by the PNGV program and elsewhere. The first, catalyst materials supported on a ceramic monolith structure, can reduce NOx to nitrogen by reaction with hydrocarbons under lean (low fuel-air ratio) engine operating conditions. Because the hydrocarbon levels in CIDI engine exhaust are low, additional hydrocarbons must be added upstream of the catalyst to achieve this reduction, which lowers fuel economy by a few percent. The national laboratories are
actively engaged in developing promising catalytic materials as part of the PNGV program, and technology transfer to the major catalyst manufacturers has been initiated. In October 1998, DOE's Office of Advanced Automotive Technologies released a solicitation for proposals for much larger, more focused two to three year engineering-development projects. The solicitation is intended to involve the automotive manufacturers, component suppliers, and catalyst suppliers. Awards have been announced and include catalyst suppliers as subcontractors.
In the past year, under the terms of a CRADA, catalyst suppliers have prepared a full-brick, monolithic device for testing using catalyst formulations developed by the national laboratories. NOx removal using the full-brick device is comparable to the removal in laboratory tests using powder catalysts. With the injection of diesel fuel into the exhaust gas, 30 to 35 percent of NOx was removed in a dynamometer test following the federal test procedure (FTP) cycle. Long-term stability tests will be performed with assistance from catalyst manufacturers. The committee is encouraged by the PNGV's increasing emphasis on the development of practical lean-NOx catalyst systems for the CIDI engine and urges PNGV management to pursue these R&D initiatives aggressively.
The second lean-NOx exhaust-treatment technology is plasma-assisted catalysis, where the exhaust flows through a nonthermal (low-temperature) plasma discharge and over a catalytic surface. This technology is at an earlier stage of development than the lean-NOx (selective-reduction) catalyst approach summarized above, and its potential is less clear. The plasma-discharge power requirements would increase vehicle fuel consumption by a few percent. Several national laboratories are actively involved in research on this technology as part of the PNGV program, and results to date are promising. The underlying science is not fully understood, however, and very little engine testing of this technology has been attempted.
The PNGV stated goal for plasma reduction of NOx is a 50 percent reduction in NOx with less than a 5 percent fuel economy penalty. To date, only bench-scale tests of plasma technology have been done at a space velocity3 of one-half the value expected for CIDI engines based on typical engine configurations. N2 production was detected, but no N2O, HNO3, or HONO by-product species. At these low space velocities, using a two-stage packed-bed reactor, NOx reduction was 65 to 70 percent, with a fuel consumption equivalent of 0.5 to 1 percent. These results were obtained with simulated diesel exhaust. Strong temperature dependence of the NOx reduction efficiency was also observed. The committee feels that PNGV should increase its efforts toward understanding, evaluating, and developing nonthermal plasma-catalysis technology, which may prove to be more effective than selective lean-NOx catalytic reduction.
The technical team is encouraging more interactions between researchers on light-duty CIDI engines and the developers of heavy-duty engines. The focus of these interactions is on fuels and after-treatment, including research on lean-NOx catalysis and nonthermal plasma-assisted catalyst systems of exhaust-gas after-treatment. Prototype hydrous metal oxide-supported bulk powder catalysts have shown up to 70 percent NOx conversion efficiency in laboratory experiments at temperatures as low as 170°C. Hydrous metal oxide-supported catalyst on alumina-cordierite monolith cores have shown reduction efficiencies of up to 60 percent at temperatures of approximately 200°C.
Sensors and Controls
To meet the PNGV performance and emission targets, precise control must be maintained over the entire power-train system, ranging from in-cylinder combustion processes to the flow rate of reductant into exhaust-gas after-treatment systems. This can be accomplished only if the requisite sensors and control algorithms are also developed. The development of the sensors (e.g., for combustion, temperature, pressure, emissions, and other parameters) and control technologies is being pursued through the USCAR Low Emission Program. Eight technical approaches to sensors were being investigated: electrochemical, thickness shear-mode quartz resonator (TSM), ion mobility, microwave, surface acoustic wave (SAW), infrared, mass spectrometry, and millimeter wave. Of these technologies, it has been determined that only four are viable: electrochemical, TSM, ion mobility, and microwave. Laboratory testing of prototypes (e.g., NOx sensors) is under way, and the Low Emission Program is performing dynamometer-screening tests of two devices.
Current Program Elements
The key performance challenges for achieving the PNGV targets have been identified in the context of 4SDI engines as achieving the very low required levels of NOx and particulate matter emissions while maintaining performance. The goals of the technical program are to develop enabling technologies in the areas of fuels, combustion systems, after-treatment, and controls and sensors.
An important aspect of the program for the next year is to begin testing integrated systems, i.e., to initiate fuel system, combustion control, and after-treatment programs with suppliers. This will be done through DOE solicitations for both CIDI and SIDI engines. Test programs will be run at the USCAR partners' facilities in conjunction with tests at FEV and AVL List GmbH. Each program will have a slightly different focus. The programs at GM, Ford, and DaimlerChrysler will include special fuel blends in the test matrix, and tentative plans have been made to include after-treatment devices. Passive and active lean-NOx systems, plasma-catalyst systems, particulate and NOx traps, and storage catalysts are being considered.
Engines
In addition to tests on integrated systems, investigations of advanced single-cylinder engines are planned to determine the potential for combustion control via an advanced fuel-injection control. Also, a substantial increase in the homogeneous-charge compression-ignition program at SNL is planned. The objective of these programs is to further a fundamental understanding of combustion regimes and control approaches.
Fuel Formulation
The incorporation of fuel specifications and the effects of various fuels on engine performance and emission systems will continue to be a major focus of the 4SDI technical program. The 4SDI team plans to continue testing fuels at Southwest Research Institute (SWRI) with the objective of optimizing the combustion parameters for a given fuel. DOE and the Engine Manufacturers Association (EMA) are planning a fuels/after-treatment test program, which should be coordinated with the test programs of the USCAR partners. In addition, the teams plan to initiate an investigation of the toxicity and lubricity of reformulated fuels.
Exhaust-Gas After-treatment
The primary objectives of research on the lean-NOx catalytic systems are to enlarge the temperature window of effective catalyst activity and to involve catalyst suppliers in the program. Lawrence Livermore National Laboratory (LLNL), Los Alamos National Laboratory (LANL), Oak Ridge National Laboratory (ORNL), Pacific Northwest National Laboratory (PNNL), and SNL are participating. The project plan is to demonstrate the catalyst performance first using bulk powder, then incorporated into a monolith core, and finally using a full-size brick. In fact, two patents for hydrous metal oxide-supported materials were issued in 1998. Tests on dynamometers of several vendor-supplied bricks are ongoing at ORNL. In 1999, testing will be done with a smaller CIDI engine that is more representative of the power plant for the PNGV concept vehicles.
Engine testing of the plasma-assisted catalyst is scheduled to begin in 1999, which would enable the technical team to evaluate the effect of the plasma on the particulates in the exhaust. In addition to engine testing, work will continue on the development of enhanced catalyst materials and models to characterize the chemistry during plasma discharge.
Sensors and Controls
The development of sensors to provide data to control systems continues to be a critical aspect of the fuel, combustion, and exhaust-gas after-treatment system. Major breakthroughs are still needed in all four sensor technologies under
development: electrochemical, TSM, ion mobility, and microwave. In the coming year, basic research will continue in these areas, as well as testing of prototype sensors on dynamometers and vehicles. NOx sensor development is also planned.
International Developments
All industrial members of the 4SDI technical team are intimately involved with, and aware of, through their respective companies, the development of CIDI engines in Europe. These companies are competing internationally and participating in the development and marketing of CIDI engines for the European market. According to the 4SDI technical team, Europe and Japan have devoted far more resources to research on CIDI engines than the United States. The committee was not informed of the status of engine development and technical directions in Asia.
Assessment of the Program
The committee believes the 4SDI technical team has correctly identified the major technical challenges facing 4SDI engines for use in HEVs. The CIDI engine has the highest potential for near-term low fuel consumption in a PNGV vehicle. However, the interdependence of often conflicting trade-offs between emissions, fuel economy, and fuel type are major concerns. As regulatory requirements for emissions (NOx and particulate matter) become tighter, unless the fuel is reformulated, it is not likely that the CIDI engine, or any other 4SDI power plant, will be able to meet the PNGV targets for fuel economy and emissions. If the PNGV program waits for alternate technologies to mature sufficiently to meet the PNGV goals, significant midterm gains in fuel economy may not be realized.
Fuel economy should be considered a systems problem. In other words, the engine, fuel formulation, exhaust-gas after-treatment, and controls and sensors must be considered as interdependent system components. A systems approach will require a cooperative effort between the automobile and fuel industries to create a balanced program. Neither industry is likely to invest in a balanced program until a cooperative interchange has been established.
Engines
Continued fundamental investigations of engine combustion will be required to exploit and expand advantageous operating regimes of the combustion engine. Certain operating regimes, for example homogeneous-charge compression-ignition, are known to have good fuel-conversion efficiency and low emissions. However, the range of engine operating conditions in which this mode of combustion can be successfully maintained is limited. A detailed understanding of the
fundamental processes governing this type of combustion may lead to a wider operating range. Similarly, the extent to which the combustion process can be controlled via an advanced, highly controllable fuel-injection system, and resultant emissions, are not well understood. This is an area that could yield large short-term benefits. Finally, with a more complete understanding of the fundamentals, the phenomena that can be measured with sensors could be determined, as well as methods of processing the readings of those sensors into control strategies.
If the PNGV determines that any of the 4SDI engines will not be able to meet the emission targets, new priorities will have to be set. It seems unlikely that alternative power plants, such as fuel cells, will be sufficiently developed in time to meet the PNGV time frame. Therefore, some version of a combustion engine will probably have to be used. If so, the PNGV may have to prioritize the performance and criteria pollutant emission goals. For example, if emission standards are considered non-negotiable, reduced fuel economy would have to be accepted. In that case, the CIDI engine might no longer be considered the most promising power plant for the concept car. At this time, the 4SDI technical team is attempting to identify critical challenges and has not addressed this issue. If this situation does arise, all of the PNGV partners should be actively involved in the prioritization, which will affect the power plant for the concept vehicle and the direction of future research.
Fuel Formulation
The time required to determine new fuel formulations and to change established refining and distribution systems are issues that need to be examined carefully. It is unlikely that a reformulated fuel that requires major infrastructure changes could be implemented in time for the PNGV concept vehicles. Furthermore, the exact composition of an ideal new fuel has not been determined.
To date, experimental investigations of fuel formulations and interactions between the chemical composition of the fuel and CIDI engine combustion and emission characteristics have been very limited. Because of the adverse effect of sulfur on emissions, reducing the sulfur content of fuel to very low levels will be necessary (Tanaka and Takizawa, 1998; Wall and Hoekman, 1984). Cetane number, density, and aromatic content have often been cited as fuel properties that greatly influence exhaust emissions. It is difficult to assess the effects of different fuel properties since they are correlated with one another. However, recent data from a carefully controlled experiment indicated no apparent relationship between exhaust emissions and these fuel properties (Ryan et al., 1998). In another fuel characteristics study, Takatori et al. (1998) observed that a test fuel produced more particulate matter precursors than a base diesel fuel, even though the tested fuel had a lower distillation temperature, fewer aromatics, and lower sulfur content. The test data also suggested that branched and ring structures in the saturated-
hydrocarbons portion of real diesel fuels could produce more particulate emissions than linear alkanes. As these studies show, the optimum characteristics of a new fuel have not been determined. More research will be necessary to resolve these issues for the development of a 4SDI engine system that meets PNGV Goal 3 targets.
Exhaust-Gas After-treatment
A critical component of the fuel-engine-exhaust emission system is the catalytic treatment of the exhaust. The lifetime conversion efficiency of these systems is still not known. Although substantial progress has been made, the PNGV must maintain its efforts if there is to be any possibility of meeting the emissions goals. The exhaust-gas after-treatment systems will also place requirements on the fuel composition, and technical teams working in this area should coordinate their work with work on fuel formulation.
Even with the best catalysts developed by the national laboratories, the NOx-treatment device would still be quite complicated, involving the use of multiple catalysts for operation over a wide temperature window, as well as sensors and control systems for fuel injection into the exhaust gas. These catalysts also produce a substantial amount of nitrous oxide (N2O) as a product (Acke et al., 1998; Lee and Kung, 1998). Further catalyst development is needed to lower the nitrous oxide production because of its high global-warming potential. 4
Particulate matter emissions can be reduced with exhaust-treatment technology through a combination of an oxidation catalyst and particulate trap. This approach has received less attention recently because engine controls plus an oxidation catalyst and some sulfur reduction in diesel fuel have been highly effective in reducing the particulate emissions of CIDI engines, and additional improvements are possible. However, the proposed particulate standards could not be met with engine controls and short-term fuels improvements, so particulate-trap technology should be reexamined.
The committee urges PNGV management to determine whether sufficient effort is going into the development of control technologies for particulate emissions from CIDI engines. If not, the program plan should be modified accordingly. The interactions and trade-offs among particulate-control technology, NOx-control technology, fuel requirements, fuel economy, and cost must be continued.
Recommendations
Recommendation. The 4SDI team should continue its program plan but should provide a more quantitative means of assessing progress and technical status relative to targets. In particular, the program should focus on exhaust-gas after-treatment and the development of performance or fuel specifications for a clean diesel fuel.
Recommendation. The 4SDI technical team should develop projections of the performance of compression-ignition direct-injection and gasoline direct-injection power-train systems, especially comparisons of the estimated emissions and fuel economy for each system. These projections would be a first step toward the quantification of trade-offs between emissions and fuel economy based on current and emerging state-of-the-art technologies.
Recommendation. Because one of the objectives of the PNGV program is to develop a vehicle that will be competitive in a global market and because fuel economy is a stronger market force in Europe and Asia than in the United States, the PNGV should continue development of the compression-ignition direct-injection engine.
Fuel Cells
Fuel cells are considered the probable long-term replacement for internal-combustion engines in automobiles and other transportation systems. Indeed, this perception is growing as more people and organizations learn of the potential for massive reductions in emissions and, depending on fueling system implementation, significant increases in thermal efficiencies compared to internal-combustion engines. Undoubtedly, the PNGV's activities have contributed to this perception and have stimulated many fuel-cell programs both nationally and internationally.
All of the evidence available to the committee continues to indicate that fuel cells have the potential for emission and efficiency gains. However, many important technical issues must still be resolved, including bringing down the high cost. Most of the unresolved technical issues are related to the use of liquid hydrocarbon fuel on board the vehicle, especially problems associated with gasoline as the onboard fuel.
The use of a liquid fuel entails a fuel processor.5 A fuel processor is not an "instant-on" device but requires time to reach the internal temperatures necessary to reform liquid fuel into a hydrogen-rich gas. Reaching the reformation temperatures requires considerable heat, which is provided by burning some of the fuel,
either in an external burner (e.g., steam reformer) or an internal burner (e.g., partial-oxidation [POX] or autothermal reformer). In either case, unburned hydrocarbons and CO are produced, which could be released to the atmosphere. The start-up delay caused by the fuel processor warm-up time is a major reason for considering a hybrid vehicle with a reserve of stored energy (e.g., a battery) and enough available power to drive the vehicle until fuel-cell power is available. Other reasons for a hybrid vehicle are for fast power response (also related to transient response of the fuel processor) and to provide a reservoir for recovering part of the braking energy through regeneration (which is not related to the characteristics of a fuel processor).
In terms of fast start-up, fast response time, essentially zero emissions, high system efficiency, and the least complex energy converter, the preferred fuel is gaseous hydrogen. However, because of its very low density, it is very difficult to store enough hydrogen gas onboard the vehicle to travel more than about 100 miles. Other problems include the lack of infrastructure for widespread distribution, high cost (two to three times the cost of gasoline on an energy basis), and problems with refueling and indoor storage.
The most likely candidates of the liquid-hydrocarbon fuels are methanol and gasoline. Methanol can be reformed at a much lower temperature than gasoline (about 400°C vs about 700°C for gasoline) and has a hydrogen/carbon ratio about double that of gasoline. But, like hydrogen, methanol fuel has virtually no infrastructure for distribution. Thus, gasoline (probably reformulated to lower vapor pressure and with some sulfur removed) is the PNGV's fuel of choice, at least in the near term. The methanol industry, however, appears to be highly motivated to develop both production and infrastructure capabilities. Potential environmental and health impacts of methanol are well known and are being addressed by potential methanol suppliers and relevant government agencies.
Gasoline is a rational choice at this time because no vehicle could be attractive to the general public without the widespread availability of fuel at a competitive price. Even so, the choice of gasoline aggravates the technical (and cost) problems of the development of an acceptable fuel-cell power train for the PNGV program. In fact, most of the PNGV's funding and efforts in the past year have been focused on the development of fuel processors. This situation is not expected to change in 1999. The PNGV's efforts have been aimed primarily at making the processor smaller, lighter, cheaper, faster responding, more efficient, and capable of producing lower concentrations of CO (which dramatically reduces fuel-cell stack performance). At the same time, parallel efforts are under way to make fuel-cell stacks more tolerant to the CO being produced by the POX gasoline reformers. The hope is that these simultaneous efforts to reduce the production of CO by the fuel processor/cleanup system and to increase the tolerance of the fuel-cell stack to CO will converge on workable system components. In view of the difficulties associated with the development of a gasoline system, the PNGV should rethink its overall rationale for fuel selection.
As design and analysis continue, it has become evident that there is a big difference between fuel-cell components that perform satisfactorily and a fuel-cell system that performs satisfactorily. Obviously, most of the PNGV's efforts to date have focused on components and subsystems. However, the committee believes that system integration and control problems will also present formidable challenges. Until very recently, however, systems issues have received little attention. This was partly a reflection of the emphasis on the development of components, but partly also a result of the delayed development of (still unverified) system simulation tools. A fuel-cell system model has reportedly now been developed and transferred to the systems analysis team and developers, and validation of the model with data from a 10-kW integrated fuel-cell system is planned.
Besides the lack of system simulations, there is still a need for experimental data for a gasoline fuel-cell system. A breadboard gasoline reformer was tested, as well as cleanup components for the reformate gas produced by the reformer that then enters the proton-exchange-membrane (PEM) fuel-cell stack. However, these components did not create a complete system, and only minimal operational capability was demonstrated for the processor and stack. Even though impressive accomplishments have been made, the committee concluded that additional progress will be necessary, even essential, for the development of a successful gasoline fuel-cell energy converter.
Program Status and Progress
Milestone Schedule
Based on a presentation to the committee in October 1998, the fuel-cell concept vehicle is expected to be several years behind the original PNGV schedule. A fuel-flexible6 concept car could possibly be ready by about 2003 or 2004 (Milliken, 1998). However, comments to the press by automotive company executives have suggested that fuel cells will be available for production at an earlier date. Several completed and planned events are directed at achieving a fuel-cell system for a concept vehicle. The following activities have been completed:
- In 1997, AD Little (ADL) demonstrated a 1-kW gasoline fuel processor with a PEM stack.
- In 1997, Ford/International Fuel Cells (IFC) demonstrated a 50-kW PEM stack with hydrogen.
- In 1998, GM demonstrated a brass-board methanol 30-kW fuel processor with PEM stack and system.
Activities in progress or about to be started include the following:
- PlugPower will demonstrate integration of a 10-kW fuel-flexible fuel processor with a PEM stack.
- PlugPower will demonstrate a 30-kW hydrogen-fueled PEM stack.
- In 1999, IFC and PlugPower plan to demonstrate a 50-kW fuel-flexible fuel processor with a PEM stack.
The completed activities have already led to the demonstration of a methanol ''mobile platform," and a hydrogen "mobile platform" will be announced soon. These are expected to lead to a "fuel-flexible mobile platform" by about 2002. The subsequent development of a 50-kW fuel-flexible fuel processor integrated with a PEM fuel-cell system by about 2003 could lead to a fuel-flexible concept car by about 2004. The milestone schedule projected by PNGV seems ambitious but possible. Significant progress was made in 1998 in virtually all areas, including stacks, components, fuel processing, system modeling, and overall system integration (for a methanol system).
Stacks and Other Components
A compression-molded carbon-composite bipolar separator plate, which is an important component for fuel-cell stacks, was demonstrated in 1998 by the Institute for Gas Technology (IGT). This plate had a materials cost of only $4/kW, which, combined with a conceptual design for mass production, is expected to meet the cost goal of $10/kW. The performance of the plate met or exceeded the performance of machined graphite plates.
In the past year, impressive improvements were made in anode tolerance to CO. Tests were conducted at LANL with up to 100 ppm of CO in reformate with no apparent performance penalty compared to reformate with no CO. However, an anode-platinum loading of 0.6 mg/cm2 and 4 percent air injection were required, and durability has not been tested. This concept is expected to be incorporated into PlugPower stacks for testing in 1999.
The 3M Company tested prototypes of high-volume, potentially lower-cost membrane-electrode assemblies (MEAs), which could dramatically reduce costs. Although excellent performance was demonstrated with low platinum loadings (0.1 mg/cm2), the data were only for hydrogen/oxygen. The performance for reformate/air has not been determined.
Fuel Processors
A catalyzed POX reformer was designed and tested at ANL. The tests were performed with standard gasoline and produced a start-up time (based on 30 percent H2 concentration compared to a theoretical maximum of 40 percent)
of less than four minutes. Although this time is still longer than the 30-second start-up target, it is much shorter than the tens of minutes that had been required.
LANL has designed and tested a 50-kW modular preferential-oxidation (PrOx) fuel processor that, through three stages, reduced CO from 8,000 ppm to 30 ppm. However, the cleanup target was 10 ppm, and approximately 4 percent of the hydrogen was also consumed in the oxidation process.
PNNL continues to work on microchannel heat exchangers with the development of a 50-kW gasoline vaporizer. The vaporizer volume is only about 300 cm3, which is about 10 percent the size of a conventional vaporizer of the same capacity. Preliminary tests show a low pressure drop (about 3.5 psi at rated flow) and no noticeable performance degradation due to "fouling." This technology could be extremely important for reducing the size and weight (and even the cost) of components of heat exchangers.
Systems
GM has built and operated a 30-kW methanol brass-board system using a GM methanol steam reformer and a Ballard PEM stack. The system includes sensors and controls that allow automatic operation and generally available automotive components. Steady-state emissions were essentially undetectable, although start-up and transient emissions were not measured. The peak system efficiency was considerably lower than predicted (30 percent compared to 38 percent), and peak power was 25 kW, as compared to the expected 30 kW. The performance loss was attributed to the CO cleanup system.
ANL has completed the development of a computer model of a fuel-cell system, which has been transferred to systems-analysis teams and fuel-cell developers. The model has not yet been verified with experimental system results.
Clearly, impressive technical progress has been made in the past year. However, the results also show that much more remains to be done. For example, in the systems area, a steam-reformed methanol brass-board system should be considerably less difficult to integrate and control than a gasoline system utilizing POX and subsequent "cleanup." Even so, the methanol systems did not meet performance goals, and no start-up or transient data are available. Parallel efforts to increase CO tolerance of the stack and decrease the CO output from the fuel-processor/cleanup system have been successful but at a high cost in terms of other important parameters, such as size, catalyst loading, and fuel consumption.
Attempts so far to develop turbomachinery to provide the PEM pressurization with acceptable size, cost, and performance have been partially successful, but none of the designs comes close to meeting all of the goals. However, efforts are continuing to improve nonpressurized systems. At this point, it is not clear if a pressurized system would have advantages in terms of overall system cost and performance over a nonpressurized system.
Costs
Significant cost reductions seem to be within reach in several areas, such as MEAs and molded separator plates. In areas such as the air pressurization system and fuel processing, however, costs are still very high. The most recent study by Ford/Directed Technologies, Inc. (DTI), projected costs based on "known but not implemented" processes at $77/kW. This projection is very encouraging compared to the $500/kW estimated by the PNGV during the committee's fourth review and compared to the target of $50/kW for a 2004 concept vehicle (NRC, 1998a). The methods and assumptions used by Ford/DTI were not disclosed but were reported to be "rigorous" and "detailed.''
International Developments
Both Europe and Japan are continuing to make substantial efforts to develop fuel-cell technology and fuel-cell-powered vehicles. Ballard Power Systems, Inc., of Canada and their activities with joint venture partners, DaimlerChrysler and Ford, still represent the most visible efforts to commercialize stacks, fuel-cell energy converters, and electric drive components for vehicles. The companies have indicated production volumes of fuel-cell systems of thousands by 2002, 40,000 by 2004, and 100,000 by 2006. Ballard has also entered into a joint venture with GEC Alsthom to supply fuel cells for stationary applications in Europe and Canada. Ballard continues to supply stacks for the majority of both U.S. and foreign fuel-cell vehicle programs. The company has also supplied three hydrogen-fueled buses to Chicago and several to Vancouver, as well as one methanol-fueled 40-ft bus to Georgetown University (in Washington, D.C.).
In August 1998, United Technologies Corporation (UTC) formed a limited liability company, IFC, LLC, to expand its fuel-cell business in the transportation market. Toshiba Corporation and UTC are equity investors in IFC, LLC.
DaimlerChrysler is continuing to develop the A-car class methanol-fueled NECAR IV and is apparently developing a hydrogen-fueled version of this vehicle for demonstration and testing. Toyota now has a new methanol-fueled vehicle in addition to its earlier hydrogen-fueled vehicle.
Progress and Status
Clearly, major obstacles must still be overcome before the PNGV can reach essential targets to realize a practical automotive fuel-cell system. However, in the committee's opinion two very positive developments have taken place in the past year. Impressive progress has been made, and PNGV seems to have been very responsive to the committee's recommendations in its fourth report (NRC, 1998a).
In the critical area of fuel-processor development, a steady-state POX gasoline reformer/CO cleanup system (at ANL) has shown good results with low CO
and more than 35 percent hydrogen yield. With the development of a 50-kW PrOx (at LANL), the first meaningful transient measurements have been made. Plans presented to the committee for 1999 include the integration of a 50-kW (by Epyx) POX reformer with a two-minute start-up time with IFC and PlugPower components and the demonstration of a bench-scale microchannel steam reformer for iso-octane by PNNL. Other significant activities are planned in design, scaleup, and expanded tests by ANL, LANL, Hydrogen Burner Technology (HBT), and others.
In stack development, important cost reductions have been identified with the composite bipolar plates (by IGT) and continuous manufacturing of MEAs (by 3M). The tolerance to CO was increased to 100 ppm (by LANL), although at a significant cost in catalyst loading and hydrogen consumption. Notable events planned for 1999 include the development and testing of four reformate-capable stacks (by IFC, PlugPower, Energy Partners, and AlliedSignal) and the continuation of the stack development programs mentioned above.
In the systems integration area, a baseline design has been completed for a gasoline system (by IFC, PlugPower, and Epyx), and the committee was told that a significantly improved systems-analysis model has been developed (by ANL) and transferred to users. The testing of the "integrated" 10-kW fuel processor and stack (by PlugPower and Epyx) was done in 1998 and subsequent tests are planned for 1999. Other plans for 1999 include the integration of the fuel-flexible processor and 50-kW stack (by IFC, PlugPower, and Epyx) and continued development of the system model (by ANL).
Major problems and uncertainties remain in the areas: (1) the air compressor/turbine still must overcome challenges with regard to performance, size, and cost; (2) the fuel processor/CO cleanup development is still in the laboratory/brass-board stage; (3) stack tolerance to CO and other impurities is still an issue; and (4) system integration remains a challenge because there is no working gasoline system, and the systems model is as yet unverified and limited. Furthermore, almost no long-term durability tests for major components have been performed or planned, and only a few high-volume manufacturing processes have been identified.
In summary, the committee commends the PNGV for making impressive progress in critical areas, as well as for responding positively to the committee's recommendations. Nevertheless, a long list of identified deficiencies (and many not yet identified) remain to be resolved. The potential benefits of automotive fuel-cell systems, however, are sufficiently high to justify the PNGV's continued efforts in this area.
Recommendations
Recommendation. PNGV should re-examine its fuels selection for fuel cells, taking into account the anticipated technical difficulties and cost implications of using gasoline as the onboard fuel.
Recommendation. PNGV should focus on improving stack performance without the use of a multi-atmosphere pressurization system.
Recommendation. PNGV should evaluate and compare reasonably optimized fuel-processor systems for different fuels to determine if the fuel-flexible or multifuel processing systems would be cost effective and would provide acceptable performance compared to systems optimized for a single fuel.
Electrochemical Energy Storage
Introduction
To reach the fuel-efficiency goals of up to three times the value prevailing for midsized passenger vehicles in 1993, an energy-storage subsystem will be necessary to provide load leveling for the primary power plant and to store energy recovered through regenerative braking. Load leveling in an internal-combustion engine can reduce the size and mass of the engine, improve the average thermal-energy efficiency, and permit better emissions control. It can also improve fuel economy by recovering some braking energy. Energy-storage technology can provide similar advantages of size reduction, thermal-energy efficiency, and regenerative braking if applied to vehicles using fuel cells and reformers, which have cold-start and transient-response limitations. With sufficient energy storage, an HEV can operate at a meaningful range on battery power alone, with zero emissions emitted directly by the vehicle.
PNGV is no longer focusing on ultracapacitors and pseudocapacitors, which are better suited for applications with discharge times substantially shorter than 18 s. They are also costly and have low specific energy. The PNGV has currently discontinued development of flywheels for energy storage on the vehicle, largely because of safety concerns. As a consequence, batteries designed for high specific power are now the most likely means of energy storage. Of these, lithium-ion batteries, which have high efficiency and high specific energy, have become the preferred technology in the long term but may not be available by 2000. The nickel metal hydride battery, which presents less of a challenge for control and safety, could be available by 2000.
Table 2-2 shows the targets for energy storage, as well as the status of lithium-ion and nickel metal hydride battery systems with respect to some targets. Results are generally for cells rather than for complete battery subsystems. The power-assist HEV configuration provides partial load leveling and recovery of braking energy for a fast-response engine like a CIDI in a parallel-hybrid configuration. The dual-mode HEV configuration involves more extensive load leveling, such as a fuel cell in a series configuration.
"Available energy" is defined as energy that can be delivered within the state-of-charge (SOC) range where discharge and regenerative pulse-power
TABLE 2-2 Design Targets and Present Performance for Short-Term Energy Storage
|
PNGV Targets |
|
1998 Performance |
|
|
Power Assist |
Dual Mode |
Li-ion |
NiMH |
Pulse discharge (constant for 18 s) |
25kW |
65kW |
|
|
Maximum regenerative pulse power (at start of a 10 s trapezoidal pulse) |
30kW |
40kWa |
|
|
Available energy |
0.3kWh |
3kWh |
|
|
Energy efficiencyb |
(90% |
(95% |
93% |
77% |
Cycle life at ΔSOC = 1.5% |
200k cycles |
200k cycles |
|
|
at ΔSOC = 3% |
120k cycles |
120k cycles |
|
|
Calendar life |
10yrs |
10yrs |
2.5yrsc |
5yrs |
Maximum mass |
40kg |
65kg |
|
|
Maximum volume |
32L |
40L |
|
|
Production costs @ 100k/yr |
$300 |
$500 |
|
|
Operating temperature range |
-40° to 52°C |
-40° to 52°C |
|
|
Available specific energy |
12Wh/kg |
83Wh/kg |
38Wh/kg |
12Wh/kg |
Available energy density |
24Wh/L |
188Wh/L |
82Wh/L |
36Wh/L |
Specific power (18 s discharge) |
960W/kg |
1,800W/kg |
960W/kg |
290W/kg |
Cost per rated energy |
$833/kWh |
$134/kWh |
$450/kWh |
$1400/kWh |
a Revised downward from 70 kW. b The corresponding electric vehicle target is 75%. c Based on higher temperature accelerated testing. Acronyms: kWh = kilowatt hour; Wh = watt hour; SOC = state of charge. Source: Haskins (1998). |
targets can both be met. The available energy is always less than the "rated energy," which is defined here as the energy delivered at the one-hour discharge rate. These are both larger than the discharge energy delivered in a specified one-minute cycle designed to approximate urban driving conditions. (For example, acceleration of a 1,000-kg vehicle to 100 km/h requires 0.1 kWh for kinetic energy alone.)
The performance and cost targets for the battery are substantially more difficult for the dual-mode HEV configuration and they may preclude any series hybrid vehicle (as for a fuel cell) if there is strict adherence to the stated targets. Full hybridization, which has system limits on mass, volume, and cost, would create severe, perhaps impossible, requirements for the dual-mode hybrid, thereby eliminating an important option for trade-offs of performance, emissions, and cost from the PNGV's strategy.
The performance results shown in Table 2-2 correspond to batteries of a particular design, usually associated with the power assist. Better results, including lower cost per rated energy and higher rated specific energy, can be expected from a battery developed explicitly for applications with the same 18 s power pulse as the battery for power assist and larger capacity. The performance results presented to the committee show that results vary substantially among battery developers.
Status and Progress
Accomplishments
Cell and module development have continued apace. The vast majority of resources is devoted to battery development, fabrication, and testing. At present, three developers are working on lithium-ion batteries. SAFT has built and tested 13-Ah cells and has developed a 50-V module. PolyStor has achieved 1,920 W/kg and 100 Wh (rated)/kg in cells of about 1 Ali and 800 W/kg and 100 Wh(rated)/kg in 10-Ah cells. VARTA has achieved 1,500 W/kg and 99 Wh/kg in very small cells and is working on 6-Ah cells. Energy and power goals thus appear to be attainable, but in all cases achievement of the goals for cycle life and calendar life is questionable for lithium-ion technology. VARTA, the sole developer for nickel metal hydride batteries, has achieved 400 W/kg and 30 Wh/kg in 10-Ah cells. VARTA has also delivered a 40-cell nickel metal hydride module for testing.
Programs for 50-V module demonstrations have been initiated at PolyStor ($9.5 million for 21 months beginning March 1998) and VARTA ($8.3 million for 24 months beginning March 1998). These studies are being funded in the usual way with PNGV and the developer sharing costs.
Abuse and safety testing of advanced batteries also continues. The lithium-ion technology uses organic materials that can burn, and fire and smoke have been observed in some abuse tests. The nickel metal hydride system, which uses an aqueous electrolyte, avoids many of these problems.
Mass, volume, and cost goals from the battery subsystem have been allocated to the cell and module levels during the design and development of these components. Such allocations could be made for the power-assist mode but not for the dual mode. Furthermore, the cycle-life targets for cells and modules have not been specified.
During the past year, the PNGV identified a mismatch between the goals for power assist and the dual-mode hybrid-vehicle configuration (see Table 2-2). A battery technology that just meets the power-assist targets will be too high by factors of 5.7, 5.3, and 8 on the dual-mode cost, weight, and volume targets, respectively. For example, the power-assist mode allows 32/0.3 = 107 L/kWh, whereas the dual model permits only 40/3 = 13.3 L/kWh. This means that a battery system that just meets the former target would miss the latter by a factor
of 8. The other ratios are more complicated by considerations of breakdown to module and cell levels but are similar in concept. Put another way, much higher values of specific available energy and specific rated energy would be required, values that are unlikely to be met by the candidate technologies. The PNGV has not revised the targets to resolve this discrepancy.
The PNGV now recognizes that innovations, perhaps even innovations in cell chemistry, will be necessary to achieve abuse tolerance, calendar or cycle life, and cost targets. For example, meeting the calendar-life target will require innovations in the basic lithium-ion electrochemistry. PNGV plans to mobilize the national laboratories in a new way to address these problems, avoiding proprietary issues by having them explore and refine a generic baseline chemistry, including improvements in intrinsic chemical stability.
High-power batteries require thinner electrodes than the lower power batteries used for electric vehicles. Therefore, manufacturing techniques will have to be improved. Unresolved issues for both hybrid and electric vehicle batteries include control, thermal stability, and cell stress levels in series strings of cells.
Assessment of the Battery Program
Meeting the PNGV targets, especially for calendar life and cycle life, but also for specific energy and cost, is in serious jeopardy. Consequently, PNGV is enlisting the help of national laboratories to define a generic (nonproprietary) baseline chemistry and to show, by example, how to elucidate the failure mechanisms of a system. Developing new electrochemistry is equivalent to starting over in this area.
Even though lithium-ion batteries may be preferred for the long term (2004) because of their higher efficiency and specific energy, nickel metal hydride batteries should be made available (and perhaps even advanced lead-acid, nickel-cadmium, or nickel-zinc batteries) for year-2000 vehicles.
The PNGV should seriously consider the consequences for vehicle goals if the battery targets cannot be met. A suitable model of the unit cell would permit trade-offs of battery size, performance, and cost against vehicle characteristics. For a specified battery type, say lithium-ion or nickel metal hydride, the battery could be sized to provide the required power and energy over a specified time profile, with iteration between the battery model and the vehicle model. Without these trade-offs, a fuel-cell powered, series hybrid vehicle may have to be precluded. If the interactions among partial hybridization and the size, fuel efficiency, transient response, and emissions of the primary power plant are well understood, the disparity between targets for power-assist and dual-mode hybrid vehicles could be eliminated.
Despite these problems, a battery remains the most promising technology for energy storage in hybrid vehicles. Hybrids are being developed, and have been demonstrated, outside the program with batteries that fall far short of the very
aggressive PNGV performance and cost targets. At 0.3, or even at 3 kWh, energy storage is not a dominant subsystem with respect to weight, volume, or cost, and some relaxation of the targets should be possible.
Major challenges of PNGV's battery program are still calendar-life and cycle-life targets and safe abuse tolerance under representative operating conditions, as well as low cost. The PNGV needs to put these issues into perspective by (1) developing a better understanding of the factors that control calendar life and cycle life, (2) conducting more realistic simulations of abuse conditions and their effects, and (3) developing a better understanding of the factors that control battery costs in mass manufacturing. Combined with a more transparent relationship between hybrid-power-train performance and battery-performance targets, PNGV could then determine if the emerging battery technologies could meet redefined targets and goals. PNGV should make this determination before making decisions that will have major consequences for the program's schedule and prospects of success (e.g., the development of alternative battery electrochemistries).
In summary, if energy-storage performance goals are relaxed and redefined, the hybrid concept could be implemented and tested even though the batteries currently under development are unlikely to meet the present targets. The program is and will remain dominated by battery development and testing, but the performance goals and cost estimates could use some reevaluation. The PNGV is well aware of the problems related to cycle and calendar life and safety, and the committee does not feel compelled to make recommendations to address these issues. The committee is not calling for a drastic reorientation of the program because the development of high-risk systems, like lithium-ion and nickel metal hydride batteries, is appropriate for the PNGV, and more conventional batteries provide suitable fallback positions. Failure to meet goals may reflect the inappropriateness of the goals rather than the impending failure of the entire project.
International Developments
The development of high-power batteries for the PNGV program is based on the work of European developers (e.g., SAFT and VARTA). The PNGV reported little to the committee on developments in Japan, where lithium-ion technology is more advanced and is already being used in HEVs.
Recommendations
Recommendation. The PNGV should update its energy-storage requirements and goals by means of subsystem models integrated with overall system analysis. In addition to specific energy, test results should be reported for energy efficiency and specific power over well defined test protocols and compared to the refined performance goals.
Recommendation. The PNGV should decide whether safety issues with lithium-ion batteries will preclude their introduction for energy storage in hybrid electric vehicles.
Recommendation. The PNGV should conduct life-cost and performance-cost trade-off studies, as well as materials and manufacturing cost analyses, to determine which battery technology has the best prospects and most attractive compromises for meeting capital and life-cycle cost targets.
Flywheels
A flywheel energy-storage subsystem on board an automobile has been defined as a relatively low-energy device (i.e., with 30 kW of power and 300 Wh of energy storage) suitable for application to fast-response power plants. A fast-response power plant, which has a similar response time to a conventional automotive engine, places a much lower requirement on power output of the flywheel than a slow-response power plant. The higher energy demands of slow-response power plants would require a large, more costly subsystem, and the flywheel has, therefore, been judged to have possible application to the less demanding power-assist HEV mode. Because of the issues of cost and weight, as well as testing to demonstrate a safety design that would contain the flywheel in case of failure, the PNGV does not consider this technology to be available for the 2000 concept vehicles, although it may still be useful for post-2000 concept-vehicle systems. Currently, the PNGV has discontinued the development of flywheels. Realizing applications of flywheel subsystems would depend on whether the vehicle system modeling indicated that cost and performance would be acceptable.
Status
In the past year, only limited systems-analysis modeling has been conducted. Design approaches for flywheel safety and failure containment have been proposed, but very limited validation testing has been done. Until test results are available and the cost of associated electronics is understood better, the PNGV does not plan to develop further systems modeling. DOE is maintaining contact with, and monitoring activities within, the flywheel technical community although no funds have been allocated for fiscal year 1999 for flywheel development. The PNGV is monitoring the progress of two flywheel programs, the joint Aerospace Flywheel Program (a cooperative project of the Air Force and the Defense Advanced Research Projects Agency, and the National Aeronautics and Space Administration) and the Defense Advanced Research Projects Agency Flywheel Safety and Containment Program.
Plans
In anticipation of future systems modeling, LLNL is developing a second-generation flywheel model to be included in the PNGV vehicle-systems model. LLNL is procuring a flywheel from the Trinity Battery Company and has an agreement with the University of California, Davis, for installation and testing on an HEV; the university is seeking financial support from the California Energy Commission.
Recommendation
Recommendation. Because limited progress is expected on the flywheel device, the PNGV considers it a post-2000 technology. Given that no money has been allocated for flywheel development in PNGV's fiscal year 1999 budget, the PNGV should follow through on monitoring developments in other flywheel programs.
Power Electronics and Electrical Systems
The three USCAR partners are pursuing two design philosophies for the HEV. One is the dual-mode hybrid, in which primary propulsion can be provided by either the electrical or internal-combustion engine drive system; the other is the power-assist HEV (sometimes referred to as the "lite" hybrid), in which an electrical drive augments primary internal-combustion engine propulsion power during acceleration and provides the vehicle with electric power for moving from standstill. In either case, success depends on the development of efficient, economic actuators, motors, and power electronic converters.
Status and Progress
The electrical and electronic systems technical team (EE technical team) has made impressive progress over the last year. The team's program is now well organized and managed. Projects at the national laboratories by DOE's Cooperative Automotive Research for Advanced Technologies (CARAT) program and by the Small Business Innovative Research (SBIR) program have been integrated into a coordinated program to address technical objectives. Now that the automotive integrated power module (AIPM) has been specified, results of the Navy's power electronic building block program can be directed toward meeting the unique requirements of the PNGV, a concern raised in the committee's fourth report (NRC, 1998a). PNGV noted that: "The AIPM is intended to be flexible and scalable to meet a large number of applications in advanced vehicles. System integration issues include delivery of complete scale modules incorporating the principles of design for manufacturability and means to update DOE existing cost analyses" (Malcolm, 1998).
An electric motor/gearbox specification has been drafted in collaboration with the systems-analysis team, and it was reported to the committee that a request for proposals (RFP) for its design and construction was planned for early 1999. The committee is pleased to see that the EE technical team has been collaborating with the systems-analysis team, as recommended in the committee's fourth report.
During the last year, the EE technical team has either initiated or redirected a large number of industrial and national laboratory activities to address the important issues of high-performance/low-cost materials, new manufacturing technologies, system integration, and standardization. These efforts can be broadly categorized as AIPM development, electric-motor development, and the integration of the AIPM with the motor. A number of national laboratory projects are directed at developing new dielectric materials and dielectric-deposition processes for the manufacture of capacitors, which are expensive and environmentally sensitive components in power-electronic systems. New thermal-management materials, such as carbon foam, are also being investigated for possible application in power-electronic systems.
Assessment of the Program
In its fourth report, the committee expressed concern about the PNGV's prospects for meeting its cost targets for power electronics and motors. The EE technical team has verified the presently achievable cost of $15/kW (peak) for power electronics through modeling done separately by each USCAR partner. The 2004 target of $7/kW (peak), a reduction of more than 50 percent from today's calculated but unvalidated cost, will require substantial innovations in component and manufacturing technologies. Although some of the technology development programs in the national laboratories (e.g., nanostructure multilayer capacitors) look promising, their projected costs are still uncertain.
Based on an analysis using DOE's cost models, the EE technical team believes the 2004 target to be realistic. The analysis necessarily relies on the assumption of innovative developments in component and manufacturing technologies, although these have not been identified. The DOE cost model does an excellent job of analyzing historical cost data for power-electronic converters in different power categories and breaking the cost down by component and process. However, although the EE technical team has done an excellent job of identifying cost obstacles and initiating or redirecting development programs to overcome them, the cost projections to the year 2004 seem to be simple extrapolations. This issue is critical because it affects the economics of other vehicle systems that rely on power electronics (e.g., fuel cells and accessory drives).
The committee is concerned about the limited response to the RFP for development of the AIPM, which may reflect an industry opinion that achieving the AIPM specifications is not feasible. However, the small response may also reflect
a concern that there is no near-term market at present for the AIPM or that potential respondents are already working with an automotive manufacturer on proprietary power-electronic developments.
Because the RFP for the motor/gearbox was just issued, industry's response is not yet known. However, the committee expressed its concern last year that the target motor cost of $4/kW might be unrealistic in light of the fact that today's cost of $10/kW is essentially the cost of materials. The projected increase in power density, from 4 kW/l to 5 kW/l, does not represent a sufficient reduction in materials to account for the desired decrease in cost.
Three small subgroups of the committee visited the three USCAR partners and were provided with proprietary presentations of prototype vehicles. In two of the three vehicles, the electrical system and drive designs were elegant and well conceived, which was reflected in vehicle performance. Functionality of the power electronics and electrical system is not an issue in these vehicles.
Although the development of electrical accessories was not explicitly addressed during this review, the committee notes that several of the development programs under the EE technical team's umbrella are focused on accessories. The compressor motor for the air conditioner and an electrical turbocharger assist are two examples.
Recommendations
Recommendation. The PNGV should review its power-electronics and motor cost targets for 2004 to determine if they are realistic based on known and projected technology. Because of the reliance of other vehicle systems on power electronics, the PNGV must have a high level of confidence that its cost projections can be met.
Recommendation. The PNGV should conduct a thorough analysis of the electrical-accessory loads to ensure that targets for supplies of electrical energy are consistent with system needs.
Structural Materials
The reduction of vehicle mass through improved design, lightweight materials, and new manufacturing techniques is one of the key strategic approaches toward meeting the PNGV Goal 3 fuel economy target.7 Figure 2-2 shows the design space for trade-offs between power-train efficiency and vehicle-mass reduction. To achieve the 80 mpg target of Goal 3, however, additional measures,
7 |
This section focuses on PNGV progress on structural materials. The issue of vehicle crashworthiness is addressed in Chapter 4. |
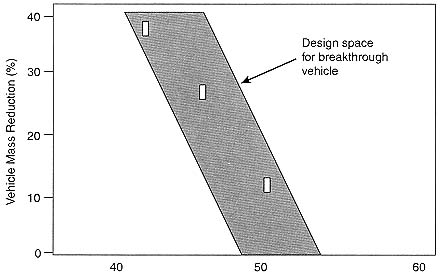
Figure 2-2
PNGV design space.
SOURCE: PNGV (1998).
such as regenerative braking with 70 percent efficiency, improved driveline efficiency, and reduced aerodynamic drag, will be necessary. According to the systems analyses on which the results in Figure 2-2 are based, a 50 percent reduction in the weight of the baseline vehicle is equivalent to improving the power-train thermal efficiency by about 9.4 percent above the baseline value (about 18.2 percent for the urban-highway cycle). After considering the options, the PNGV decided to adopt the following targets: 40 percent mass reduction, 40 percent power-train thermal efficiency, and a regenerative braking system with 70 percent efficiency. These must be achieved while the baseline vehicle performance, size, utility, and cost of ownership are maintained.
The PNGV has set substantial vehicle weight-reduction targets for various subsystems (Table 2-3). These targets will result in an overall reduction in curb weight of 1,200 lbs (40 percent), leading to a 2,000-lb vehicle.
Materials Road Map
The PNGV materials team has developed a road map that identifies lightweight material alternatives for the major subsystems of the vehicle. Alternative materials are prioritized based on their weight-saving potential and feasibility to meet the PNGV time requirements. Technical challenges are also identified and
Table 2-3 Weight-Reduction Targets for the Goal 3 Vehicle
Subsystem |
Current Vehicle (lbs) |
PNGV Vehicle Target (lbs) |
Mass Reduction (%) |
Body |
1,134 |
566 |
50 |
Chassis |
1,101 |
550 |
50 |
Power train |
868 |
781 |
10 |
Fuel/other |
137 |
63 |
55 |
Curb weight |
3,240 |
1,960 |
40 |
Source: Stuef (1997). |
prioritized by the likelihood that solutions can be found to overcome the challenges. The road map is summarized in Table 2-4. The absolute magnitude of the weight-saving potential depends not only on the density and structural properties but also on where the use of these materials is suitable.
The committee was pleased to see that 38 projects have been established to address the technical challenges identified in the materials road map. In addition, the R&D portfolio is supported by 13 manufacturing technical-team projects and five supplier projects. The committee believes that these projects have the potential to overcome the barriers that have made it difficult to use alternate materials in today's vehicles. The committee recognizes that many of these programs have just been initiated and that, therefore, there is little progress to report at this time. The committee has suggested that the materials technical team use the U.S. Automotive Materials Partnership (USAMP) project tracking system as a means of reporting progress to the committee on an annual basis.
The requirement that there be no increase in the overall cost of vehicle ownership presents an obvious hurdle to meeting the PNGV's fuel economy goal. This is shown clearly in Table 2-4, where the reduction in the cost of feedstock is a common challenge for all alternate materials. The committee is pleased to note that PNGV personnel are working closely with materials suppliers to develop less costly manufacturing processes and new design practices that utilize materials more efficiently.
Status and Progress
The major material alternatives under consideration in 1998 for reducing vehicle weight are discussed below in terms of the primary vehicle subsystems: body, chassis, and power train. These subsystems account for 96 percent of the weight of the Goal 3 baseline vehicle (Table 2-3). For each subsystem, there are several competing alternative materials. The weight savings quoted for various
TABLE 2-4 Materials Road Map: Weight-Savings Potential and Technical Challenges
Materialsa |
Weight-Savings Potential (lbs) |
Primary Subsystem |
Primary Challenge |
Aluminum |
600 |
body |
feedstock cost |
Magnesium |
150 |
chassis/body power train |
feedstock cost |
Polymer composite (GFRP) components |
150 |
body |
high-volume manufacturing |
Polymer composite BIW (CFRP) |
500 |
body |
low-cost carbon fiber |
Steel |
>120 |
body |
design manufacturing concepts |
Metal matrix composites |
30–50 |
chassis and power train |
feedstock cost |
Titanium |
50 |
chassis and power train |
feedstock cost |
Glazing materials |
50 |
body |
safety regulations and cost |
a Materials are listed in decreasing priority. Acronyms: GFRP = glass fiber-reinforced polymer; CFRP = carbon fiber-reinforced polymer; BIW = body-in-white. Source: PNGV (1998). |
subsystems and components do not take into account secondary weight savings that derive from the fact that certain components may be downsized in keeping with the total weight of the vehicle. Examples of candidate subsystems are: wheels, brakes, suspension components, and power trains. If a vehicle is designed from the ground up, secondary weight reductions can be as much as 0.5 lbs for every 1.0 lb of primary weight reduction.
Body System
The baseline vehicle body system weighs approximately 1,100 lbs and is targeted for 50 percent weight reduction. Because the body-in-white (BIW)
(590 lbs) and the closure panels (220 lbs) account for a large fraction of the weight, the PNGV team is concentrating on reducing the weight of these components and has identified weight-saving opportunities of aluminum sheet to be in the range of 50 to 55 percent, or 400 to 450 lb. Competing with aluminum sheet are glass fiber-reinforced polymer composites (GFRP) and carbon fiber-reinforced polymer composites (CFRP). GFRP materials, which may be considered for closure panels, offer only a 25 to 35 percent weight savings. The PNGV materials team has fabricated a BIW from CFRP sheet and sandwich materials that achieves a 68.5 percent weight reduction over the Multimatics baseline vehicle (Multimatics is a Canadian manufacturer of automotive parts). Another alternative is a more efficiently designed steel BIW, which has been demonstrated by the American Iron and Steel Institute ultralight steel auto body project. This approach has the potential of a 20 percent (120 lbs) weight reduction in the BIW structure and a cost reduction of $154. If more efficient design techniques are applied to all alternative-material BIW concepts, the 50 to 55 percent weight savings of aluminum over steel should remain intact.
The U.S. automotive industry has considerable production experience in stamping aluminum closure panels, usually deck lids or hoods, and in many cases aluminum panels have been put into high-volume production, in spite of a sizable cost penalty. In this situation, a 40 to 50 lb weight reduction is considered worthwhile because it keeps an ''overweight" vehicle from being classified in a higher weight class, where it is more difficult for the vehicle to meet the tailpipe emission standards and corporate average fuel economy (CAFE) standards.
As a matter of public record, several aluminum-intensive prototype vehicles have been built outside the PNGV program by the USCAR partners and evaluated for ride, handling, noise, vibration, and harshness, crashworthiness, and production processes, such as stamping, extruding, joining, and painting (Jewett, 1997). Thus, the change to an aluminum-intensive vehicle would not be a major technological challenge because the USCAR partners already have extensive design and manufacturing expertise with this material. The challenge is to develop new processing methods, especially for feedstock materials, so that an aluminum-intensive vehicle can be manufactured as inexpensively as a steel vehicle. Based on a price for aluminum of $1.60/lb (Table 2-5) and average weight savings of 47 percent, the cost penalty of an aluminum BIW is estimated at $400, including incremental manufacturing costs. Current PNGV programs involving direct casting of thin aluminum sheet, which avoids expensive hot-rolling processes, have the potential to reduce the cost of aluminum sheet to $1.00/lb (Table 2-5), which would reduce the BIW cost penalty to $200. With a more efficient design, a 55 percent weight savings may be possible, which would reduce the cost penalty even further.
Recyclability of the major materials of the vehicle is an important requirement. Today 75 percent of the materials of an average vehicle is recycled; PNGV has set a target of 80 percent. The procedures and processes for recycling
Table 2-5 Material Cost Targets
Material |
Current Cost ($/lb) |
Target Cost ($/lb) |
Product Form |
Aluminum |
1.40 to 1.60 |
1.00 |
sheet |
Magnesium |
1.65 |
1.20 |
ingot |
Carbon fiber |
> 8.00 |
3.00 |
fiber |
Aluminum metal-matrix composites |
2.00 |
1.40 |
ingot |
Titanium |
8.00 |
2.00 |
bar, sheet |
Source: Sherman (1998). |
aluminum are already in place, and much of the material is returned to high-value applications.
The cost estimates given above include an allowance of $0.50/lb for the scrap value of aluminum. Given the current process for shredding vehicles and recovering their metal content, techniques will be necessary for separating higher value aluminum sheet from aluminum castings. Programs that could accomplish this are included in the PNGV Materials Roadmap.
In the committee's fourth report, a number of serious obstacles were discussed that would have limited the use of CFRP composite materials in meeting Goal 3 (NRC, 1998a). During the past year, however, some exciting progress has been made in the development of thin (1.0 mm) CFRP sheet and aluminum honeycomb lamellae sandwiched between CFRP layers.
A hybrid material BIW was fabricated from a variety of multilaminate materials, as shown in Figure 2-3. The PNGV BIW weighed 90 kg on a baseline BIW that weighed 285 kg in steel, or a 68.5 percent weight savings. This is significantly better than the 59 percent forecast by the PNGV materials team last year and close to what might be expected from a structural analysis assuming adequate material properties. The reduction was achieved in part by very stiff CFRP lamellae (1.0 mm), which can be formed much like steel into box beams and other more complicated shapes.
In the past, work by the USCAR Automotive Composites Consortium showed that it was difficult to achieve good frontal crash response from polymer-composite front-end structures. Some of these early problems have been overcome. In the PNGV hybrid material BIW (including CFRP thin sheet, sandwich panels, and aluminum front ends), lower cost, extruded or hydro-formed aluminum beams were used in the front-end structure to ensure adequate crash response, which was verified by 30 mph frontal-crash simulations. Finite element analyses showed that static bending and torsional stiffnesses were significantly better than for the baseline steel vehicle and that frequencies of the first bending and torsional modes were shifted to higher values.
The committee considers these results very encouraging, even though there is still much to be learned about (1) composite design techniques, (2) the consistency
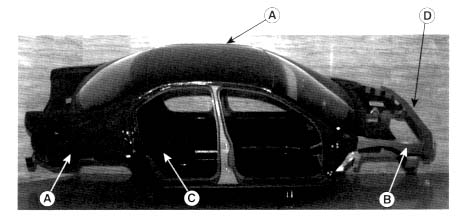
Figure 2-3
Multimatics PNGV hybrid-material body structure. Some selected materials used are as follows: (A): sandwich panel (aramid fiber-reinforced core with carbon/epoxy skins); (B) aluminum sheet metal; (C) sandwich panel (aluminum honeycomb core with carbon/epoxy skins); (D) sandwich panel (aluminum honeycomb core with hybrid carbon/aramid/epoxy skins).
SOURCE: Adapted from Todd (1998) and a photograph given to the committee by USCAR.
of mechanical properties in high production volumes, and (3) the reduction of manufacturing-cycle times. Finally, methods for recycling materials into high-value applications to take advantage of their intrinsic properties, as opposed to using them only as filler, must still be developed.
The major barrier to the intensive use of CFRPs for a Goal 3 vehicle is the high cost of the carbon fibers. As shown in Table 2-5, the cost of carbon fiber must be reduced from $8.00/lb to $3.00/lb. Currently, the cost of a CFRP BIW is much higher than for a steel or aluminum BIW. The committee was pleased to note that an ORNL project has demonstrated the production of carbon fibers by microwave heating, which may have the potential to reduce processing costs by 50 percent or more. Other concepts are being pursued to reduce the cost of precursor materials.
In another project, a lightweight interior has been developed, including lightweight seats, and magnesium frames, door-trim panels, and overhead system, all of which allows a 40 percent mass savings in the interior with a minimal cost penalty.
Also, work continues on lightweight glazing materials (e.g., thin glass and polymers), which offer a potential weight savings of 50 lbs. The major concerns about polymers are abrasion/scratch resistance and cost.
Power Train and Chassis System
The total weight in the power train and chassis subsystems for the baseline vehicle is 1,101 lb and 868 lb, respectively, and the targeted weight savings are 561 lb (50 percent) and 87 lb (10 percent), respectively. Thus, the total targeted weight savings for the two subsystems is 648 lb, whereas the total identified weight savings, based on the PNGV Materials Roadmap (Table 2-4), is 325 lb, a shortfall of 323 lb. Thirteen of the 38 projects in the materials road map (Table 2-4) are directed toward reducing the weight of the power train and chassis, but the committee was apprised that progress has been made in only a few projects, primarily because many of the projects in this category are new. The materials technical team has identified a process for tracking progress in all road-map projects.
Cast aluminum has been used extensively in the power-train subsystem, replacing cast iron over the past two decades in most cylinder heads and intake manifolds and increasingly replacing cast iron in cylinder blocks. This trend is expected to continue. Moreover, magnesium will be used increasingly in the power train, chassis, and body subsystems. The PNGV materials road map includes major initiatives to reduce the costs of feedstock and improve the casting processes for both materials. Progress in the cast light-metals programs includes the creation of a cast light-metal material-property database (CD-ROM) that correlates with cast microstructures, the development of a fiber-optic infrared temperature sensor for on-line process control, and the development and validation of a simulation model to predict the monotonic tensile properties of cast metals.
Studies to improve the machinability of magnesium castings and to develop a low-cost, high-temperature alloy are also under way. Improved processes for recycling magnesium will have to be developed.
Aluminum metal-matrix composite applications in chassis and power-train subsystems account for only 30 to 50 lb. The major hurdles to developing applications of this material are feedstock costs (Table 2-5) and the development of a reliable process for fabricating the composites. A low-cost powder-metal process is under development, but no progress was reported for this period.
The applications for titanium are in the chassis (40 lb potential savings) and power-train (10 lb potential savings) subsystems. The components of interest are springs, piston pins, connecting rods, and engine valves. A program designed to lower the cost of titanium feedstock has been initiated during the past year.
Program Assessment and Plans
Body System
In the past year, aluminum sheet has been the leading structural-material candidate for the Goal 3-vehicle technology-selection process because (1) the
demonstrated weight savings (50 percent) meets, and might exceed, the Goal 3 target, (2) it has the best chance of meeting the affordable cost target, (3) the USCAR partners have an extensive knowledge base for the design and fabrication of components from aluminum sheet, (4) a supplier infrastructure for ore, feedstock, and semifinished materials already exists, (5) existing stamping facilities for steel can be used for aluminum without major modifications, and (6) considering all of the alternate materials, aluminum is the most recyclable alternative and would cause the fewest disruptions in the existing recycling industry for steel-bodied automobiles.
A major CRADA has been initiated between Reynolds Metals, LANL, and the USAMP to reduce the cost of aluminum sheet through the development of a thin-slab (less than 1 in thick) continuous-casting process to replace the more costly ingot-based process used today. During the past year, automotive sheet was produced from direct-cast thin slabs that demonstrated excellent formability. Another program to develop low-cost, non-heat-treatable alloys competitive with the 6000 series aluminum alloys is also under way and is about to initiate stamping trials. However, additional developments beyond continuous casting of sheet will be necessary to reduce the current manufacturing and assembly cost penalty of parts fabricated from aluminum sheet. The added costs are associated with differences in spring-back characteristics, die maintenance, joining technologies, and recycling costs.
During the past year, the fabrication of a hybrid material, CFRP BIW, from thin sheet and sandwich materials, as well as some aluminum extrusions, demonstrated an impressive 68.5 percent weight savings over a steel baseline vehicle. Even though this weight savings is impressive, CFRP technology must be viewed as a long-term alternative to aluminum. The cost of carbon fiber and a short cycle-time fabrication process are major issues that probably cannot be resolved in time to support Goal 3, year-2000 concept vehicles. Nevertheless, the promising development of CFRPs should be continued with applications targeted beyond Goal 3. An R&D program is in place at ONRL to produce low-cost carbon fiber by microwave processing. Future programs should concentrate on reducing the cost to $3/lb, developing a process for mass producing components in thin sections, acquiring a deeper understanding of reliable design for complex loading conditions, and developing high-value applications for the recycled material.
The injection molding of GFRPs being investigated by DaimlerChrysler and the Automotive Composites Consortium (thermoset resins) offers potential weight savings of 25 to 35 percent, which is considerably less than aluminum or CFRP. With this technology, the Goal 3 target would be missed by a sizeable margin. However, for Goal 1 and Goal 2 applications, GFRP may compete effectively on a cost basis with aluminum for body panels and certain structural applications because large integrated parts can be made and lower cost dies can be used, thus reducing assembly and manufacturing costs. Nevertheless, the extensive design and production experience with aluminum for body panels and structural
applications, as well as the available supplier infrastructure, gives aluminum an edge in the near term.
Power Train and Chassis System
Several important R&D studies are in place to reduce the costs and improve the properties of aluminum and magnesium castings, including sand casting, semipermanent mold casting, squeeze casting, and high-pressure die casting. Progress in this area was discussed in the preceding section.
Also, the committee was pleased to see that programs have been initiated with titanium and aluminum metal-matrix composites that will help to reduce feedstock and processing costs. In the coming year, gerotors (rotating part in an air-conditioning compressor) and timing sprockets are expected to be fabricated by the low-cost powder-metal process technology for metal-matrix composites. Other new projects that will be initiated include low-cost magnesium, high-temperature magnesium, and low-cost cast metal-matrix composites.
The committee noted that there was minimal discussion of progress in this area, probably because many of the programs are in the early stages of development.
Recommendations
Recommendation. The committee continues to believe that fabricated aluminum sheet should be the primary candidate for the body-in-white and closure panels for the year-2000 concept vehicles. The development of the low-cost continuous-casting process of aluminum sheet should be given a high priority in terms of resources and technical support. In addition, low-cost processes to overcome the cost penalty associated with the manufacturing and assembly of parts from aluminum sheet should be pursued.
Recommendation. The best long-term candidate—beyond year 2000—is the hybrid-material body-in-white, featuring thin carbon fiber-reinforced polymer sheet, sandwich panels, and aluminum front ends. The development program for low-cost carbon fiber should be continued for longer term applications beyond Goal 3. A low-cycle-time process and better recycling methods should also be pursued.
Recommendation. The PNGV materials technical team should endeavor to decrease the gap between the PNGV targets for weight savings and the actual identified weight savings for the power-train and chassis subsystems.